Advanced imaging methods have had an unfathomable impact on human manufacturing and research capabilities, liberating scientists from the limitations of conventional optical microscopy and enabling the visualization of structures on the sub-micron to sub-nanoscale. This success hinges on numerous interwoven innovations, including control electronics, sample preparation and development of high-precision motion platforms based on novel electro-ceramic drives.
In this blog post, PI explores the key principles of motion platforms in advanced microscopy in greater detail.
The resolving powers of leading-edge microscopic instrumentation vary dramatically given the sheer variety of tools available to modern scientists. For example:
- Atomic force microscopy (AFM) has one of the highest vertical (Z-axis) resolutions available – as much as 0.1 nanometres (nm) – although this depends on the method and mode used (i.e. tapping). Certain AFM techniques can provide reliable visualization of individual atoms and molecules in samples. However, AFM cannot reveal spectral information and does not work on living cells.
- Scanning electron microscopy (SEM) exploits a beam of electrons to interrogate specimens with an approximate resolution of 0.2 nm, or 200 picometres (pm), achieving magnifications of up to 2,000,000x.
- Confocal microscopy was the first optical microscopy to allow 3D images of living cells. It has a comparatively poor resolution in the Z-axis– approximately 500 nm – but with good lateral resolution (XY-axes) and the ability to observe a relatively wide sample plane from a distance comparable to compound microscopy.1 http://www.physics.emory.edu/faculty/weeks//confocal
- Super resolution optical microscopy techniques take confocal microscopy a step further and allow resolutions down to the 10nm range, with the ability to image single bio molecules. More information on the latest light sheet super resolution microscopes
These are just three examples of a richly diverse field of instruments – many of which rely on high-precision motion platforms to move optical components or the samples. To accurately and repeatably acquire nanoscale information from samples of interest, advanced visualization methods require precise positioning of samples with tight control of at least three axes of motion (XYZ).
Case Study: Motion Platforms in AFM
Take AFM systems, for example: The atomic-scale resolution of AFM demands a sample positioning motion platform with a resolution in the sub-nanometer range. Consequently, AFM systems use motion platforms based on electro-ceramic drives known as piezo actuators, which exhibit small-scale dimensional changes in response to applied voltages. Often AFM scanners are based on segmented piezo tubes, but higher accuracy and linearity can be achieved when flexure guideds are used to guide the motion and high resolution sensors are integrated for exact position feedback.
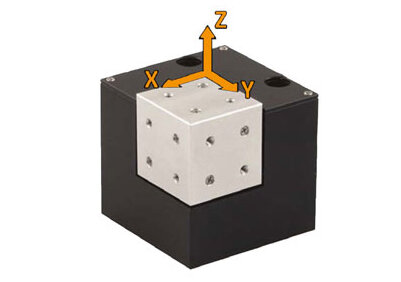
P-616, closed loop XYZ piezo flexure nanopositioning stage, 100µm travel. The stage allows for easy integration due to its compact size and flexible control. See link for research paper on Adaptive atomic force microscope, below with more information on “custom AFM platform which is readily integrated into an FPGA controlled fluorescence microscope…”. The adaptive system “presents the freedom to perform precise measurement and manipulation in a high throughput manner, over a broad range of distances” Source: https://www.spiedigitallibrary.org/conference-proceedings-of-spie/11246/0000/Adaptive-atomic-force-microscope/10.1117/12.2545261.short
A flexure guided nanopositioning stage can provide motion in up to 6 degrees of freedom with sub-nanometer precision. Driven by piezo ceramic actuators (blocks of thin ceramic layers on the order of a few micrometers interspersed with electrodes and sintered into a singular structure), the actuation of these flexure stages is extremely sensitive and quick, as piezo material can expand with the speed of sound. This allows response times in the sub-millisecond range and facilitates high dynamic control for fast scanning of XY axes over travel ranges up to several 100µm for direct and precise sample positioning across a broad scanning plane.
Multi-axis motion platforms for AFM sample positioning utilize flexure guides for their outstanding accuracy, longevity, and compatibility with vacuum environments (no lubricants, no wear). Often, capacitive sensors are used in conjunction with flexures to increase path fidelity and guarantee the reliability of positioning over billions of use cycles. Motion platforms subsequently provide the framework for effective, future-proof testing of myriad sample types (ceramics, metals, organics, etc.) via AFM to develop a deeper understanding of the atomic-scale structures and interactions of different materials.
PI: Motion Platforms for Microscopy
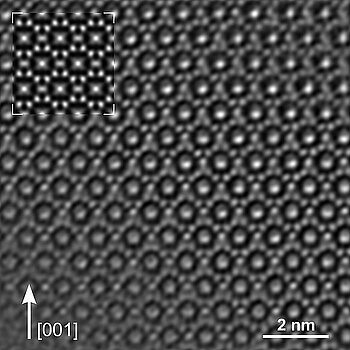
Physik Instrumente (PI) is a world leader in the design of innovative motion platform solutions for high precision and high dynamics applications. We supply a suite of piezo-based positioning solutions for advanced imaging applications, whether it is the objective, the sample, or both that need manipulating in situ. If you would like to learn more about the motion platform products that we offer for microscopy applications, take a look at our recent blog post:
Piezoelectric Positioning Equipment for Nanoscale Microscopy & Imaging
Otherwise, contact a member of the PI team today with any questions about increasing precision in your visualization tasks using advanced motion platforms.
Blog Categories
- Aero-Space
- Air Bearing Stages, Components, Systems
- Astronomy
- Automation, Nano-Automation
- Beamline Instrumentation
- Bio-Medical
- Hexapods
- Imaging & Microscopy
- Laser Machining, Processing
- Linear Actuators
- Linear Motor, Positioning System
- Metrology
- Microscopy
- Motorized Precision Positioners
- Multi-Axis Motion
- Nanopositioning
- Photonics
- Piezo Actuators, Motors
- Piezo Mechanics
- Piezo Transducers / Sensors
- Precision Machining
- Semicon
- Software Tools
- UHV Positioning Stage
- Voice Coil Linear Actuator
- X-Ray Spectroscopy