Air bearings have played a crucial role in the development and construction of coordinate measuring machines (CMMs) and other metrology tools for decades. Since they are inherently frictionless and highly stable, air bearings play a key role in delivering the precision required in metrology equipment. Performance criteria, such as repeatability and minimized error motions, geometric precision straightness and flatness for linear bearings, and axial and radial runout for rotary bearings, favor air bearings over mechanical ball and roller bearings in applications where the ultimate precision counts. Using high quality standard and custom air bearings designed and manufactured by PI, companies can develop world-class metrology equipment with sub-micron precision.
History
Development of the modern CMM began in the 1960’s, and with the advent of the Renishaw touch-trigger probe in the 1970’s, the industry boomed. The vast majority of CMMs built in the following decades have used air bearings for the guidance of the probe and in many cases to also move the part being measured.
To learn more about the history of the CMM, see:
- http://www.wenzel-cmm.co.uk/history-of-cmm/118
- https://en.wikipedia.org/wiki/Coordinate-measuring_machine
Design
CMMs and metrology tools use a variety of design architectures, including moving gantries, static gantries, cantilevered X-Y-Z, and many others. The most common type of CMM is composed of three orthogonal axes (X, Y, and Z) operating in a three-dimensional coordinate system. Each axis has a position encoder that indicates the position of that axis. The machine will read the input from the touch probe, as directed by the operator or computer program. The machine then utilizes the X, Y, & Z coordinates of each of these discrete points to determine size and position of the part being measured.
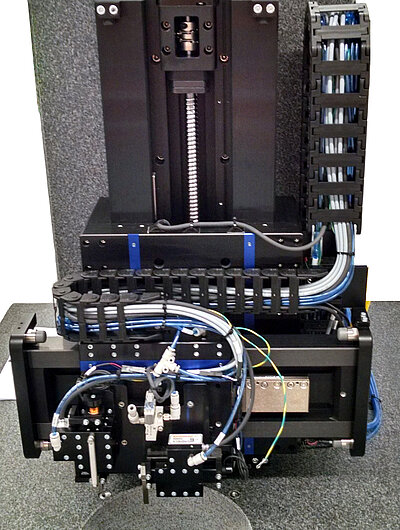
In addition to CMMs, there are many types of metrology tools on the market that use air bearings. These include systems to measure roundness, flatness, surface profile, or thickness of shafts, cams, turbine blades, optics, semiconductor wafers, and other precision components. In each of these system configurations, the high precision, stiffness, and stability of the air bearing enables the machine to measure part features with sub-micron accuracy and fidelity.
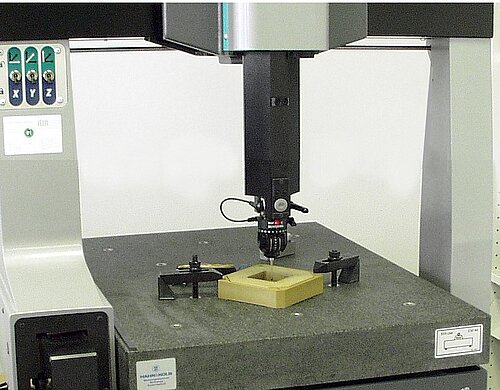
As discussed in a previous blog post, PI rotary air bearings can deliver axial error motions less than +/-25 nanometers. This allows the part measurement systems to gauge roundness errors of well under 0.1µm.
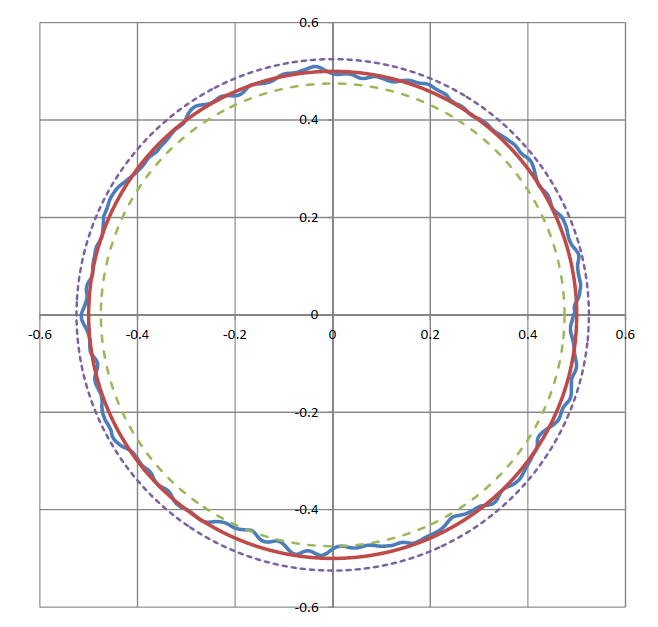
Air bearing motion systems are ideal for both point-to-point measurements, as well as more advanced scanning metrology methods. See here for more information about the superb scanning performance of a PI air bearing system.
Customization
Off-the shelf CMM cannot satisfy all metrology needs – especially for manufacturers that push the boundaries of technology. Such customers usually need to measure complex part geometry with extreme levels of precision. These parts can include turbine components, ball bearing raceways, engine bearings, camshafts, optics, and aerospace components. In these cases, PI will design and build a custom multi-axis air bearing motion system that can be used as the basis for a tailor-made high-end CMM. While PI does not deliver a finished CMM (which would include the probes and the CMM software), we do provide a turnkey motion system including the air bearings, granite structure, drive and feedback technology, cabling, controller, and machine base with vibration isolation. These systems often combine linear and rotary motion, with up to eight (8) synchronized axes of motion.
Blog Categories
- Aero-Space
- Air Bearing Stages, Components, Systems
- Astronomy
- Automation, Nano-Automation
- Beamline Instrumentation
- Bio-Medical
- Hexapods
- Imaging & Microscopy
- Laser Machining, Processing
- Linear Actuators
- Linear Motor, Positioning System
- Metrology
- Microscopy
- Motorized Precision Positioners
- Multi-Axis Motion
- Nanopositioning
- Photonics
- Piezo Actuators, Motors
- Piezo Mechanics
- Piezo Transducers / Sensors
- Precision Machining
- Semicon
- Software Tools
- UHV Positioning Stage
- Voice Coil Linear Actuator
- X-Ray Spectroscopy