These high performance linear translation stages and rotary precision positioning stages are designed for high load / high duty cycle applications in industrial automation. Different bearings and guiding systems are available, including recirculating ball bearings, crossed roller bearings and air bearings. For maximum accuracy, duty cycle and life time, linear motors and frictionless, wear-free, air bearings are recommended. Linear stages can be combined to XY sand XYZ systems – and planar XY stages and XYZ gantry systems are also available for high performance automation, test and inspection tasks.
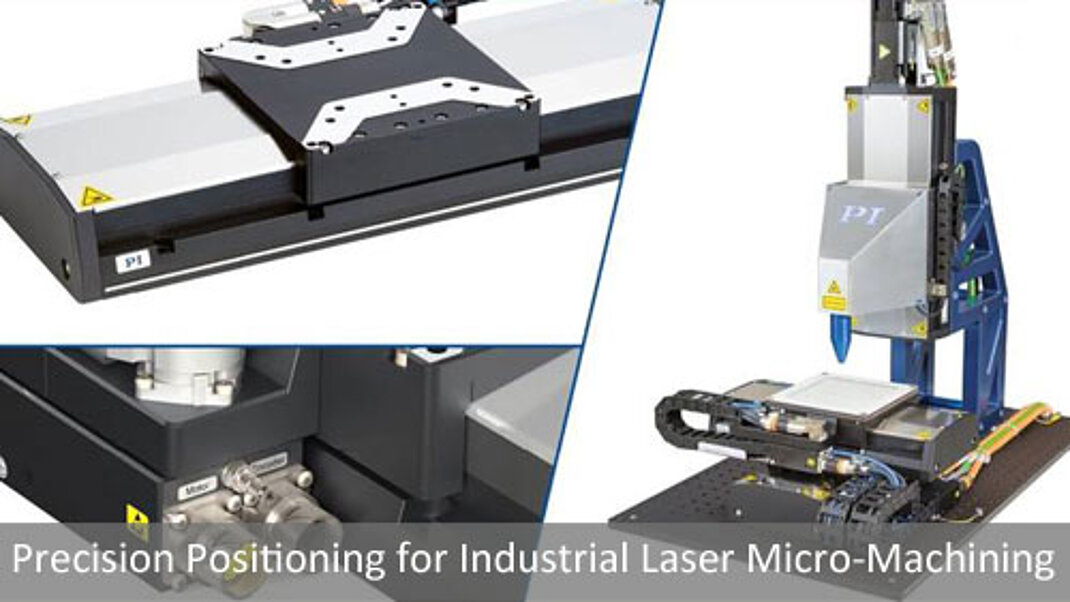
High Speed 3-phase Linear Motor Driven Stages: Single Axis and XY Planar, Mechanical Bearings and Air Bearings
High Load Ball Screw Linear Stages for Industrial Automation
1 to 600nm Resolution, up to 813mm Travel
These stages are equipped with brushless motors for high duty cycle applications. Ball-screw drives provide higher push/pull forces than linear motors and can work in vertical orientation without the need for counterbalance. Position feedback is provided by rotary encoders, linear incremental encoders with sine/cosine output or absolute encoders (no need for homing).
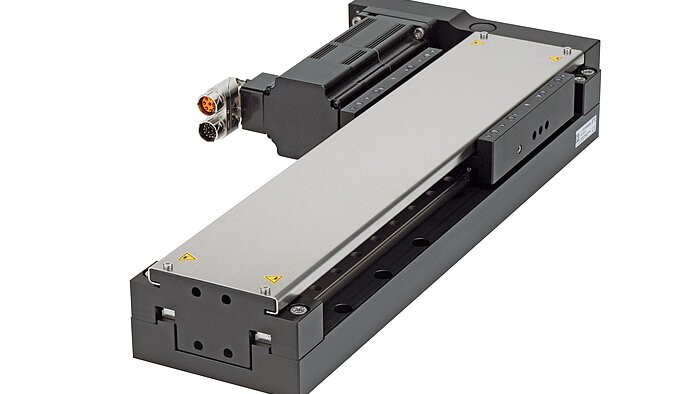
L-812 High Load Linear Module
Cost Effective, Servo & Stepper Motor
- 114 - 610mm (4.5”-24”) travel
- 3µm min. inc. motion
- 5µm bidirectional repeatability
- 100mm/sec max. velocity
- 377N push/pull force
- Absolute encoder option
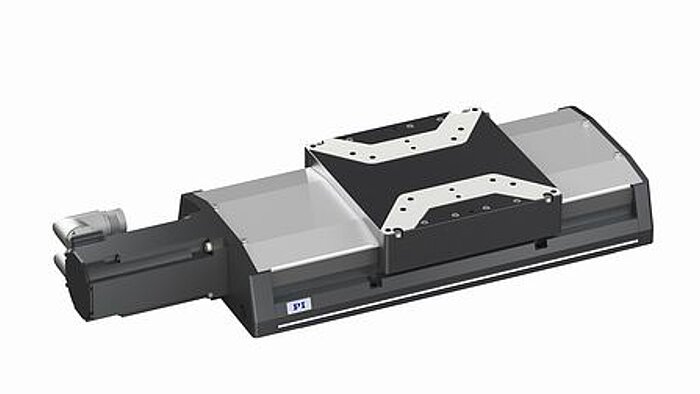
L-417 High Load Linear Stage
Ball Screw Drive, 450N Load
- 102 - 813mm (4”-32”) travel
- 0.05µm to 1µm min. inc. motion
- 1nm to 600nm encoder res.
