Direct-drive, linear motor stages and actuators provide high performance, speed and acceleration over large travel ranges. Direct-drive linear motors are usually based on the electrodynamic (magnetic) principle, but piezoelectric direct-drive motors are another option. These motors are usually based on the electrodynamic (magnetic) principle, but piezoelectric direct-drive motors are another option. Due to the lack of friction, very good resolution and repeatability is feasible and the lifetime of the direct drive motors is not limited by wear and tear. Linear motor stages are often used in industrial automation applications where throughput and speed are crucial. PI linear motor direct-drive stages are available with ironless (no cogging) and ironcore (higher force) 3-phase motors and voice coil drives (shorter travel ranges). Optical linear incremental encoders or optical linear absolute encoders are integrated to provide position feedback. Mechanical bearings and air bearings for ultra-high precision applications are available. PI also offers Direct-drive rotary stages.
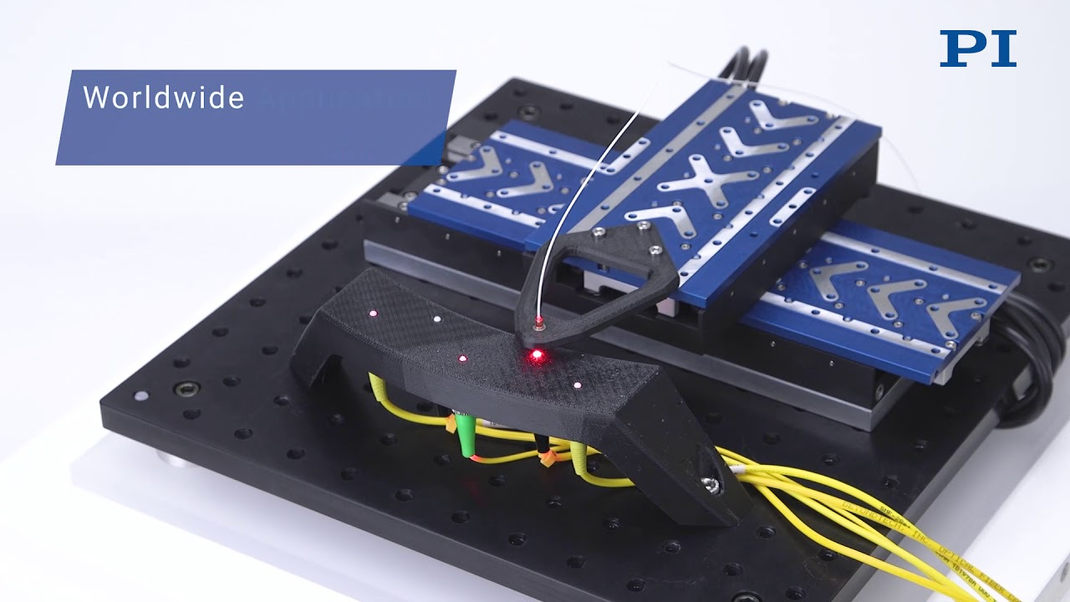
When the highest geometrical performance is required, linear motor stages with air bearings are recommended.
Read article on performance of linear motor stages.
