Metrology and Test Equipment for Qualifying Nanopositioning and Motion Control Systems
Part 1: What Tools are Required
When it comes to high performance motion control and nanopositioning equipment, test and metrology data matter, as much as the methods used to acquire the data. PI engineers have been working for years on better ways to measure the figures such as dynamic performance, precision, resolution, repeatability but also geometric accuracy of all kinds of micropositioning and nanopositioning devices, from single axis motorized actuators to complex multi-axis parallel kinematic motion system.
When each individual measurement and qualification step is seen as an instrument for quality assurance, only motion systems and nanopositioning components within the guaranteed specifications will reach the customer.
Depending on the type of motion control component of positioning system, different criteria apply and for highly dynamic applications, rise time, settling time, resonant frequency and body plots may be important, while for static applications stiffness, long term stability, and maximum load and position hold capability without power can be more meaningful.
In either case, the accuracy of the measuring equipment should be significantly better than the component that needs to be tested, in terms of stability, resolution, linearity, etc.
1 Measuring Environment
1.1 Nano-Metrology Labs
Nanometer accuracy cannot be tested on an office desk. As the basis for high precision measurements, PI designed special nanometrology labs, with multiple vibration and temperature isolation functions. Anyone who has spent time at the top of a tall TV/radio tower can understand that the place with the lowest amount of vibration and motion is usually found in the basement of a building, which is where the highest performing PI nanometrology labs are located. By separating the foundation of the lab from the rest of the building, seismic influences from the outside are further suppressed. Equipment is mounted on vibration isolated honeycomb tables. A room-in-room design with two stage air conditioning ensures temperature stability better than 0.25 Kelvin over a period of 24 hours. 15 special measuring laboratories are available at PI's headquarters in Karlsruhe alone, with additional labs in its engineering and production facilities in USA and Asia. Five measuring laboratories with special seismic, electro-magnetic, acoustic and thermal isolation allow measurements down to the picometer range and long-term positional stability tests with nanometer precision which is only possible under such conditions.
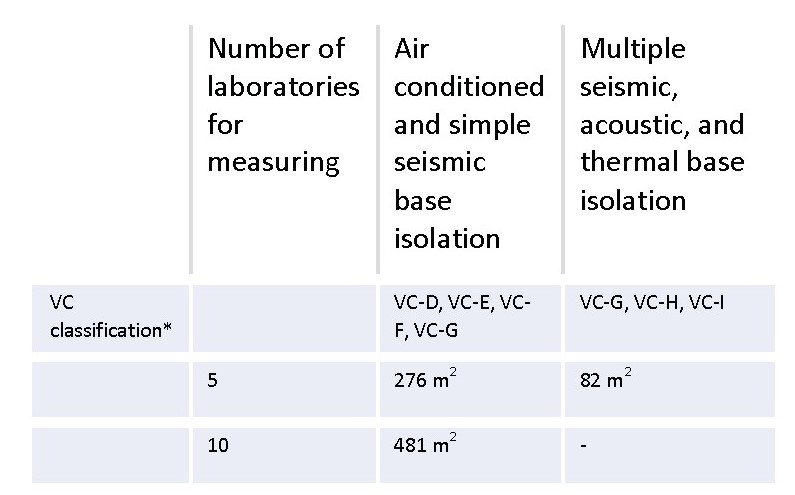
1.2 Measuring Technology in the Production Environment
In (large) series production, a significant part of the tests already take place directly in the production environment allowing deviations in the process to be detected immediately, enabling high yield, and reducing rejects and costs for reworking.
For this purpose, PI develops fully and semiautomatic measuring and test stations that are validated for their suitability before they are used in production.
1.3 Overview of Measuring Capabilities under Specifically Designed Environmental Conditions
A great variety of different measurements need to be conducted under specific ambient conditions. This is where the great variety of test tools in our different application laboratories is key. Vacuum chambers with a base pressure to 10-11 hPa allow functional tests and residual gas analysis, which is very important for applications such as crystallography, semiconductor technology or optical coating. Cryogenic chambers are available for low temperature examinations down to 77 °K (condensation point of nitrogen) allowing startup, function tests, and lifetime tests under extreme conditions.
1.4 Special Equipment
A high load lift and swivel table allows with a load capacity of 5000kg allows qualifying of positioning systems at random angles with application-specific alignment and load. In a special heavy-load hall, three gantry cranes span the working area, and lift and transport the components of the high load precision positioning systems.
2 Measuring Equipment
All measuring equipment is subject to recalibration (ISO9001) guaranteeing meaningful results with minimal uncertainty and high reproducibility with respect to national and international standards. Interferometric measuring systems are frequently used due to their high resolution, bandwidth, and noncontact, wear-free nature.
2.1 High End Measuring Equipment
In addition to standard measuring tools, PI has access to high end metrology tools. Here are a few examples.
- We use laser scanning vibrometers, for high dynamic measurements. They provide insights into unwanted vibration modes and help to improve the structural rigidity of our high precision motion products. We also use them to analyze the motion characteristics of piezoelectric transducers and ultrasonic piezoceramic motors.
- Special capacitive gauges and software are used to analyze eccentricity and wobble of rotary tables.
- 3D CMMs (coordinate measuring machines) are used for incoming inspection and for multi-degree of freedom motion systems.
- White light interferometers are available for surface topology analysis and for material research.
- A 6-Axis laser tracker is available for the qualification of multi-axis motion systems and 6-DOF hexapod parallel robots.
3 Evaluation of the Measured Data
The ISO 230-2 and VDI/DGQ 3441 standards are the basis for qualification of PI products and evaluation of the measurands. The qualification data is always verifiable for each individual product. The measured data is compiled in a database and used for process control. Traceability at product level is particularly important for large production runs. The metrology report is provided with all high-performance motion and piezo nanopositioning systems many systems.
3.1 Acquiring Measuring Data and Statistical Process Control
Measuring data is transmitted in real time, saved to a database, and visualized on a web-based user interface. Production and test engineers have immediate access to all process data and can intervene immediately if necessary.
- Automatic saving of the measured data after measuring
- Real-time display of the measured values in the control charts
- Multi-control charts for maximum process control
- Dynamic calculation of warning and intervention limits
- Download of raw data and customer log
- Calculation of process capability Cpk level
- Pareto chart for process analysis and optimization
- Correlation chart to check the dependence of two measurands
- Various export functions
3.2 Measuring Software
The software for controlling the fully and semiautomatic test and measurement stations is developed in-house by PI. All measuring equipment can be configured directly and polled from the software, eliminating possible error sources between for test location and database. Software development makes use of current development standards such as version control systems, bug tracking, automatic build systems, static code analysis, unit tests, and code reviews. This ensures that the software is always traceable and the quality standards are adhered to.
Additional details on metrology for nanopositioning equipment are found here: Measurement Standards for Precision Motion Control Systems
Blog Categories
- Aero-Space
- Air Bearing Stages, Components, Systems
- Astronomy
- Automation, Nano-Automation
- Beamline Instrumentation
- Bio-Medical
- Hexapods
- Imaging & Microscopy
- Laser Machining, Processing
- Linear Actuators
- Linear Motor, Positioning System
- Metrology
- Microscopy
- Motorized Precision Positioners
- Multi-Axis Motion
- Nanopositioning
- Photonics
- Piezo Actuators, Motors
- Piezo Mechanics
- Piezo Transducers / Sensors
- Precision Machining
- Semicon
- Software Tools
- UHV Positioning Stage
- Voice Coil Linear Actuator
- X-Ray Spectroscopy