- 350mm/sec max. velocity
- 700N push/pull force
- Linear encoder option
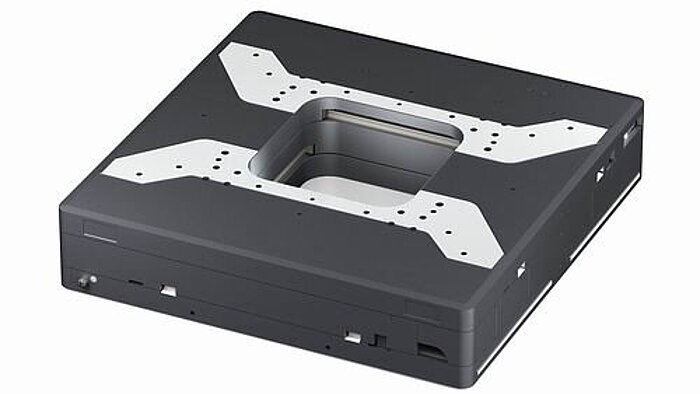
L-738 Integrated High Load Precision XY Stage, 4" Travel, Aperture
Ballscrew, Stepper & Servo Motor
- 4” XY travel (102mm)
- 0.1µm min. inc. motion
- 0.1 to 0.001µm sensor resolution
- 90mm/sec max. velocity
- 20kg load
- Linear encoder option
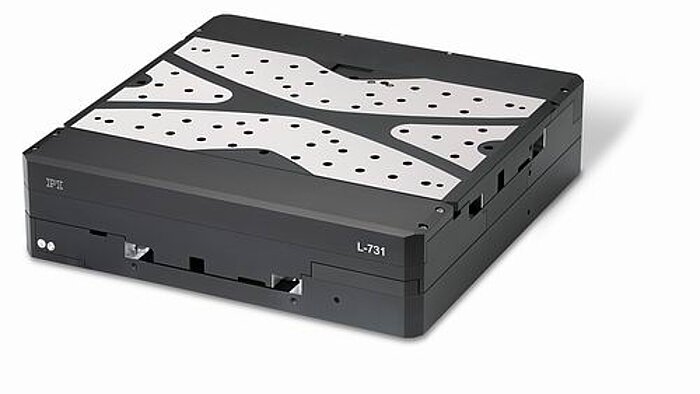
L-731 Integrated High Load Precision XY Stage, 8" Travel
Ballscrew, Stepper & Servo Motor
- 8” XY travel (205mm)
- 0.1µm min. inc. motion
- 0.1 to 0.001µm sensor resolution
- 90mm/sec max. velocity
- 20kg load
- Linear encoder option
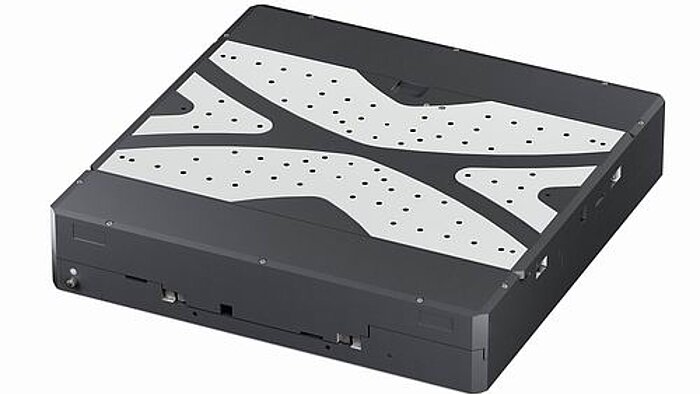
L-741 Integrated High Load Precision XY Stage, 12" Travel
Ballscrew, Stepper & Servo Motor
- 12” XY travel (305mm)
- 0.1µm min. inc. motion
- 0.1 to 0.001µm sensor resolution
- 90mm/sec max. velocity
- 20kg load
- Linear encoder option
Compact & Medium-Sized Linear Motor Stages for Precision Automation
<1 to 20nm Resolution, up to 1m/sec
These compact and mid-sized linear motor stages provide high speed and very long lifetime – ideal for 24/7 precision automation with smaller loads. Frictionless 3-phase motors provide high velocity to 1m/sec, 2g acceleration and zero wear. Crossed roller bearings provide excellent straightness and flatness with minimized runout. Position feedback is provided by linear encoders with sine/cosine output or optional absolute encoders (no need for homing).
V-141: This economical stage family is available with 40mm, 60mm and 100mm travel. The 100mm variant features a high-force motor.
V-571: The V-571 stage comes with a 1nm absolute-measuring encoder for ultra-high precision.
V-574: The V-574 family provides extremely high geometric precision (pitch/roll) and is equipped with a 1nm absolute-measuring encoder or a sin/cos analog encoder with 4µm pitch.