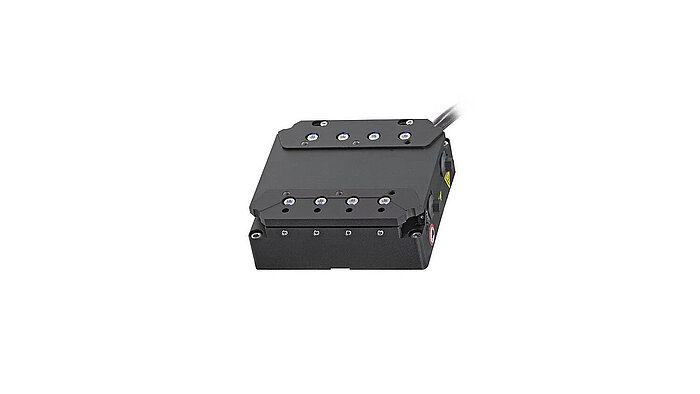
V-308 Fast Scanning Stage
Integrated Counterbalance
- 7mm motion
- Voice coil linear motor
- Adjustable Z-counterbalance
- Millisecond settling time
- 1nm sensor resolution
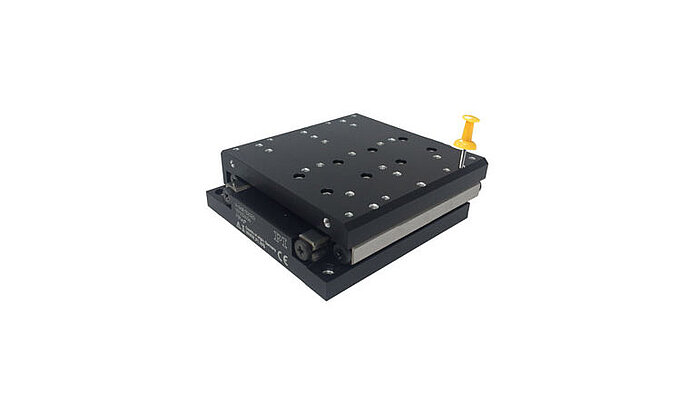
V-408 Low Cost Linear Motor Stage
Compact, High Force
- 25 and 50mm travel
- 20nm min. incremental motion
- 10nm linear encoder resolution
- 0.7m/sec max. velocity
- 14N push/pull force
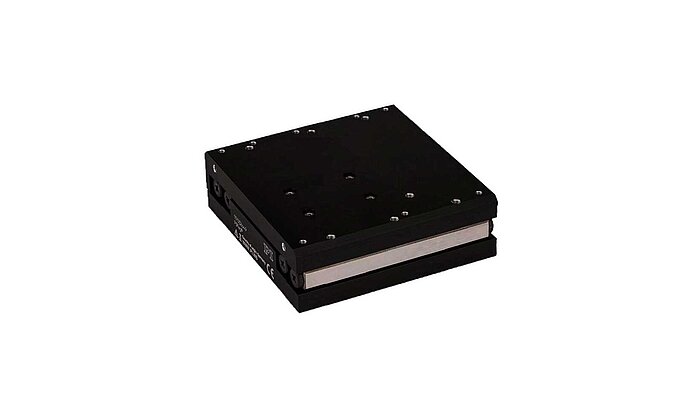
V-141 Low-Cost Linear Motor Stage
Compact, High Force, 80mm Width
40, 60, and 100mm travel
120nm bidirectional repeatability
2µm accuracy
1m/sec max. velocity
Up to 45N push/pull force
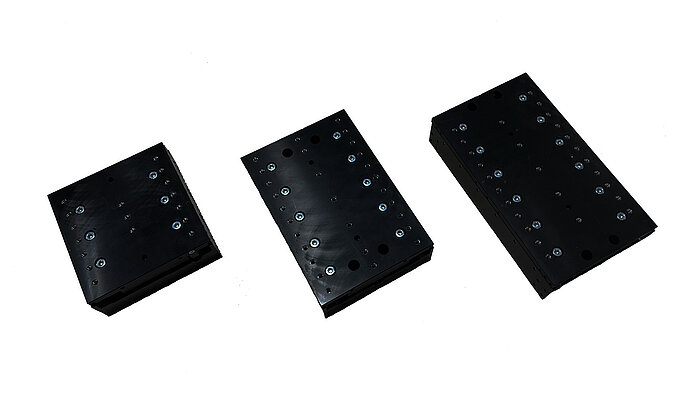
V-571 Compact Linear Motor Stage
95mm Stage Width
- 25/50/75/100mm travel
- 1µm straightness/100mm
- 120nm bidirectional repeatability
- 1nm absolute encoder resolution
- 0.5m/sec max. velocity
- 21N push/pull force
