Piezo motor-driven positioning stages differ from traditional piezo stack/flexure guided nanopositioning systems. They combine elements of classical motorized positioners such as cross roller bearings, long travel ranges, etc., but replace electromagnetic linear motors (or motor / screw drive combinations) with electroceramic direct drives.
The compact piezo motor positioning stages on this overview page are grouped by the piezo motor type used internally. Ultrasonic motors provide the highest speed, inertia motors are extremely small, but not as fast, and PiezoWalk® motors provide the highest forces and precision. The video here explains the different drive principles.
Ultrasonic motors provide very fast start/stop behavior, smooth motion with a very wide dynamic range from microns/second to 100’s of millimeters/second. Both linear and rotary ultrasonic motors are based on compact piezo ceramic elements driven at high frequencies of 10’s to 100’s of kHz (beyond the human hearing range). Each oscillation cycle transfers nanoscopic motion to a linear or rotary ceramic surface bonded to a linear runner or rotary platform.
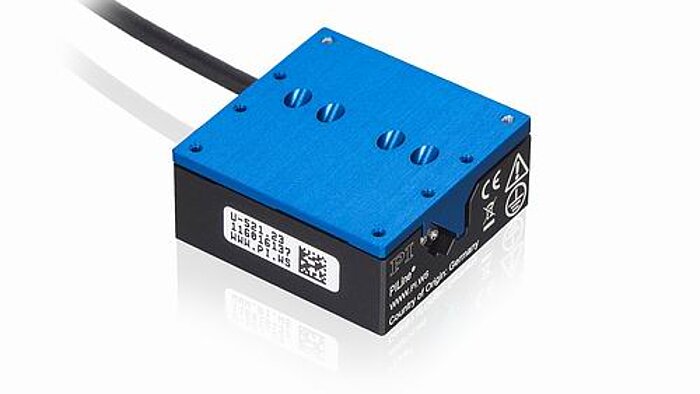
U-521 Miniature Linear Stage
Silent Ultrasonic Linear Motor
- 18mm motion range
- 0.1µm encoder resolution
- 200mm/sec velocity
- 35x35mm footprint
- Self clamping motor design
- Vacuum options
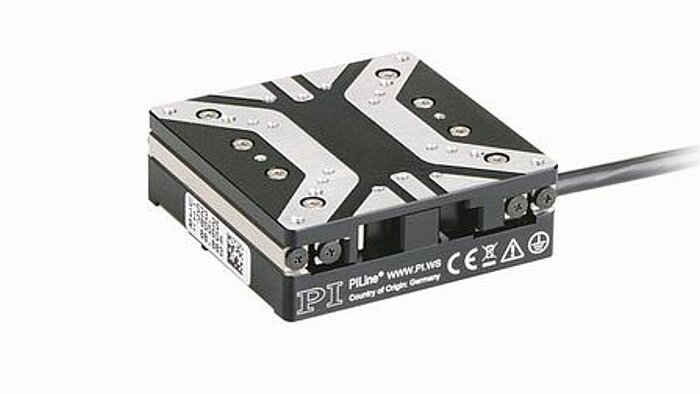
U-523 Miniature Linear Stage
Silent Ultrasonic Linear Motor
- 22mm motion range
- 10nm encoder resolution
- 200mm/sec velocity
- 42x42mm footprint
- Self clamping motor design
- Vacuum options
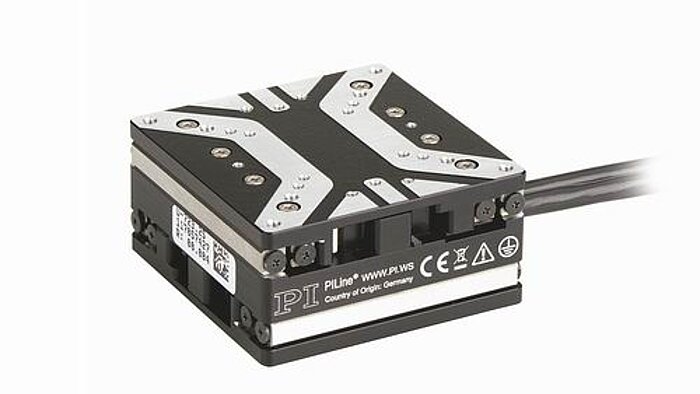
U-723 Miniature XY Linear Stage
Silent Ultrasonic Linear Motor
- 22x22mm XY motion range
- 10nm encoder resolution
- 200mm/sec velocity
- 42x42mm footprint
- Self clamping motor design
- Vacuum options
PIshift inertia-type piezo motors provide resolution in the micron to nanometer range. These extremely compact motors can be integrated into linear and rotary stages. The drive principle is based on a cyclical alternation of static and sliding friction between a moving runner and the drive element, related to the classic tablecloth trick.
Piezo inertia motors can be operated in open loop, but for high accuracy and repeatability, a position encoder is integrated in the stage. Vacuum compatible and non-magnetic versions are also offered. The PIShift piezo inertia drive is very quiet, due to its high operating frequency of 20 kHz.