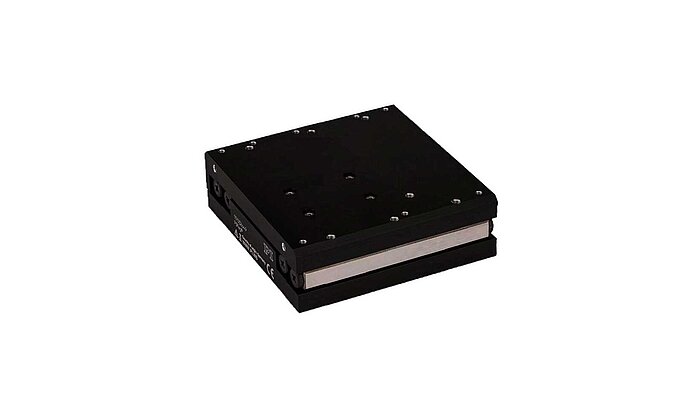
V-141 Low-Cost Linear Motor Stage
Compact, High Force, 80mm Width
40, 60, and 100mm travel
120nm bidirectional repeatability
2µm accuracy
1m/sec max. velocity
Up to 45N push/pull force
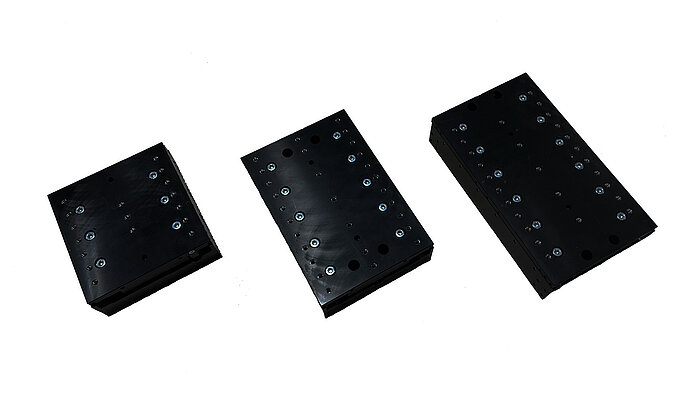
V-571 Compact Linear Motor Stage
95mm Stage Width
- 25/50/75/100mm travel
- 1µm straightness/100mm
- 120nm bidirectional repeatability
- 1nm absolute encoder resolution
- 0.5m/sec max. velocity
- 21N push/pull force
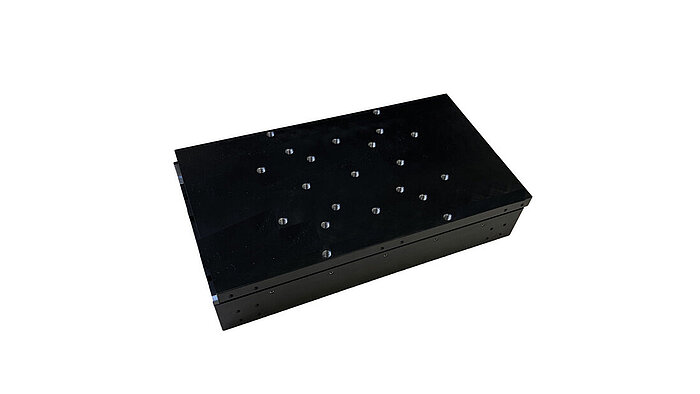
V-572 Linear Motor Stage
130mm Stage Width
- 60/110/150/210mm travel
- 0.8 - 1.5µm straightness
- 160nm bidirectional repeatability
- 1nm absolute encoder resolution
- 0.5m/sec max. velocity
- 60N push/pull force
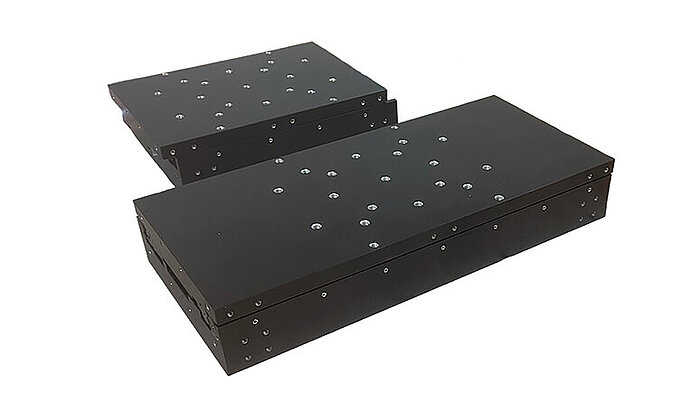
V-574 Linear Motor Stage
160mm Stage Width
- 1 - 1.5µm straightness
- 60/130/230mm travel
- 80nm bidirectional repeatability
- 1nm absolute encoder resolution
- 1m/sec max. velocity
- 58N push/pull force
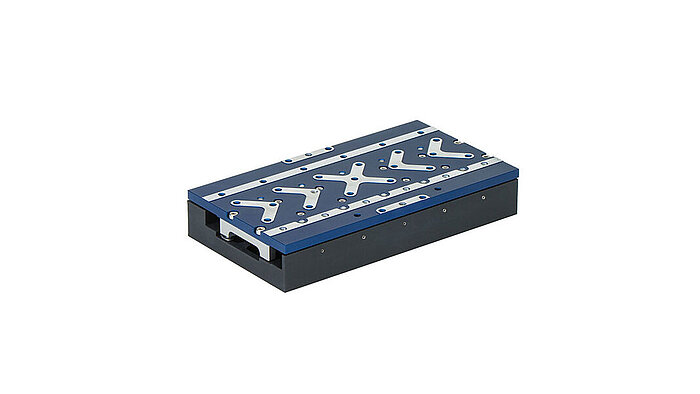
V-508 Linear Motor Stage
Compact, High End Sensor Option
- 80/170/250mm travel
- 1 to 20nm min. inc. motion
- 0.2-10nm linear encoder resolution
- 0.7m/sec max. velocity
- 14N push/pull force
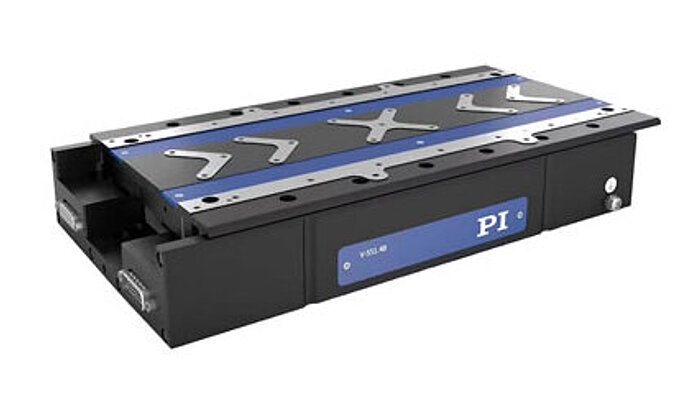
V-551 Linear Motor Stage
Absolute Encoder Option
- 60/130/230mm travel
- 0.5 to 2nm min. incremental motion
- 0.2 to 1nm linear encoder res.
