Piezoelectric materials, like most electro-ceramics, do not show perfectly linear displacement behavior compared to the input voltage. Closed-loop operation with position feedback usually takes care of the nonlinearities. Although perfect settling to the desired position is achieved to nanometric scale in positioning operation, the deviation in dynamic continuous motion operation can in some cases be considerable. For high-dynamics applications, bandwidth limitations of the controller and the piezo mechanism can be limiting factors. Several control methods are now available in commercially available controllers to significantly increase dynamic accuracy, linearity while reducing phase errors. Simple methods, such as feedforward, can only reduce the phase difference control input signal and motion output.
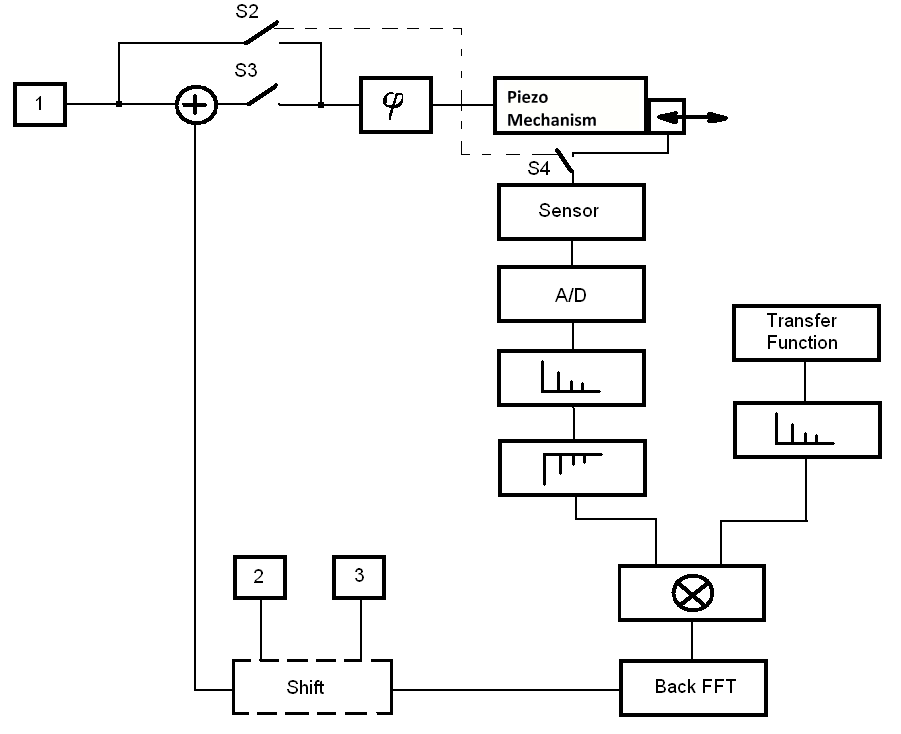
Signal Preshaping
Signal Preshaping, a patented technique, can reduce rolloff, phase error, and hysteresis in applications with repetitive (periodic) inputs. Signal Preshaping is implemented in object code, based on an analytical approach in which the complex transfer function of the system is calculated, then mathematically transformed and applied in a feedforward manner to reduce the tracking error. Signal Preshaping is not to be confused with phase-shifting approaches and can improve the effective bandwidth up to 10 times and more, especially in tracking applications such as precision, particularly in precision contouring (out-of-round finishes) of mechanical and optical parts. With this technique, it is possible to increase the command rate for a piezomechanism with a natural frequency of 400Hz from 20Hz to 200Hz without compromising stability. At the same time, the tracking error is reduced by 50 fold.
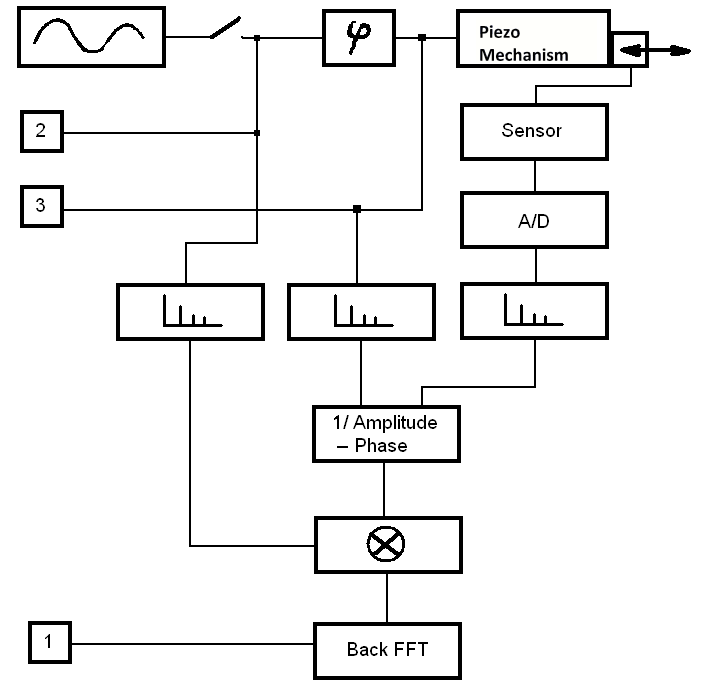
The technique is based on Fast Fourier Transformation (FFT) and external metrology. Frequency response and harmonics (caused by material nonlinearities) are determined in two steps. The data gathered by FFT are then applied to the original control signal to calculate the new, modified control signal. This new, pre-distorted control signal and the nonlinearty from the piezo material cancel each other out, resulting in a very linear response.