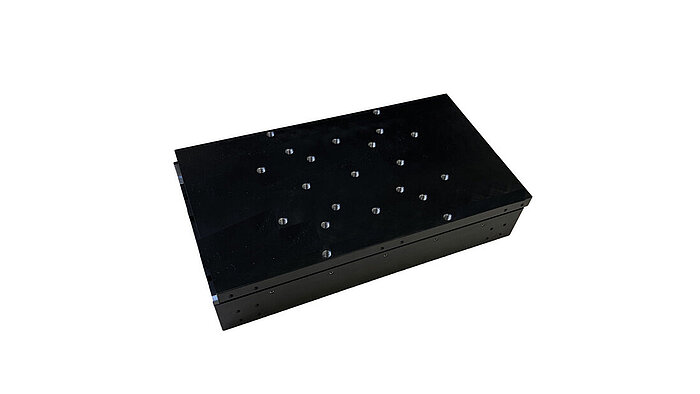
V-572 Linear Motor Stage
130mm Stage Width
- 60/110/150/210mm travel
- 0.8 - 1.5µm straightness
- 160nm bidirectional repeatability
- 1nm absolute encoder resolution
- 0.5m/sec max. velocity
- 60N push/pull force
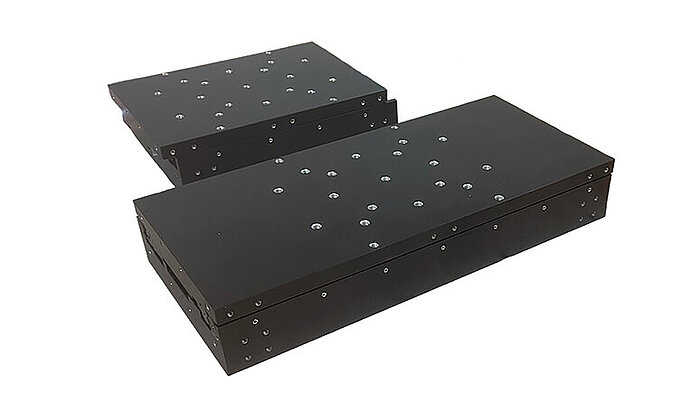
V-574 Linear Motor Stage
160mm Stage Width
- 1 - 1.5µm straightness
- 60/130/230mm travel
- 80nm bidirectional repeatability
- 1nm absolute encoder resolution
- 1m/sec max. velocity
- 58N push/pull force
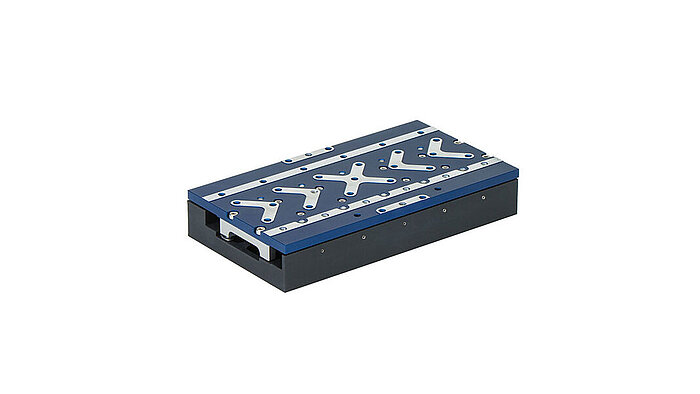
V-508 Linear Motor Stage
Compact, High End Sensor Option
- 80/170/250mm travel
- 1 to 20nm min. inc. motion
- 0.2-10nm linear encoder resolution
- 0.7m/sec max. velocity
- 14N push/pull force
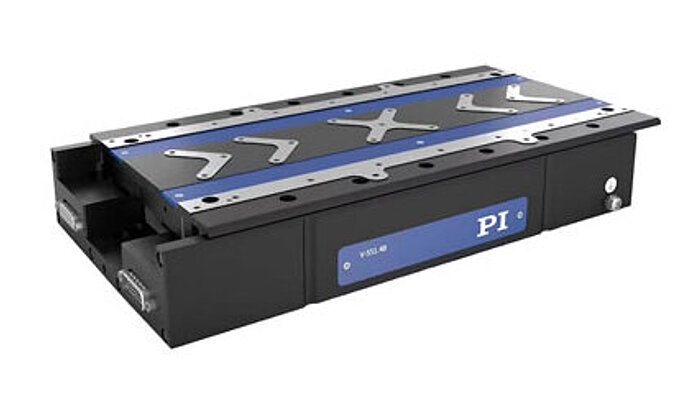
V-551 Linear Motor Stage
Absolute Encoder Option
- 60/130/230mm travel
- 0.5 to 2nm min. incremental motion
- 0.2 to 1nm linear encoder res.