- 0.5m/sec max. velocity
- 180N push/pull force
High Speed Linear Motor Stages for Industrial Automation
1 to 10nm Resolution, up to 1200mm Travel, Recirculating Ball Bearings and Air Bearings
Linear motor stages provide very high speed and very long lifetime. They are ideal for precision automation applications. Frictionless 3-phase motors and voice coil motors provide the driving force. Stages are equipped with self lubricating high-load recirculating ball bearings or frictionless air bearings. Position feedback is provided by linear encoders with sine/cosine output or optional absolute encoders (no need for homing).
The linear modules use a single guiding rail and are well suited as high performance actuators and can form the basis of a gantry system.
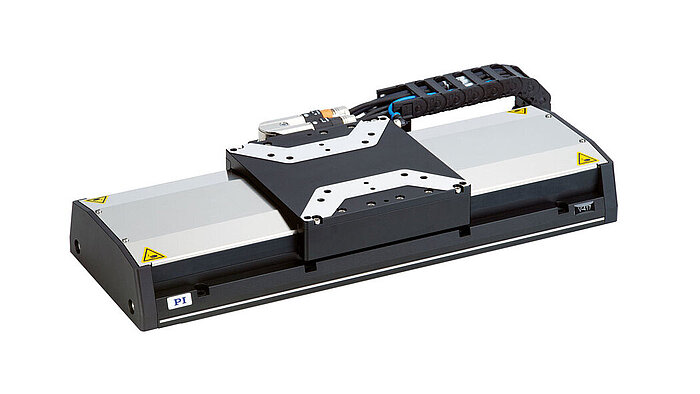
V-412 High Speed Linear Stage
Linear Motor 400N Load
- 102 - 610mm (4”-24”) travel
- 5nm to 10nm min. inc. motion
- 1nm encoder res.
- 2m/sec max. velocity
- 151N peak force
- Absolute encoder option
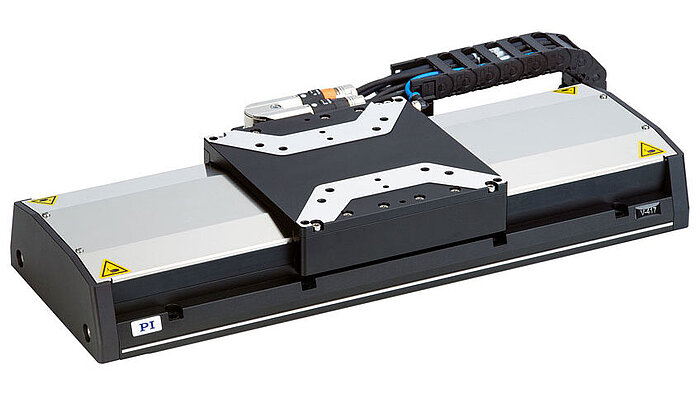
V-417 High Speed Linear Stage
Linear Motor, 450N Load
- 102 - 813mm (4”-32”) travel
- 5nm to 10nm min. inc. motion
- 1nm encoder res.
- 2m/sec max. velocity
- 300N peak force
- Absolute encoder option
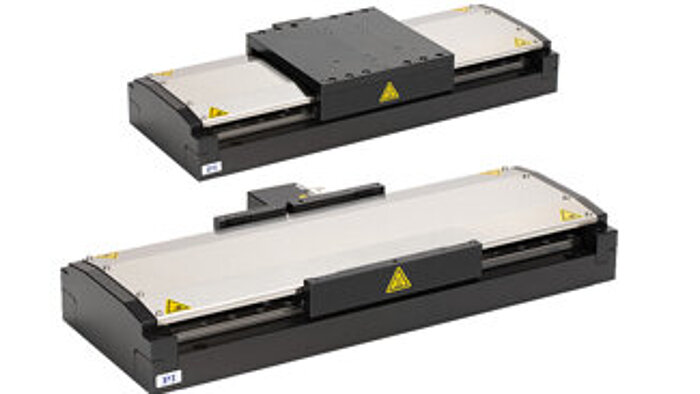
V-817 Economical High Performance Stage
Linear Motor, 3m/sec 600N Load
- 204 - 813mm (8”-32”) travel
- 10nm min. inc. motion
- <1nm encoder res.
