A piezo nanopositioning stage is defined as a positioning device capable of nanometer or sub-nanometer resolution.
There are several types of nanopositioners – PI also makes air bearing stages, linear motor stages and magnetic levitation stages; devices featuring the highest dynamics and precision are piezo-driven, flexure guided and equipped with direct metrology position feedback, such as capacitive sensors.
Piezo Stage FAQs
- Why should I use a piezo stage?
- How do I control the piezo stage?
- Are flexure stages reliable?
- Serial and parallel kinematic stages — what is the difference?
- Strain gauge and capacitive sensors — what is the difference?
- Analog and digital piezo controllers — what is the difference?
- What software support is available?
- I also need a long-travel stage; can I combine coarse and fine motion?
- What are the advantages of working with PI?
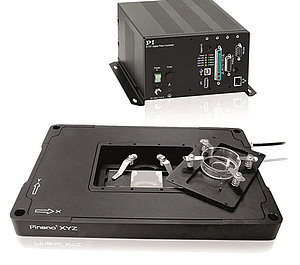
There are several types of piezo drives, optimized for different applications. Customers typically choose piezo flexure stages for their rapid response, extremely straight motion and virtually unlimited resolution.
When fast response, high stability and extremely smooth nanometer scale motion are required piezo flexure stages are superior to positioners with traditional mechanical bearings (cross rollers, ball bearings, etc.). The play, friction and tolerances of these bearings affect the precision of motion at the functional point. As a rule of thumb, a good flexure stage can provide 100 times better guiding precision.
Another advantage of piezo flexure stages is their minimized moved mass and higher stiffness, a combination that leads to better stability due to higher resonant frequency and a better ability to make short, fast moves with settling times in the millisecond range.
Travel ranges of piezo flexure stages are typically in the range of 50 microns to 2 mm. When longer travel is required, PI offers other types of piezo motor positioners and traditional motorized positioners.
How Do I Control The Piezo Stage?
PI makes piezo control easy. Controllers with both analog (0 – 10V) and digital interfaces are available. The digital interfaces have a high level command set. For example, the command to move to X=0.01mm position is MOV X0.01. The PI controller reads the position sensor (for closed-loop stages) compares it with the target position and the servo continuously calculates the correct drive voltage to achieve and maintain the required position.
Communication with the controller is also easy – there is a “terminal software”, a graphical user interface called “PI MikroMove”, and well developed software tools (DLLs, LV drivers, etc). Commands are ASCII structure sent via Serial or Ethernet.
Are Flexure Stages Reliable?
Yes! PI has been building and optimizing piezo flexure stages for almost 40 years. Key design parameters for reliability are the piezo ceramics itself, the mechanical interface between the piezo and the stage and the flexure design. PI’s patented PICMA® piezo actuators passed 100 billion cycles of life testing by NASA engineers and are used on the Mars Rover. Flexures, if designed and operated properly exhibit no wear and provide exceptional guiding characteristics due to the absence of friction and play. PI flexure stages are used in automation applications as well as high availability scientific applications. And – over the last 4 decades PI has improved the performance and reliability as well as reduced the cost.
Serial and Parallel Kinematic Stages — What Is The Difference?
There are 3 ways to achieve multiaxis piezo motion:
- stacking of individual single-axis stages
- coplanar nesting of independent axes
- parallel kinematics
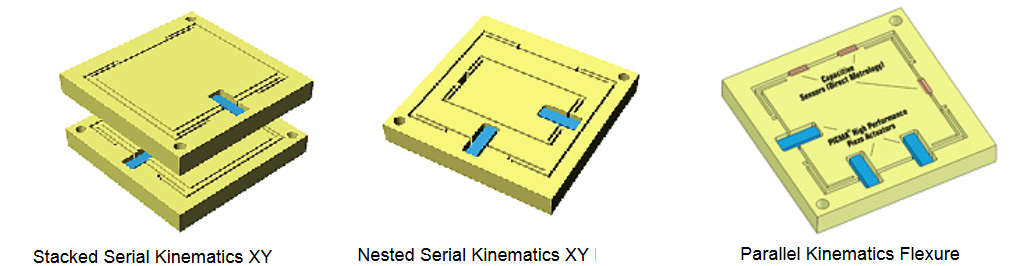
In a parallel kinematics design, multiple actuators are moving a single platform directly resulting in higher stiffness and reduced moved mass. In addition, parallel metrology can be implemented, where each position sensor can “see” on-axis and unwanted off-axis motion, resulting in higher multi-axis precision.
Strain Gauge And Capacitive Sensors — What Is The Difference?