- 0.5m/sec max. velocity
- 180N push/pull force
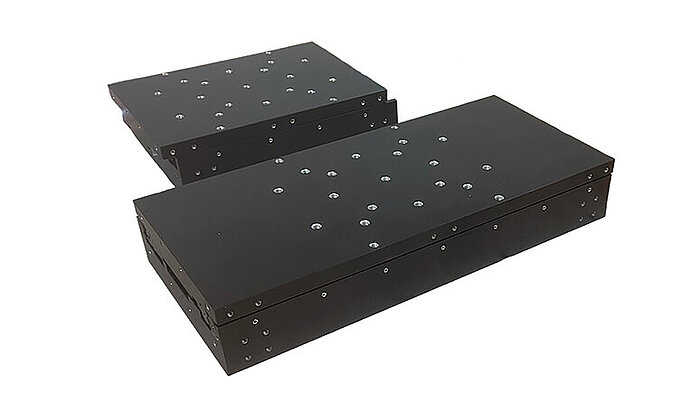
V-574 Linear Motor Stage
160mm Stage Width
- 1 - 1.5µm straightness
- 60/130/230mm travel
- 80nm bidirectional repeatability
- 1nm absolute encoder resolution
- 1m/sec max. velocity
- 58N push/pull force
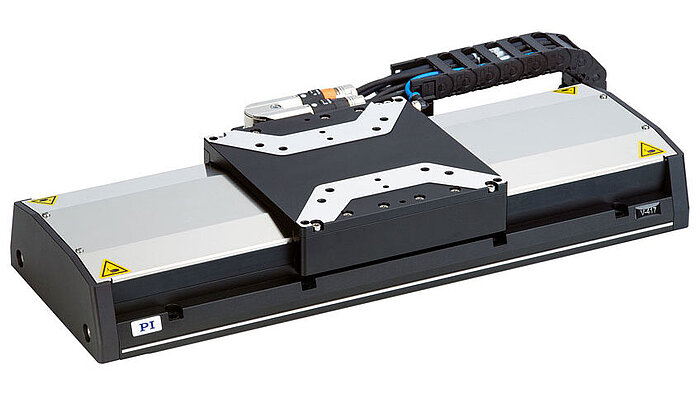
V-417 High Speed Linear Stage
Linear Motor, 450N Load
- 102 - 813mm (4”-32”) travel
- 5nm to 10nm min. inc. motion
- 1nm encoder res.
- 2m/sec max. velocity
- 300N peak force
- Absolute encoder option
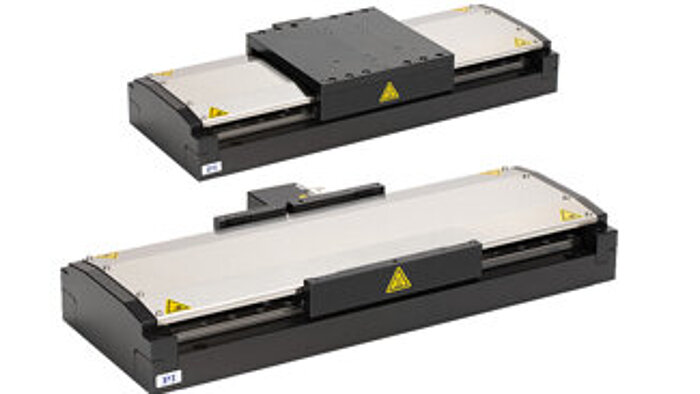
V-817 Economical High Performance Stage
Linear Motor, 3m/sec 600N Load
- 204 - 813mm (8”-32”) travel
- 10nm min. inc. motion
- <1nm encoder res.