- 3m/sec max. velocity
- 300N peak force
- Excellent value for precision automation
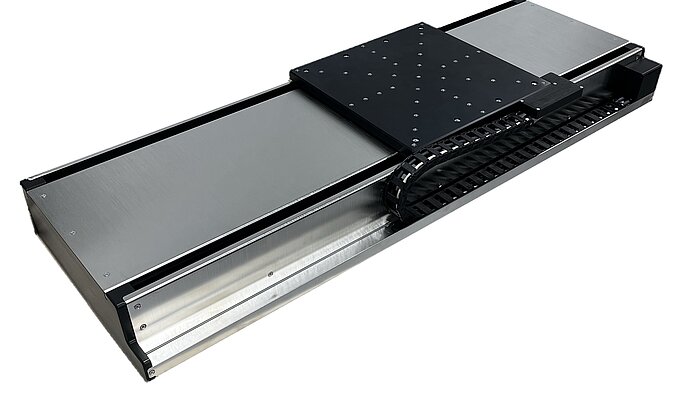
V-827 Linear Motor Stage
Wide Base, High Load, to 1m Travel
300/500/750/1000mm travel
150nm bidirectional repeatability
1nm absolute encoder res.
2m/sec max. velocity
720N push/pull force
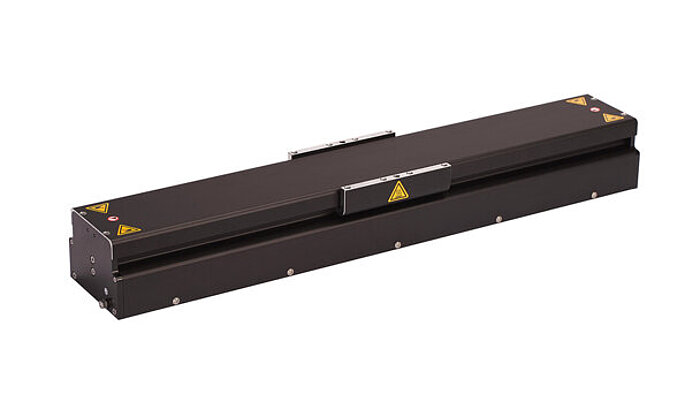
V-855 High-Speed Linear Module
Linear Motor, 4m/sec 600N Load
- 200 - 800mm travel
- 0.1µm min. inc. motion
- <1nm encoder res.
- 4m/sec max. velocity
- 90N peak force
- Excellent value for precision automation
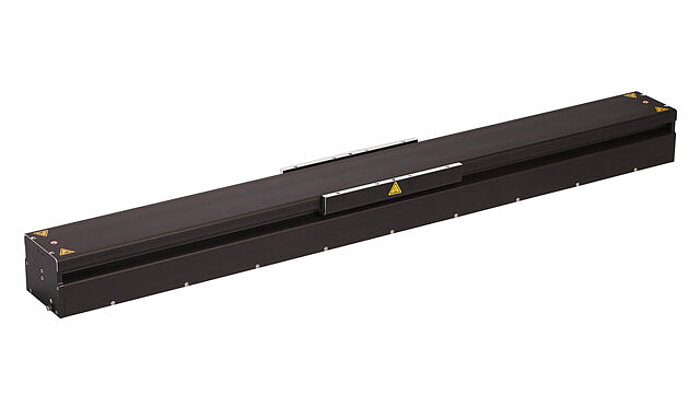
V-857 High-Speed Linear Module
Linear Motor, 5m/sec 1000N Load
- 400 - 800mm travel
- 0.1µm min. inc. motion
- <1nm encoder res.
- 5m/sec max. velocity
- 420N peak force
- Excellent value for precision automation
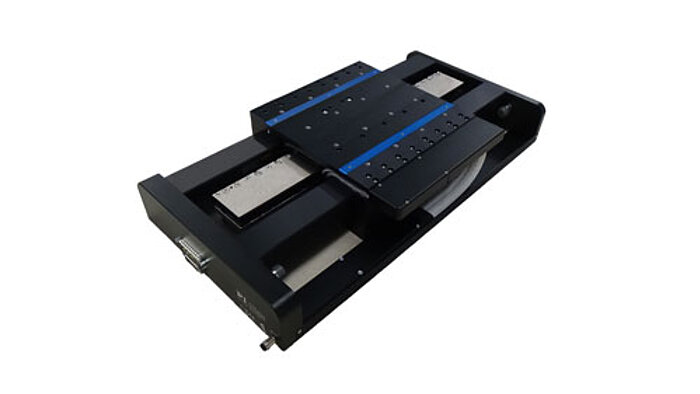
A-123 PIglide Air Bearing Stage
Large, Travel to 30”
- 2/4/6/10/14/20/30” travel
- 10kg load
- 1nm resolution, abs/enc option
- 210x210mm table; 85mm height
- 1m/sec max. velocity
- 3g max. acceleration
XY Planar High Speed, Linear Motor Stages for Industrial Automation
Mechanical Bearings and Air Bearings
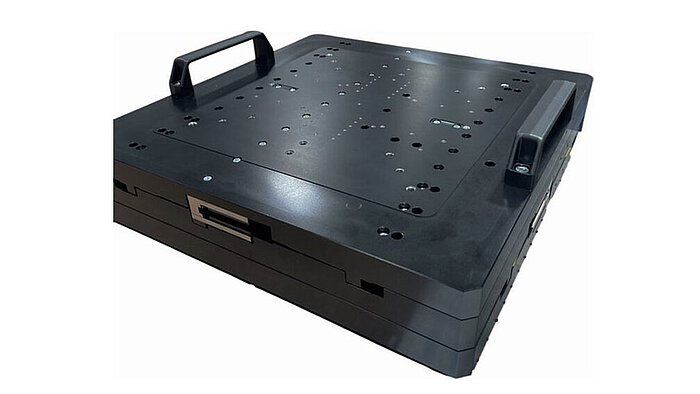
V-781 Integrated High-Speed Precision XY Stage Family
4”/8”/12”, Linear Motor & Encoder
- 4”/8”/12” XY travel (110 - 310mm)
- 0.01µm min. inc. motion
- 0.001µm sensor resolution
- 1m/sec max. velocity
- 50kg load
- Linear motor, linear encoder
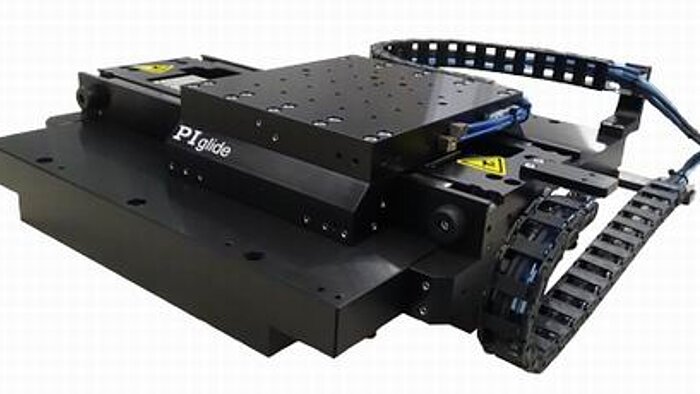
A-311 Planar Air Bearing Stage
Compact, Affordable, Al Base
- 50x50mm to 300x400mm travel
- 15kg load
- 1nm resolution
