Compact Automated XYZ Fiber Alignment System
Fast Multistage Approach in an Affordable Modular Concept
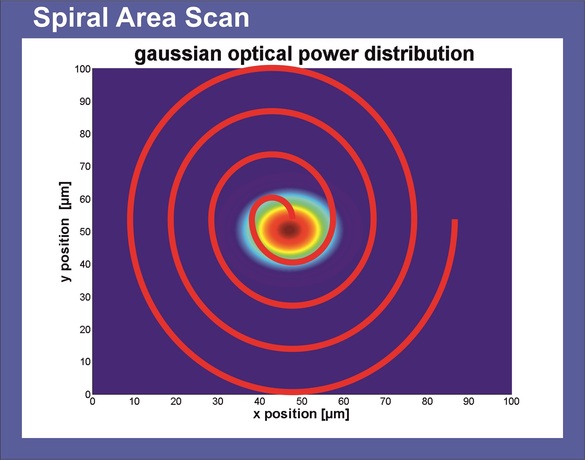
A defined area is scanned using a spiral or sinusoidal scan routine. The advantage of scanning at a constant frequency is the ability to avoid system resonance. This ensures successful scanning.
Practical work with fiber-optics based components such as optical chips, silicon photonics wafers, and single mode fibers requires alignment tools that provide nanometer-scale resolution and excellent stability. In the old days of fiber optics, a good mechanical system could often do the trick when time and throughput were inconsequential. However, for developing, studying, and pursuing manufacturing & testing methods of photonic components, an automated alignment system is essential today.
Applications include maintaining and characterizing optical couplings, which can be sensitive to the scale of a few nanometers. Automation is essential both because of the delicate submicron nature of these alignments, and because demanded quantities are rising rapidly as the technology is increasingly integrated into the mainstream of microelectronics manufacturing.
Why Multistage Approach?
Multistage rockets have been used to carry astronauts and equipment into space for a long time. The advantage over single stage rockets is that with each stage the remaining inertia (moved mass) is reduced, allowing better dynamics with higher efficiency. In PI’s F-131 photonics alignment system, long-travel motion (15mm, 50nm resolution) is provided by closed-loop servo motor/screw drives, while high resolution motion is provided by an XYZ piezo flexure scanner with integrated position feedback for nanometer precise scans.
This approach reduces the moved mass significantly and allows for faster scanning while minimizing recoil forces and improving stability at the same time. The piezo flexure scanner is also friction, maintenance, and wear-free – another decisive advantage for long term performance.
Integrated Spiral and Sinusoidal Scan Routines Improve Throughput and Reduce Vibrations
The integration of area scanning capabilities into the controller can lead to significant improvements in scan-and-align throughput since pointwise approaches are avoided, eliminating communication latencies and settling times. A single-frequency, sinusoidal approach represents a significant advancement over traditional raster and serpentine area scans by replacing their time-consuming stops-and-starts with continuous motion, ending ensuing vibrations. The frequency of the scan can be set by the user to avoid excitation of structural resonances in the fixturing and device, further facilitating overall scan speeds.
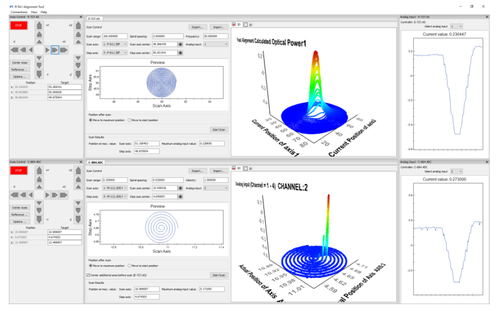
A single command starts the scan, and you can activate integrated data recording that synchronously acquires optical data with multi-axis position. High-speed Ethernet and USB interfaces, a high resolution analog input for optical metrology, and a wealth of software libraries for rapid application development help ensure rapid productivity and flexibility in usage. A versatile graphical utility called PIMikroMove is included for easy interactive control and visualization right out of the box, and programming examples in NI LabVIEW, Python, MATLAB, and other popular programming environments are provided. Cross-platform support, including Windows, macOS, and Linux, is amply documented for efficient development.
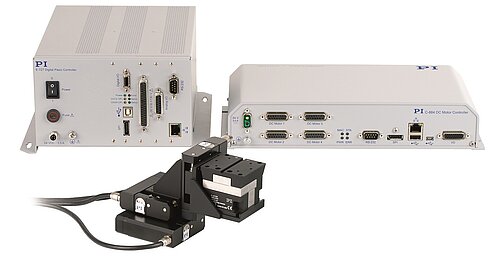
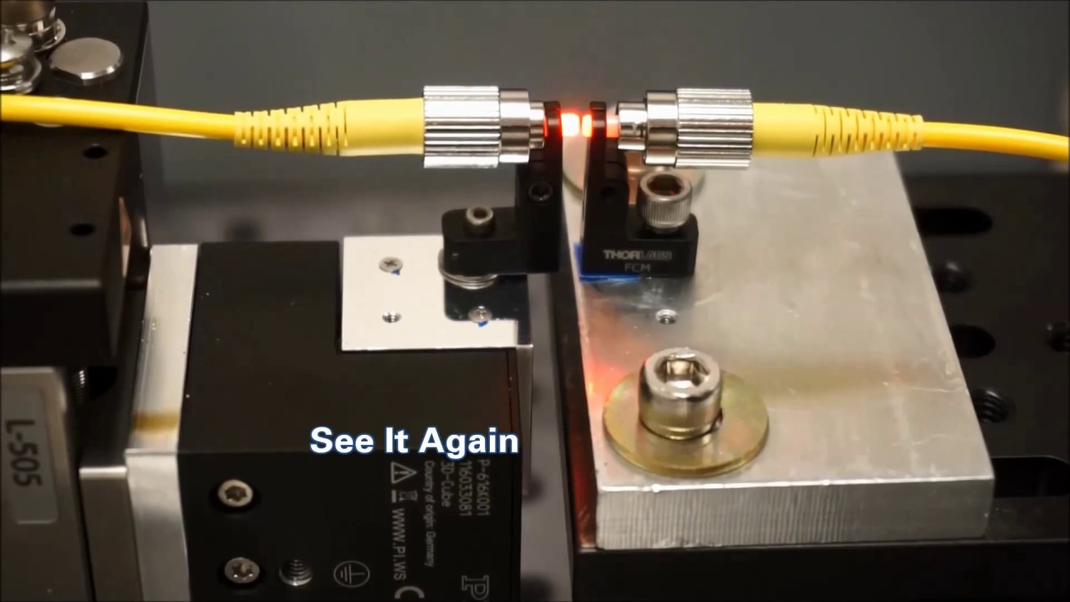
Blog Categories
- Aero-Space
- Air Bearing Stages, Components, Systems
- Astronomy
- Automation, Nano-Automation
- Beamline Instrumentation
- Bio-Medical
- Hexapods
- Imaging & Microscopy
- Laser Machining, Processing
- Linear Actuators
- Linear Motor, Positioning System
- Metrology
- Microscopy
- Motorized Precision Positioners
- Multi-Axis Motion
- Nanopositioning
- Photonics
- Piezo Actuators, Motors
- Piezo Mechanics
- Piezo Transducers / Sensors
- Precision Machining
- Semicon
- Software Tools
- UHV Positioning Stage
- Voice Coil Linear Actuator
- X-Ray Spectroscopy