Engineered Motion Systems, Multi-Axis Automation Systems
Performance Automation: Precision Motion Systems for High Speed and High Precision Positioning and Automation
PI is a supplier of high-performance granite motion systems and multi-axis motion systems used in precision positioning and automation applications. We use our in-house engineered positioning stages and motion controllers to provide customized positioning and automation sub-systems — “motion engines”—for our customers. The PI group employs over 1,300 people in 15 countries and runs engineering and manufacturing centers on 3 continents. Select from the broadest portfolio of precision motion technologies, including piezoelectric and air bearing systems, with 1,000’s of standard products or have our engineers provide you with a custom solution.
Applications of PI motion systems are found in the automation of processes in industries including:
Optics & Photonics, Semiconductor, Laser Machining, Micro-assembly, Electronics Test & Measurement, Medical Engineering, Bio-Tech, Life Sciences
Save Your Time – Get Free Advice from Our Engineers
There is no need to spend your time comparing the features, pros, and cons of all the different drive technologies and products we provide – unless you want to. Instead, talk to our engineers first. They have access to in-depth knowledge and test data on diverse driving and guiding technologies, spanning from electromagnetic to piezoceramic and from mag-lev to air bearings.

508-832-3456
or email ask-an-engineer
- Definition phase: Together, we identify current issues and/or the goal of your new motion system.
- Concept phase: Brainstorming about the best solution in close cooperation with you.
- The resulting solution is converted into a Technical and Business proposal.
- The design and detail phase begins after your approval.
- The system is then assembled, tested, and delivered.
- You end up with a fully functioning system, and don’t have to waste time trying to integrate components from different suppliers.
These applications often require large multi-axis precision positioning stages, or high-speed granite-based gantry motion systems, linear motor driven with air bearings or mechanical bearings. High speed, perfect path control, and exact synchronization with cameras or laser trigger events on a microsecond scale matter.
Examples of 3 motor gantries with linear motors:
- (left) with air bearings
- (middle) with mechanical bearings
- (right) customized XY-Z system for inspection applications
PI can provide the individual stage components, as well as the complete system including controls and software.
PI can provide custom multi-axis systems for applications related to semiconductor and silicon photonics wafer testing. For highest geometric performance, air bearings are available and optional piezo nanopositioning systems can provide millisecond responsiveness with resolution down to the picometer range.
Products manufactured in clean rooms and positioning systems for vacuum and UHV applications are also available.
Due to their geometric performance and frictionless motion, air bearings have played a crucial role in the development and construction of coordinate measuring machines (CMMs) and other metrology tools for decades.
As the precision requirements in the automotive industry are increasing, the need for advanced robotics arises. Traditional robots are fast, can handle heavy loads, but lack positioning accuracy. Hexapod robots have a long history in precision alignment & micro-manufacturing automation, but were considered too precise for the automotive industry. The situation is rapidly changing.
Best of two worlds example: Combination of a traditional articulated-arm robot with a hexapod parallel-robot provides long travel ranges and very high precision and flexibility.
These applications often require hexapods, multi-axis precision positioning stages, or gantries, linear motor driven with air bearings or mechanical bearings. High speed, perfect path control, and exact synchronization with cameras or laser trigger events on a microsecond scale matter.
Additive nano-manufacturing and laser micromachining are disrupting technologies that both rely on precision motion control and positioning equipment. In the case of laser cutting, long-travel ironless linear motor stages virtually extend the field of view of a high-speed galvo scanner. The key to high accuracy and throughput lies in the synchronization of the scanner and the motorized positioning system.
The latest generation of linear motor stages designed for laser micro-processing and machine building applications
At the nanometer level, multi-axis piezo-mechanic nanopositioning systems make possible 3D nano-manufacturing based on laser lithography. Focus and path precision are extremely critical requiring mechanics and servo electronics to provide nanometer precise trajectory control.
Advances in drug discovery rely on analysis of huge amounts of data and before that testing of large amounts of samples. Increasing the throughput of these tests, requires highly repeatable ways of focusing down to sub-micrometer precision in milliseconds for perfect optical data acquisition. PI has designed piezoelectric drives and voice coil drives specifically for fast microscope automation applications.
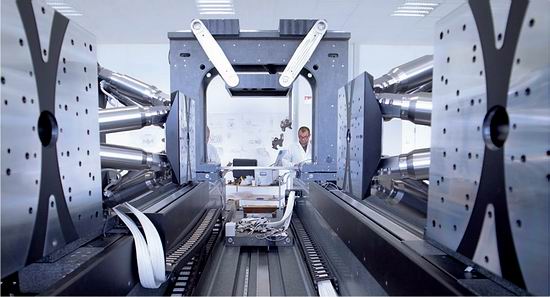
MiQA is a 20-ton, 56-axis motion system of extraordinary precision, designed for for x-ray microscopy and quality assurance of x-ray optics. The system is equipped with 56 motors 16 controllers, 7 air bearing granite slides. In order to achieve this performance, the entire spectrum of PI’s precision technologies is put to use. When operated in “Tomography Mode” the sample’s point of interest can be held inside a sphere with the diameter of 85 nanometers. This extraordinary performance – considering the size of the machine - is an example for what our engineers can achieve based on the broad spectrum of precision technologies they have at their disposal.