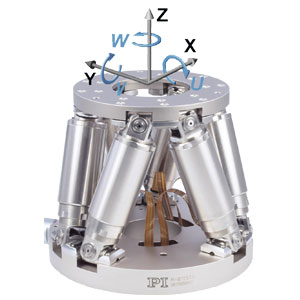
Active optical alignment in 6 degrees of freedom provides the best conditions for high image quality when it comes to aligning multiple lenses. Hexapod micro-motion robots are a novel technology that delivers motion in all six degrees of freedom in an unusually stiff, compact, and high-precision structure, composed of a single moving platform supported in parallel by six motorized struts arranged with optimized constraint (“parallel kinematics”). From a motion control standpoint, hexapod alignment systems are the equivalent of an XYZ stack with a rotation stage and two-axis goniometer mounted on top. This is actually an oversimplification since the double-tripod format combined with PI’s latest digital motion controller technology allows free translation and rotation of the system’s coordinate system at any time. This allows the rotational centerpoint to be placed anywhere in space, such as at an optical focus, a fiber optics or waveguide end-face, or any other convenient location. This in turn allows geometric errors and cross-couplings to be minimized or eliminated during angular actuation. Other advantages include an order of magnitude higher stiffness than even the highest-quality stage stacks, identical dynamics across axes, and elimination of moving/sweeping cables and the deflections, wear, and unreliability that they cause.
But the biggest differences relate to functionality. For camera and optical device manufacturing, these can be not just significant to, but actual enablers of next-generation manufacturing processes. For example, PI’s controller incorporates a built-in position-waveform generator, a high-speed data recorder, and a host of novel automated-alignment and scanning algorithms, including a parallel gradient search capable of simultaneous optimization of multiple degrees of freedom. An optional force sensor is available for measuring and generating calibrated forces with milligram-scale sensitivities. PI’s unique H-811 hexapod precision 6-axis motion system offers travels of up to 34mm/42 degrees with sub-sub-micron closed-loop precision and speeds to 20mm/sec. PI’s insistence on high-quality, high-stiffness offset cardanic joints means these hexapods can be mounted in any orientation for virtually backlash-free operation. And their advanced, brushless DC motors yield long lifetimes with broad operational dynamic range — all in a package about the size of a 2-lb coffee can.
Enabling Examples
MTF Optimization
Combined with fast imaging and modulation transfer function conversion that may be externally implemented in several ways, multiple hexapod micro-robots can optimize MTF of optical-train elements simultaneously. This active alignment approach relies on the ability of multiple optimization processes to be defined and run on hexapods carrying each element in the lens assembly. This can vastly improve process throughput for final assembly and qualification of precision optical imaging devices. Optimization can even be performed during adhesive curing to rectify curing stresses and improve device quality.
Throughput Optimization
Combined with fast external optical power metrology, hexapod micro-robots can optimize optical throughput through optical trains, laser cavities, and photonic assemblies, across multiple degrees of freedom and multiple channels, all in one step. Compared to traditional techniques that until now have necessitated repetitive, looping sequences of positional tweaking across the involved degrees-of-freedom, the resulting throughput improvement can exceed two orders of magnitude. This can virtually eliminate the alignment process as a contributor to manufacturing process cycle time.
Many times, a key process and quality metric will involve mapping the positional dependence of a measured quantity as a function of position in one or two axes. PI’s hexapod micro-robots incorporate unique, vibrationless single-frequency areal scanning algorithms which, combined with the controller’s built-in data recorder, allows synchronous acquisition of external metrology and six-axis position on-the-fly. Internal mapping allows accurate determination of calculated maxima and centroid positions even with coarse, fast scans. The data can be subsequently pulled from the controller for graphing or further analysis via the fast interfaces (TCP/IP or RS-232).
Optical Image Stabilization Test & Calibration
PI’s hexapod micro-robots incorporate a built-in, multi-axis arbitrary positional waveform generator that is useful for simulating disturbances, such as physiological tremors and vehicular motions. This capability has proven valuable for development, evaluation, and production test of optical image stabilization technologies and mechanisms. Data acquisition can proceed in parallel with position-waveform generation.
PI’s hexapod micro-robots have been delivered in quantity for demanding, 24/7 optical fabrication, pick-and-place and assembly tasks for many years. PI’s commitment to continuous improvement has yielded significant and valuable new functionality over time as well, as we have detailed here. And PI’s broad and deep software stack provides quick, cross-platform development. As the undisputed world leader in high-precision hexapod technology, PI delivers the functional capability and global support demanded by today’s tough manufacturing challenges. Contact your local PI office for expert applications consultation on high-throughput, high-reliability optical assembly automation solutions.
Blog Categories
- Aero-Space
- Air Bearing Stages, Components, Systems
- Astronomy
- Automation, Nano-Automation
- Beamline Instrumentation
- Bio-Medical
- Hexapods
- Imaging & Microscopy
- Laser Machining, Processing
- Linear Actuators
- Linear Motor, Positioning System
- Metrology
- Microscopy
- Motorized Precision Positioners
- Multi-Axis Motion
- Nanopositioning
- Photonics
- Piezo Actuators, Motors
- Piezo Mechanics
- Piezo Transducers / Sensors
- Precision Machining
- Semicon
- Software Tools
- UHV Positioning Stage
- Voice Coil Linear Actuator
- X-Ray Spectroscopy