- Light weight, AL base
- Dynamic error mapping
- 2m/sec / 2.7g max. acceleration
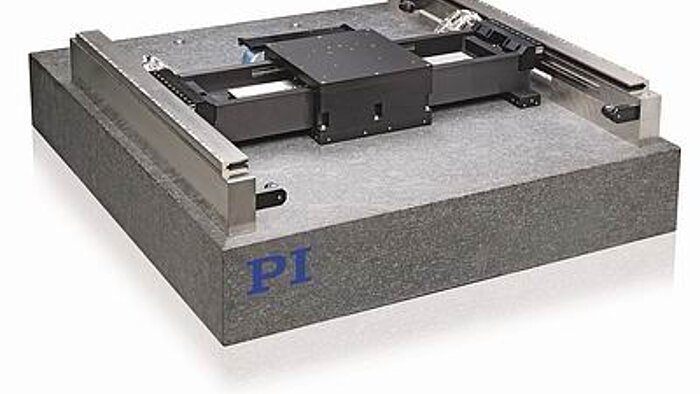
A-322 Planar Air Bearing Stage
3&4-Motor Designs, Granite Base
- 3 Models: Base, Plus, Ultra
- 500x1000mm max. travel
- 15kg load
- 1nm resolution
- Active yaw control flex coupling
- Dynamic error mapping
- 1m/sec / 2g max. acceleration
PI provides different drive technologies to match the application as best as possible.
Worm gear drives provide high holding torque as well as self locking capabilities, direct drive torque motors provide high acceleration and speed, and air bearings provide the highest possible geometric performance along with zero friction and wear.
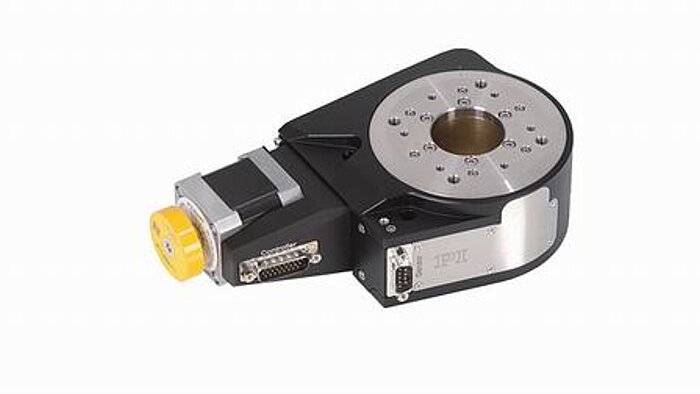
L-611 Precision Rotary Stage
Worm Gear, Servo / Stepper
- 35mm aperture, 80mm turn table
- 0.7µrad min. inc. motion
- 50-200°/sec max. velocity
- 10kg load
- Direct encoder option
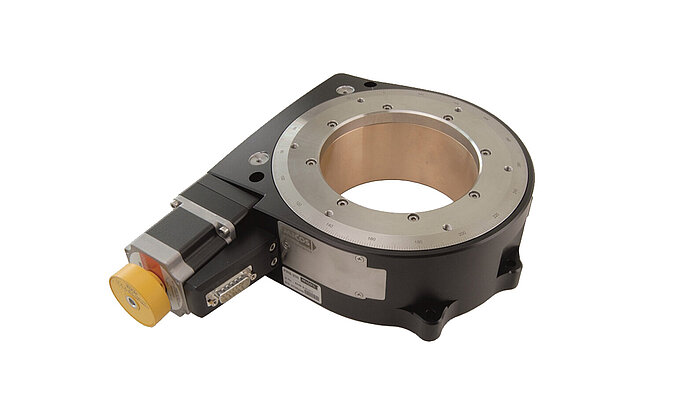
PRS-200 Precision Rotary Stage
Worm Gear, Servo / Stepper
- 120mm aperture, 200mm turn table
- 0.5 – 8.7µrad min. inc. motion
- 35-75°/sec max. velocity
- 50kg load
- Direct encoder option
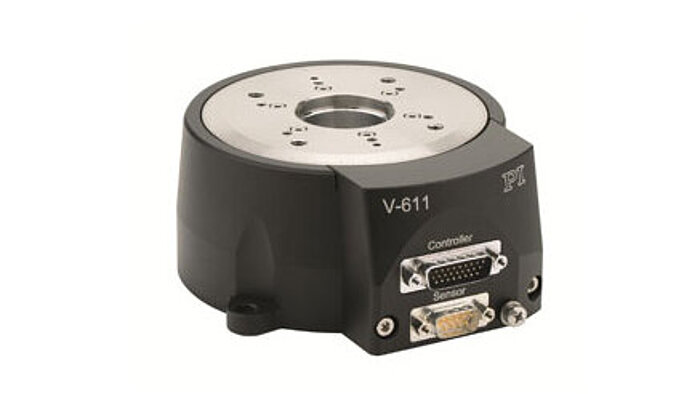
V-611 High Precision Rotation Stage
Direct Drive, Absolute Encoder Option
- 35mm aperture, 100mm turn table
- 1µrad min. inc. motion
- 2880°/sec max. velocity
- 10kg load
- Torque motor
- Sine/cosine or absolute encoder
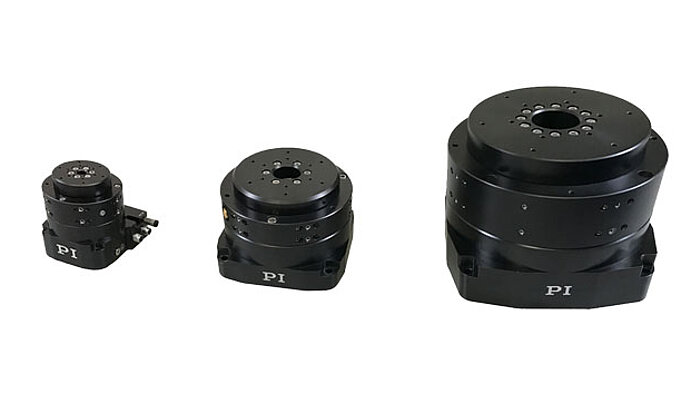
A-621 - A-627 Air Bearing Rotary Stages
Direct Drive, High Load
- 2/4/6/8/12” table diameter
- 13 to 420kg load
- 0.008µrad max. resolution
- 40 to 100nm flatness