- 3m/sec max. velocity
- 300N peak force
- Excellent value for precision automation
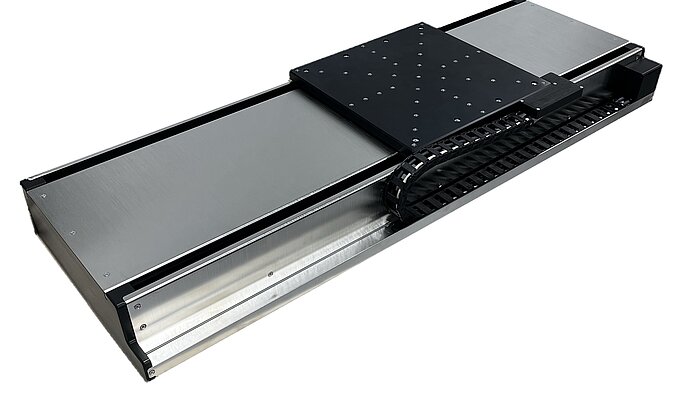
V-827 Linear Motor Stage
Wide Base, High Load, to 1m Travel
300/500/750/1000mm travel
150nm bidirectional repeatability
1nm absolute encoder res.
2m/sec max. velocity
720N push/pull force
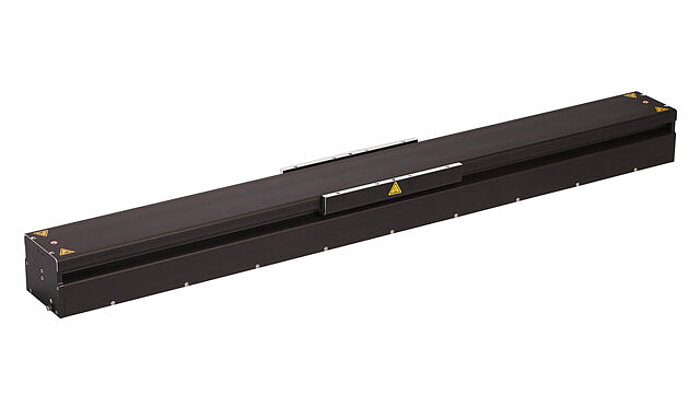
V-857 High-Speed Linear Module
Linear Motor, 5m/sec 1000N Load
- 400 - 800mm travel
- 0.1µm min. inc. motion
- <1nm encoder res.