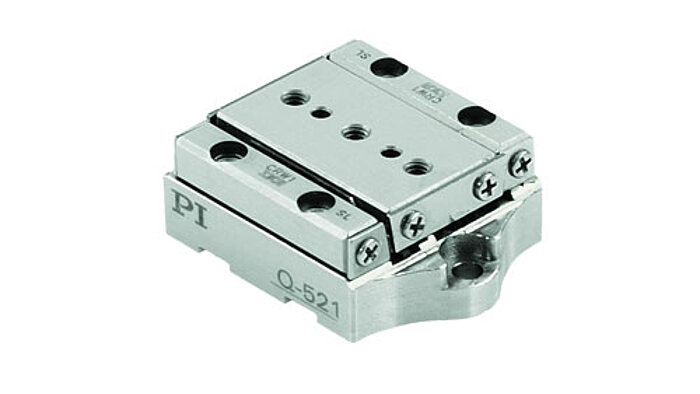
Q-521 Sub-Miniature Linear Stage
Piezo Inertia Direct Drive Motor
- 12, 22, 32mm motion range
- 1nm encoder resolution option
- 10mm/sec velocity
- 21mm width, 10mm height
- Self clamping motor, 1N
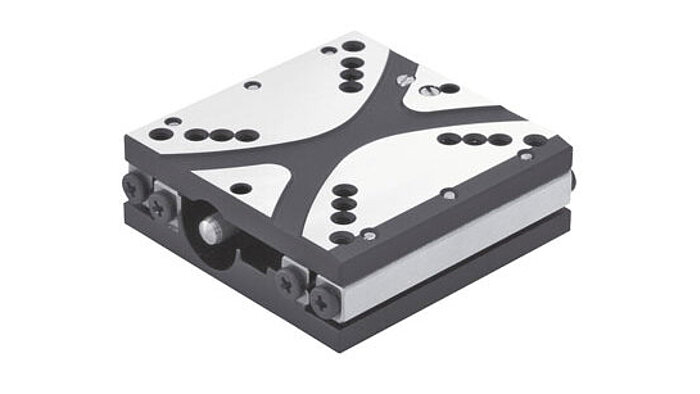
Q-545 Miniature Linear Stage
Piezo Inertia Direct Drive Motor
- ½” & 1” motion range
- 1nm encoder resolution option
- 10mm/sec velocity
- 45mm width, 15mm height
- Self clamping motor, 8N
The N-565 compact linear stage is equipped with PiezoWalk® linear motors and PI’s ultra-high precision PIone linear encoder providing 0.5nm resolution. The patented PiezoWalk® drive is based on the coordinated motion of several piezo actuators and combines piezo-class resolution in the sub-nanometer reange with long travel and extreme reliability. The motors are self-locking at power off, with no heat generation at position hold and extreme position stability.
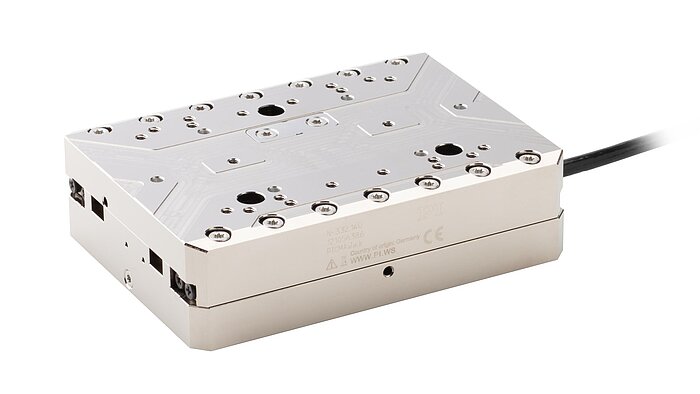
N-332 Nanometer-Precision Stage
1µm straightness/100mm
- 1” and 2” motion range
- 3nm min. incremental motion
- 12mm/sec velocity
- 80mm width, 30mm height
- 75N force, self-clamping motor
- UHV option
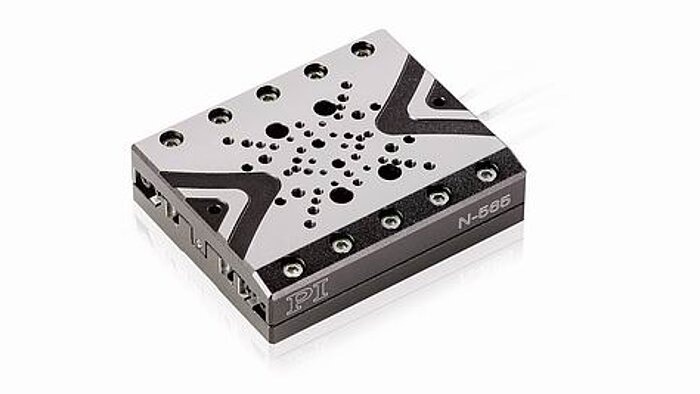
N-565 Nanometer-Precision Stage
PiezoWalk Direct Drive Motor
- ½”, 1” and 2” motion range
- 0.5nm encoder resolution
- 10mm/sec velocity
- 65mm width, 20mm height
- Self clamping motor, 10N
- Vacuum options