- 500 to 2500 RPM max.
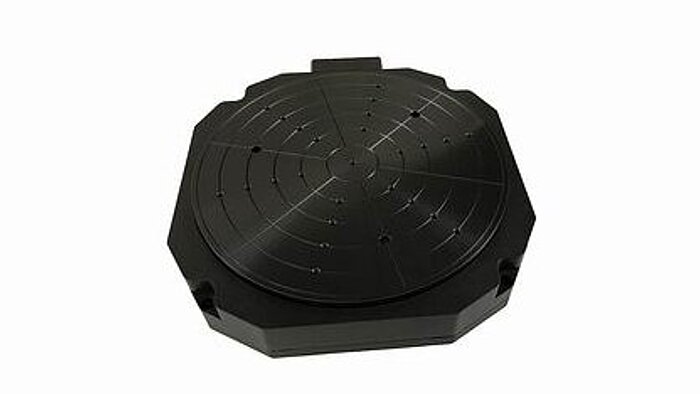
A-634 – A-638 Air Bearing Rotary Stages
Low Profile, Large Diameter
- 6/8/14” table diameter
- 20/32/60/120kg load capacity
- 0.03µrad max. resolution
- <100nm eccentricity & flatness
- 500 RPM max.
- Self-locking option at rest
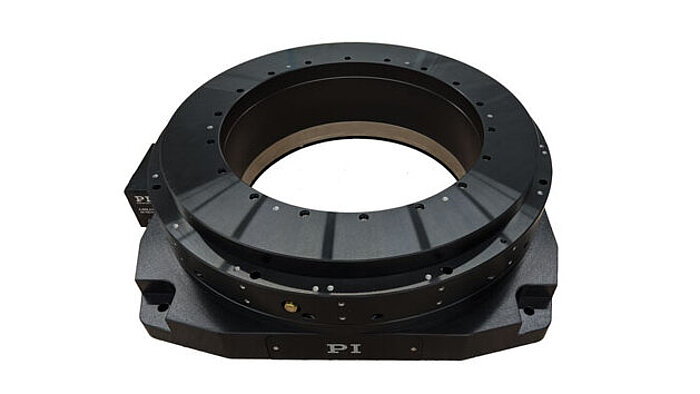
A-688 Air Bearing Rotary Stage
Large Clear Aperture
- ⌀260mm clear aperture
- 77kg load capacity
- 0.0015µrad max. resolution
- 500 RPM max.
- Flatness/Eccentricity <175/300nm
- Wobble: < 1µrad
- Direct drive
PI offers rack-mount and modular motion controllers based on ACS hardware. The ACS modular system is organized in three layers: User interfaces (software), motion controllers, and drive modules.
The motion controller communicates with the host software and manages profile generation, trajectory, macros, diagnostics, etc. Position commands are sent to the universal drive modules (third level) via an EtherCAT real-time network. Drive modules include the digital servo processor (DSP) and actuate the motors, handle the feedback devices, manage the I/Os, and analyze the sensor signals for closed-loop positioning control.
Patented features, such as NanoPWM, enable dynamic current control ranges of >100,000:1, resulting in nanometer level tracking accuracy (e.g. for wafer scanning) and standstill jitter of sub-nanometer in metrology applications.
Extensive trigger functionality facilitate laser applications and inspection, and an integrated 3-DOF error compensation and yaw compensation for gantry solutions satisfy the highest demands on accuracy.