- 5m/sec max. velocity
- 420N peak force
- Excellent value for precision automation
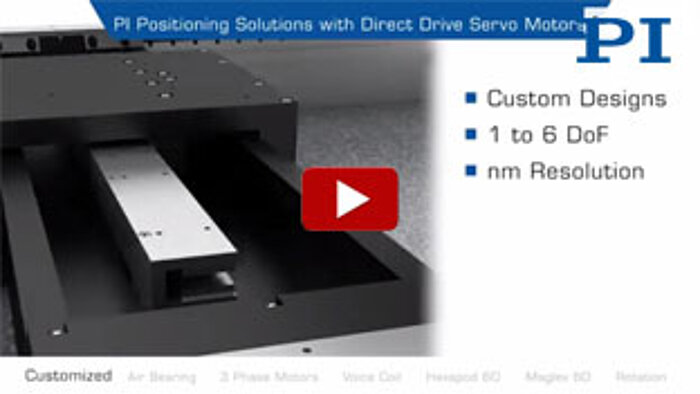
Video: Precision Automation Drive Principles
Watch Video
PI's Direct Drive Servo Motor Solutions with Air Bearings, 3-Phase Motors, Voice Coil, Hexapod 6D, MagLev, Rotation
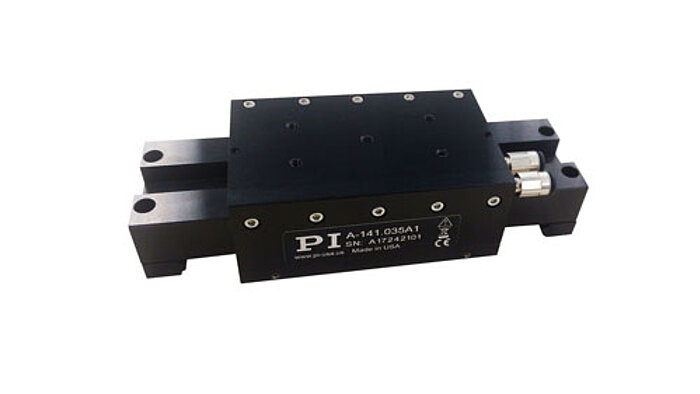
A-141 Miniature Air Bearing Stage
Ultra-Compact Air Bearing Stage
- 40mm travel
- 3.5kg load
- 20nm resolution
- 57x83mm table; 38mm height
- 0.25m/sec max. velocity
- 0.35g max. acceleration
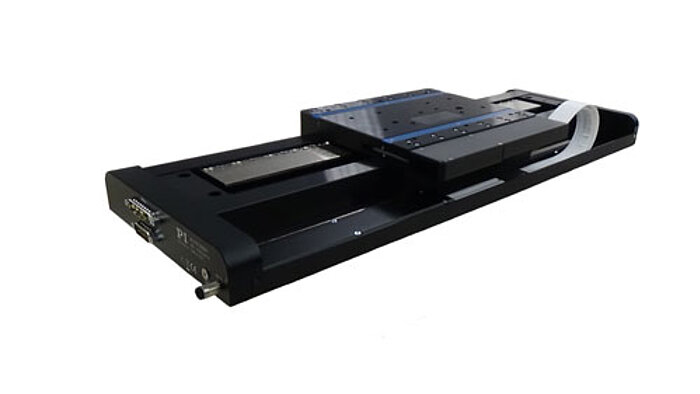
A-110 PIglide Air Bearing Stage
Affordable Design, Travel to 16”
- 2/4/8/12/16” travel
- 10kg load
- 1nm resolution, abs/enc option
- 160x200mm table; 60mm height
- 1m/sec max. velocity
- 2g max. acceleration
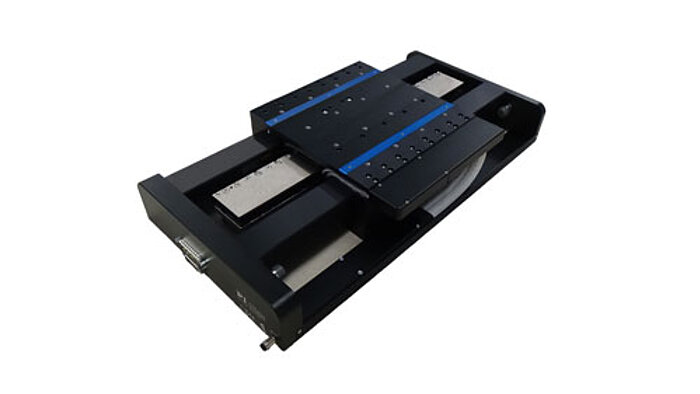
A-123 PIglide Air Bearing Stage
Large, Travel to 30”
- 2/4/6/10/14/20/30” travel
- 10kg load
- 1nm resolution, abs/enc option
- 210x210mm table; 85mm height
- 1m/sec max. velocity
- 3g max. acceleration
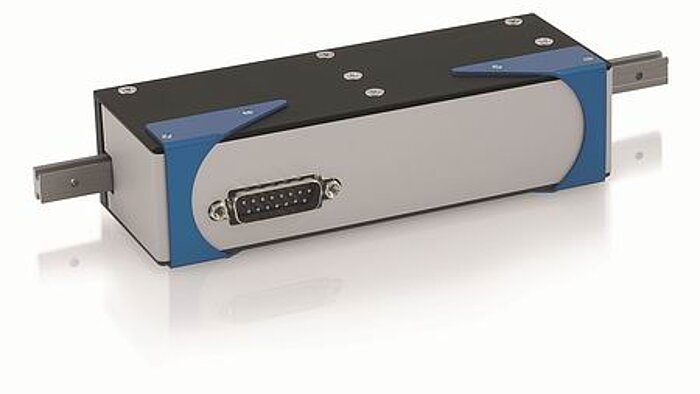
V-273 Voice Coil Actuator
Force Sensor Option
- 20mm travel
- 10nm linear encoder resolution
- 100mm/sec max. velocity
- 6N push/pull force
- 1mN force sensor option
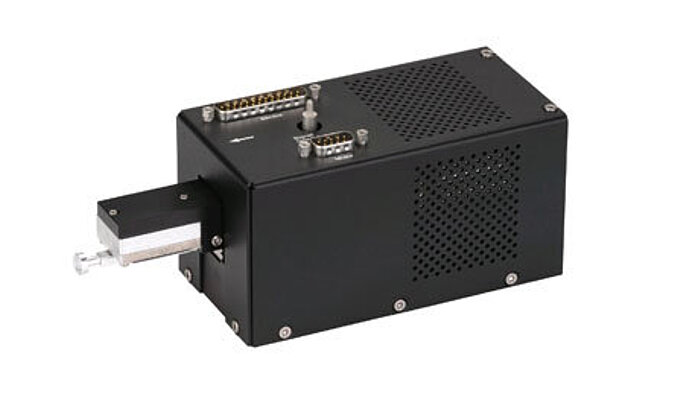
V-277 Voice Coil Actuator
High-Speed, Force Sensor Option
- 15mm travel
- 10nm linear encoder resolution
- 750mm/sec max. velocity
- 20N push/pull force
- 1mN force sensor option
Direct drive linear stages offer several advantages over other types of linear stages that employ a mechanical transmission system, such as belts, gears, or screws. Here are seven advantages of direct drive linear stages over gear and screw driven translation stages.
