50 Hexapod 6-DOF Alignment Systems for the Sub-Reflectors of ALMA, the Largest Telescope Project in the World
The ALMA (Atacama Large Millimeter Array) observatory is the largest and most advanced astronomical telescope system in the world. ALMA is not a classical optical telescope but a combination of up to 66 radio-telescope dishes receiving electromagnetic radiation at millimeter and sub-millimeter wavelength. The combination of many antennas, spread out over a large area, has a similar effect as a much larger single antenna, but at a lower cost. The individual antennae are spread between 150 m and a maximum of 12 km.
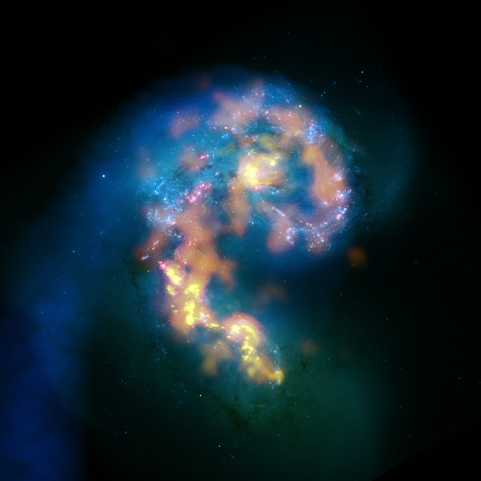
Millimeter and sub-millimeter astronomy investigates the universe in the spectral range which traditionally stretches from radio waves to the infrared. Data gathered by ALMA will tell us more on the structure of the early universe, as well as galaxies, stars, and planets in their formative stages.
The antenna array is located in the Atacama Desert of northern Chile at an altitude of 5,000 meters. These are favorable conditions for the best possible observations, since millimeter radiation is absorbed by water vapor in the atmosphere and humidity levels at this altitude are extremely low, minimizing the attenuation mm and sub-mm wavelength radiation. In its final state, there will be a combination total of 66, 39ft and 23ft antennas.
A typical radio telescope antenna consists of a main reflector (the large dish) and a secondary, sub-reflector that needs to be aligned properly in regard to the main dish for maximum efficiency. This precision alignment task is carried out by special Hexapod 6-axis parallel positioning systems from PI. It gives insights into the birth of new galaxies, stars, and planets, but also into star systems of the early universe that are more than 13 billion light years away.
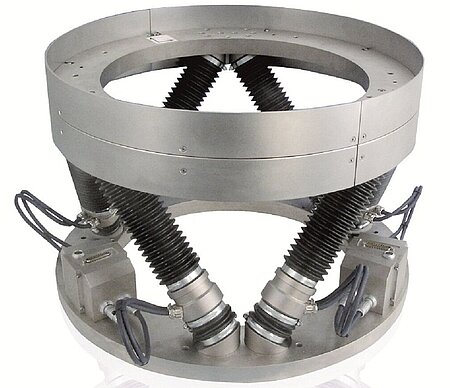
Technological demands here are high: low air pressure, temperature differences of up to 50°C, strong winds, dust and rain are additional challenges in 5,000 meters above sea level that have to be faced.
One of the challenges for designing the high precision systems are the adverse conditions with low pressure, high winds, and huge temperature swings between day and night, of up to 90°F (50°C).
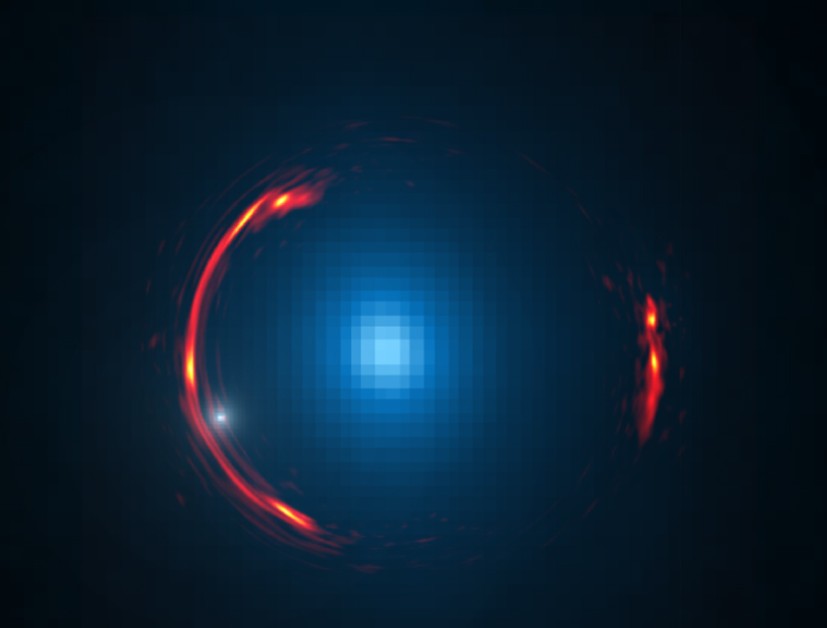
To keep the antenna performance at its optimum, the sub-reflectors even out external impacts on the mechanical system. Deviations can occur, for example, with antenna tracking that compensates for global rotation, with bending of telescope components due to gravitation, or through thermal effects or wind load.
The sub-reflectors are mounted on the hexapods which provide motion with 6 degrees of freedom. The PI Hexapod combines a load capacity of 200 kg with sub-micron linear resolution and microrad-level angular resolution. A digital motion controller provides advanced features, such as a user-programmable virtual pivot point, critical in complex alignment applications. Target positions in 6-space are commanded in Cartesian coordinates and reached by smooth vectorized motion. Hexapod parallel kinematics are lighter, more compact, and stiffer than conventional serially stacked multi-axis motion systems. The effect is a higher natural frequency with improved dynamics, faster step & settle, and higher stability.
High Altitude Controller – Fanless
All components in the digital vector motion controller were selected to work in the low atmospheric pressure at 16,000 ft altitude. For higher reliability, the controller does not require a fan for cooling. PI has been supplying hexapods, micropositioning actuators, and active optics for astronomical telescopes, including several infrared telescopes on Mauna Kea in Hawaii, as well as telescopes in Chile, South Africa, and the Canary Islands, for over 25 years.
Early Prototypes
Prototypes of the final antenna design were developed as early as 2000. PI delivered an industrial Hexapod that had proven reliable in operation at the ALMA VertexRSI test antenna and the Atacama Pathfinder Experiment (APEX) radio telescope.
Blog Categories
- Aero-Space
- Air Bearing Stages, Components, Systems
- Astronomy
- Automation, Nano-Automation
- Beamline Instrumentation
- Bio-Medical
- Hexapods
- Imaging & Microscopy
- Laser Machining, Processing
- Linear Actuators
- Linear Motor, Positioning System
- Metrology
- Microscopy
- Motorized Precision Positioners
- Multi-Axis Motion
- Nanopositioning
- Photonics
- Piezo Actuators, Motors
- Piezo Mechanics
- Piezo Transducers / Sensors
- Precision Machining
- Semicon
- Software Tools
- UHV Positioning Stage
- Voice Coil Linear Actuator
- X-Ray Spectroscopy