Novel Sample Stage Alignment Hexapod for X-ray Microscopy and Tomography
Hexapod with Additional Linear Encoders to Achieve the Highest Precision
1. Application: X‑Ray Microscopy / Tomography
For synchrotron-based sub-micrometer hard X‑ray Tomography, the sample rotation axis must be aligned very precisely in at least five degrees of freedom with respect to the field of view, the lens, the detector or the beam itself. High stiffness and stability are required, too. A hexapod-type parallel kinematic machine (PKM) is well suited for this purpose. It provides six degrees of freedom, the pivot point can be chosen arbitrarily (for example, along the rotation axis), and it is very stiff and compact compared to a serial kinematic stack of stages.
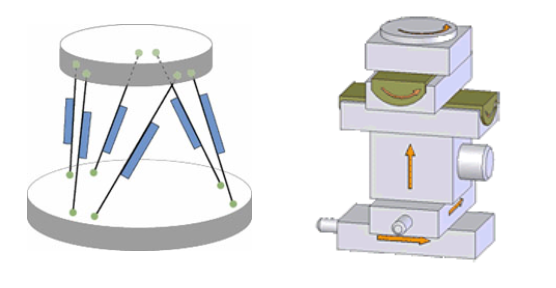
For the example in focus, we implemented a customized hexapod. It features an oval baseplate to fit into an actual X-ray microscope and a top platform which provides mounting interfaces to other components on top of the device. But, the main challenge was to meet the very demanding requirements regarding its precision.
2. Challenge: Load / Position-Independent Position Measurement
The position of the center of mass of the payload will necessarily change when the PKM is moving. In the given application, the mass of the device mounted on top of the PKM is around 60 kg and in addition, it moves along the longitudinal axis independently from the hexapod movements. Therefore, the legs and their respective joints are facing varying mechanical loads. Rotary encoders implemented in the driving legs can only infer the linear extension by measuring the rotary motion of the screw drive inside the leg. This measurement does not take into account that deformations of the joints are varying and that the thermal impact, caused by motor, gearbox, and the stiff roller screw drive, causes expansions that affect the overall accuracy at the point of interest at the platform. This situation is independent of the kinematic model; serial kinematic stacks of individual single-axis positioners are even more affected.
To overcome the limitations, the task was to find a way to enable load- and travel-history-independent platform position measurement for all six degrees of freedom at large travel ranges.
3. Solution: Hexapod with 6 Additional Sensor Legs
As basis a tried and proven off-the-shelf design was chosen, the HP-550 high-load hexapod. It was modified with six additional non-motorized measurement struts. These linear sensors are directly attached between the bottom and top platforms and not affected by varying mechanical loads and thermal influences in driven legs. The measurement struts were designed carefully with play free joints and linear scales. A lightweight space-frame structure was chosen to support the linear measuring systems, reducing forces and torque caused by gravity to a minimum.
4. Results / Figures
Equipped with this solution, the hexapod achieves better overall positioning precision and repeatability independent of the travel-history. A positive side-effect was generated due to the oval design of the PKM. The achieved minimum incremental step size (MIM) for movements around the transverse axis (RotY) is less than 2 µrad, which is a great result for a hexapod in this payload-class.
The prototype of the Ovali hexapod achieved the results stated in Table 1. It has to be emphasized that travel ranges were customized to best fit the specific application. For some DoF, the required motion ranges were much smaller than for others – different requirements can be met with a modified design.
Table 1: Achieved metrology results
Video: 7-Axis motion system consisting of a custom PI Hexapod and PRS200 Rotary stage in a setup with 3D-printed phantoms imaged repeatedly with a cone-beam computer tomography scanner. More information on this research from Johns Hopkins University is available here: https://aiai.jhu.edu/research/#phantom and here: https://jhu.pure.elsevier.com/en/publications/assessment-of-boundary-discrimination-performance-in-a-printed-ph
Blog Categories
- Aero-Space
- Air Bearing Stages, Components, Systems
- Astronomy
- Automation, Nano-Automation
- Beamline Instrumentation
- Bio-Medical
- Hexapods
- Imaging & Microscopy
- Laser Machining, Processing
- Linear Actuators
- Linear Motor, Positioning System
- Metrology
- Microscopy
- Motorized Precision Positioners
- Multi-Axis Motion
- Nanopositioning
- Photonics
- Piezo Actuators, Motors
- Piezo Mechanics
- Piezo Transducers / Sensors
- Precision Machining
- Semicon
- Software Tools
- UHV Positioning Stage
- Voice Coil Linear Actuator
- X-Ray Spectroscopy