- Higher Accuracy: Direct drive linear stages can provide higher precision because there is no transmission system that can introduce backlash or mechanical hysteresis. Depending on the linear encoder and closed-loop controller used, they are capable of very high positioning resolution down to the nanometer range and below with high repeatability.
- Higher Velocity: Linear motor stages can provide motion with higher speeds than gear-driven stages because there are no losses in a mechanical transmission system to limit the velocity. This makes linear motors ideal for applications that require high-speed positioning.
- Higher Acceleration: Direct drive linear stages can achieve higher acceleration rates (typically several g’s), due to their reduced inertia and high power density, making them suitable for applications that require rapid step-and-settle motion.
- Smoother Motion: Linear motor stages provide smoother motion without jerkiness or vibrations, a decisive advantage in precision laser machining, metrology, and semiconductor wafer test and processing.
- No Maintenance: Linear motors lack gears, belts, leadscrews / ballscrews or other mechanical parts that can wear out due to friction or require lubrication. When integrated in linear stages together with air bearings, completely maintenance-free motion systems can be designed, with virtually unlimited lifetime. This results in lower operating costs and better ROI.
- Quieter Operation: Linear motors are non-contact drives and as such produce less noise compared to other types of drive systems, making them ideal for applications that require quiet operation. Less noise also means lower vibrations.
- Higher Energy Efficiency: Linear motors can be more energy efficient compared to other types of linear drives because there are no losses caused by friction in the power transmission system.