Capacitive sensors measure distance directly and without contact. They provide very high linearity and the best long term stability. Strain gauge sensors (piezo resistive types and metal foil types) are bonded to the structure of the stage and derive distance information from strain. They cost less and are sufficient for many applications, but cannot match the linearity and stability of the direct measuring capacitive sensors. PI offers nanopositioning stages with piezo resistive sensors; metal foil strain sensors; and several types of capacitive sensors ; metal foil strain sensors; and several types of capacitive sensors and a variety of other displacement sensors.
The difference has nothing to do with the control interface. Analog controllers with digital interfaces are available as well as digital controllers with analog control interfaces. The answer lies in the servo part of the controller. Traditionally, piezo controllers were based on analog servos, due to the analog output nature of the position sensors employed. Digital servos permit the use of advanced control algorithms, error correction and linearization schemes not feasible with analog servos. In addition, parameters can be changed on the fly, and optimization or adaptation to different load and operating conditions can be performed remotely without touching the controller hardware. There are other advantages such as stage / controller interchangeability etc. Learn more about PI’s analog and digital piezo nanopositioning controllers.
What Software Support Is Available?
PI controllers use the PI General Command Set (GCS). GCS provides numerous preprogrammed functions to accelerate the orientation and application development phase significantly. GCS is consistent for all PI motion controllers. Additional software:
PIMikroMove GUI
PIMikroMove is a very powerful graphical program ensuring rapid start-up right out of the box. It also integrates a Macro language, scan/align algorithms and a data recorder for system analysis.
LabVIEW
PI provides complete open source LabVIEW drivers sets to facilitate programming.
Text-Based Programming Languages
All common programming languages under Windows & Linux with libraries and code
examples.
Supported languages and software environments
C, C++, Python, Visual C++, Visual Basic, Delphi, LabVIEW, MATLAB, EPICS, TANGO, MetaMorph, µManager and all programming environments that support loading of DLLs
Simulation Programs:
Predict the system response and bandwidth with different controllers and load settings.
More on software
I Also Need A Long-Travel Stage, Can I Combine Coarse And Fine Motion?
PI offers piezo stages and motorized stages. Since all PI motion controllers use the same command and driver set, the development phase is shortened significantly. PI also provides hybrid positioners – with piezo and motor drives – combining the benefits of both worlds. In either case, PI will seek to understand the requirements of your application and help you make a good choice about the precision motion design path.
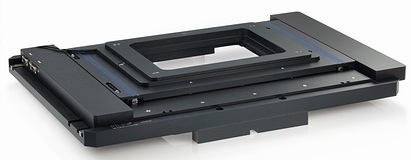
What Are The Advantages Of Working With PI?
- Experience: PI has been designing piezo positioning systems for 4 decades and has manufactured more precision flexure nanopositioning systems than anybody else. With 850+ employees, PI is also the largest piezo positioning systems manufacturer in the world by a wide margin.
- Performance: The performance of a piezo flexure system depends on the precision of the flexure design, the sensor and the controller. The ability to choose from a larger variety of proven sensors, flexure designs and controllers gives PI design and application engineers the ability to find a better solution for a given task. When it comes to performance there is no “one-design-fits-all” solution.
- Metrology, Test & Measurement Equipment: You can only specify what can be verified by external independent metrology. PI uses world-class, 6-fold isolated and stabilized nanometrology labs, equipped with the latest laser interferometers, and test equipment to verify and characterize its nanopositioning devices. More information on PI metrology equipment
- Reliability: PI’s piezo stages are driven by the patented PICMA® piezo ceramic actuators – a highly reliable technology that was selected by NASA engineers for the Mars Rover mission after it had passed 100 Billion test cycles without failures. More information on PICMA® reliability
- Last but not least, controller technology is critical for the system performance. Piezo controllers differ largely from servo motor or stepper motor controllers. Here, PI’s extensive research and experience is another great advantage.
- You get a complete package with mechanics, controller, software and PI’s expert global support. If you want to learn more about piezo positioning technology, refer to the Piezo Motion Control Tutorial.
Blog Categories
- Aero-Space
- Air Bearing Stages, Components, Systems
- Astronomy
- Automation, Nano-Automation
- Beamline Instrumentation
- Bio-Medical
- Hexapods
- Imaging & Microscopy
- Laser Machining, Processing
- Linear Actuators
- Linear Motor, Positioning System
- Metrology
- Microscopy
- Motorized Precision Positioners
- Multi-Axis Motion
- Nanopositioning
- Photonics
- Piezo Actuators, Motors
- Piezo Mechanics
- Piezo Transducers / Sensors
- Precision Machining
- Semicon
- Software Tools
- UHV Positioning Stage
- Voice Coil Linear Actuator
- X-Ray Spectroscopy