Flexible Piezo Transducers find Applications in Structural Health Monitoring, Contouring, and Sound Cancellation
Piezo ceramics - like all ceramics - are brittle materials, very good at handling compressive loads, but sensitive to shear, bending, and tensile loads. To protect the piezo material from unwanted forces, several mechanical solutions have been developed over the years. One clever way is found in the patented laminate structure of the DuraAct patch transducers. These are composites of one or more thin piezoceramic plates equipped with electrodes, electrically insulated and mechanically pre-stressed by a polymer outer skin. Depending on the application, strands can be soldered, glued or clamped at two contact points. The patch transducer can even have separate sensor and actuator functionality by contacting several layers separately.
Structural Health Monitoring
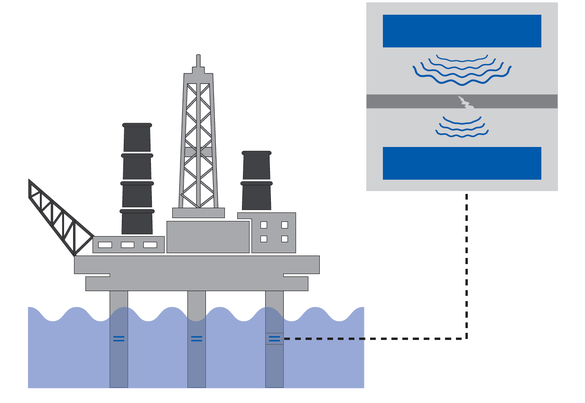
Structural Health Monitoring
Piezo transducers can be used to measure deformations on structures or components that are difficult to access such as weld seams, bridges, etc. Entire areas can be actively monitored by using some transducers as wave-generating actuators, while other modules work as sensors and pick up these waves. Disturbances within a component, e.g. micro-cracks, are detected by comparison with reference signals from the undamaged system.
Active Vibration and Sound Insulation
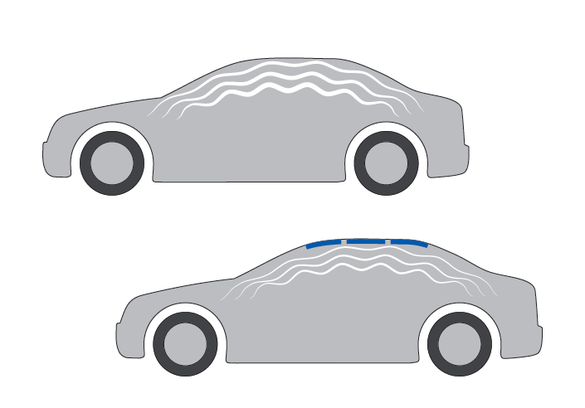
Active Vibration and Sound Insulation
DuraAct Patch Transducers can be operated in sensor and actuator mode. When used in actuator mode, they can dampen or cancel undesired vibrations. The phase-shifted sensor signal can also be used as voltage supply for the same piezo element.
Contouring
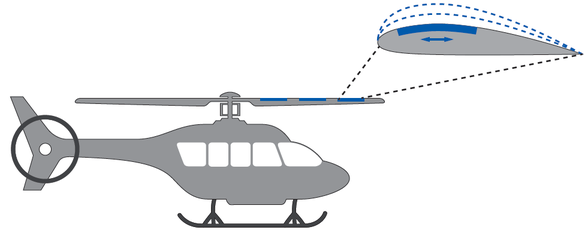
Contouring
Due to their function as sensors, DuraAct Patch Transducers can detect deformations that can be counteracted by driving an appropriate signal into the actuator. This enables contouring and deformation with precision in the sub-micrometer range.
Different Designs: Contraction Mode, Shear Mode, Bulk and Multilayer Variants
There are several variations available that behave differently (when used as actuators) and have different directional sensitivities when used in sensor mode.
Standard variations such as the P-876 type transducers are polarized in a way to provide longitudinal and transversal contraction or expansion, when an electric field is applied, with a max displacement to 800µm/m and a maximum operating voltage of 1,000V. These versions are very flexible and allow for a minimum bending radius to 12mm.
Shear piezo transducers provide shear motion between the top and bottom surface. They can be used to generate surface acoustic waves. The maximum drive voltage is 500V.
Multilayer patch transducers (P-878 family) provide longitudinal expansion with transverse contraction, with relatively high axial displacement to 1,200µm/m. The multilayer design provides greater efficiency and reduces the max operating voltage to 120V.
Blog Categories
- Aero-Space
- Air Bearing Stages, Components, Systems
- Astronomy
- Automation, Nano-Automation
- Beamline Instrumentation
- Bio-Medical
- Hexapods
- Imaging & Microscopy
- Laser Machining, Processing
- Linear Actuators
- Linear Motor, Positioning System
- Metrology
- Microscopy
- Motorized Precision Positioners
- Multi-Axis Motion
- Nanopositioning
- Photonics
- Piezo Actuators, Motors
- Piezo Mechanics
- Piezo Transducers / Sensors
- Precision Machining
- Semicon
- Software Tools
- UHV Positioning Stage
- Voice Coil Linear Actuator
- X-Ray Spectroscopy