The proprietary Servo-Boost algorithm increases robustness, minimizing the effect of external disturbances in real time, while simplifying tuning and optimizing the performance and settling with changing loads.
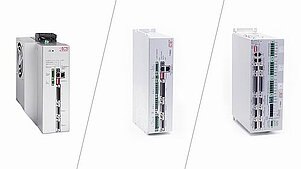
PI provides multi-axis solutions, such as gantries, parallel kinematics and engineered automation sub-systems. Our engineers have access to diverse driving and guiding technologies, spanning from electromagnetic to piezoceramic and from mag-lev to air bearings. They also have experience selecting the right technology for each individual application. Often an adaptation of existing technologies/products will suffice to solve a problem. However, experience along with detailed knowledge and PI’s significant R&D investment in new technologies enables our engineers to take unique approaches.
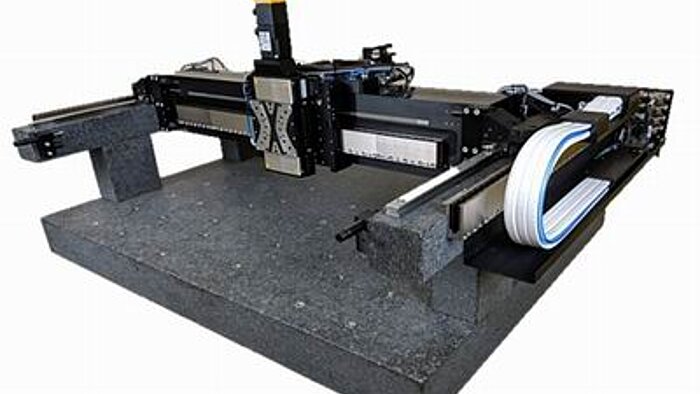
A-341 Hybrid XY / XYZ Gantry Stage
Air Bearings & Linear Bearings, Linear Motors
- 300x300 to 500x1000mm XY travel
- 10kg load
Absolute encoders, 1nm resolution
- Z-Stage options: linear motors or ball screws
- Dynamic error mapping
- 2m/sec max velocity (cross axis)
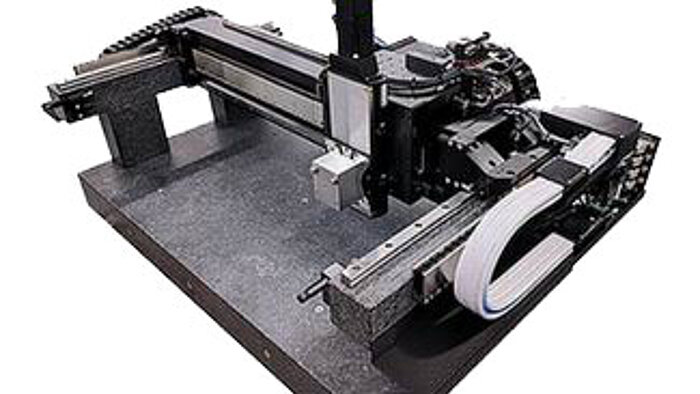
A-351 Overhead XY / XYZ Gantry Stage
Linear Bearings, Linear Motors
- 300x300 to 500x1000mm XY travel
- 20kg load
Absolute encoders, 1nm resolution
- Z-Stage options: linear motors or ball screws
- Dynamic error mapping
- 2m/sec max velocity (cross axis)
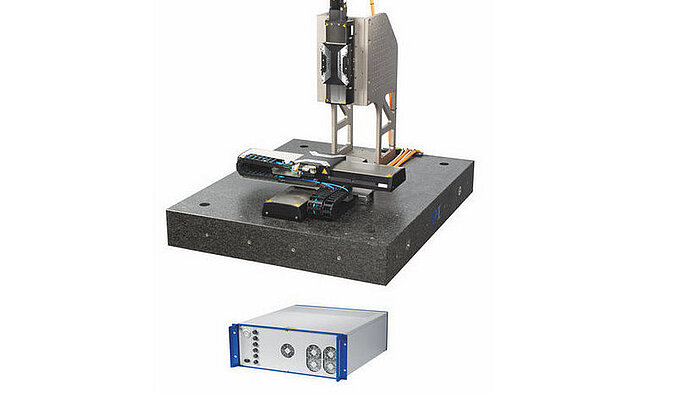
X-417 Scalable Multi-Axis System
Flexible, Fast Delivery
- 204x204 to 407x407mm XY travel
- 20kg load
- Absolute encoders, 1nm resolution
- 102mm Z-Stage travel
- Powerful EtherCat Controller
- 2m/sec max velocity
Fast and precise motorized positioning stages play a major role in the accuracy and throughput of modern laser micro-machining and processing applications. The performance of the motion control system is crucial for the quality of the machined parts. The video shows an automation platform for high dynamic laser processing of small geometries. The multi-axis system is based on the advanced family of L-4xx and V-4xx stages linear stages. A highly dynamic XY-stack of V-417 stages with direct drive linear motors moves the workpiece in the X-Y plane.
The vertical distance of the laser objective can be controlled by a robust L-412/L-417 screw-drive servo motor stage with a holding brake. To address the needs of machine builders the high performance stages are equipped with reference edges to support the alignment in the machine, side seals for debris protection and robust industrial connectors for flexible cable exit. Different encoder variants including absolute-measuring sensors offer nanometer resolution. The automation platform can be controlled by an EtherCAT based ACS motion control module for optimum synchronization of the axes and simultaneous control of the laser.