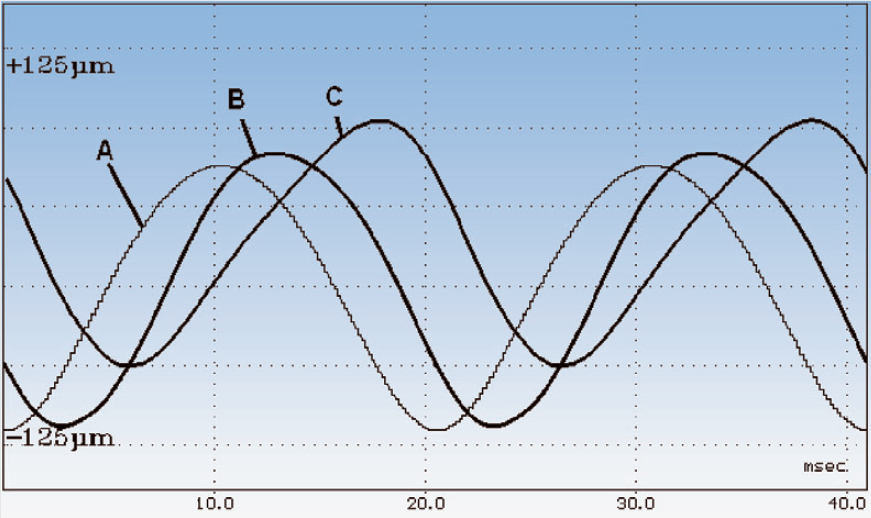

The Simple Integrated Solution: Dynamic Digital Linearization (DDL)
DDL is similar in performance to Input Preshaping, but requires no external metrology; instead it is embedded inside the firmware of the digital piezo motion controller (such as PI’s E-712). In addition, it can optimize multi-axis motion such as XY raster scans or tracing of shapes such as circles or ellipses. Learn more on digital vs. analog piezo controllers.
DDL significantly improves the performance for applications with periodic signals, where conventional piezo controllers cannot completely avoid phase-shift and tracking errors for higher frequency motion. This is caused by the limited control bandwidth of the servo system, the non-linear nature of the piezoelectric material, and the inherent limitations of PID (pro-Portional Integral Derivative) servo- control, which is reactive by nature, feeding off errors.
DDL works for periodic signals and uses the position information available from the highly linear capacitive position feedback sensors integrated in the piezo mechanism to calculate the optimum control signal. As with Signal Preshaping, the result is an improvement in linearity and tracking accuracy of up to three orders of magnitude (see graphs).
APC: Advanced Piezo Control: Advanced Algorithm for Faster Settling
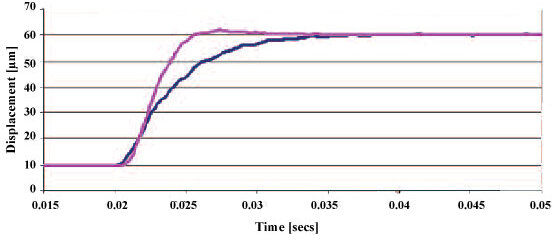
Advanced Piezo Control is an alternative closed loop algorithm based on a state controller which is, in turn, modelled on the positioning system. While conventional PID / notch filter concepts “cut” the mechanical resonance out of the excitation spectrum, APC actively damps these unwanted resonant frequencies.
The result is higher stability, faster settling, and lower sensitivity to external disturbances. In addition, there is significantly less phase shift compared to the damping based on one or multiple notch filters with positive effects on the trajectory trueness and the settling response.
APC provides most benefits over PID algorithms for mechanical systems with resonant frequencies below 1 kHz. It also has limitations when in the case of multiple, closely spaced resonances.
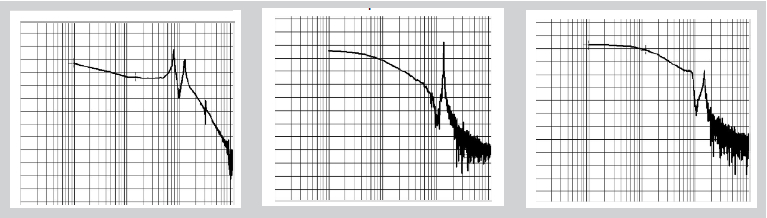
Higher Dynamics with Energy Recovery Driver Design
Most drive electronics for piezo actuators are based on linear amplifiers or charge amplifiers. For industrial 24/7 high dynamics applications, driving large capacitance actuators, the energy consumption can be a factor to be considered. With typical periodic dynamic applications and linear amplifiers, the energy to charge and discharge a piezo actuator is lost after each cycle – actually it is turned into heat that needs to be dissipated.
A new patented amplifier design with an energy recovery circuit is available with standard drivers covering up to 6KVA. The system is based on a combination of PWM (pulse width modulation) where the pulse width of the drive voltage is modulated and the relatively large piezo capacitance smoothes out the signal. In addition, a patented circuit for energy recovery is also integrated. It stores a portion of the returned energy when the piezo discharges in a capacitor, making it available for next charging cycle. The result is significantly higher efficiency with energy savings up to 80%.
Weight savings in the amplifier and significant reduction in the amplifiers heat dissipation are additional benefits. In contrast to conventional switched amplifiers (Class D), the new patented energy recovery piezo amplifier is run in both current and voltage control mode.
This is critical for applications in the field of active vibration control.
Additional Temperature Monitor to Protect the Piezo Mechanisms
The energy loss in static piezo operation is negligible. In continuous dynamic operation, especially with powerful drivers, it is recommended to monitor the temperature of the piezo mechanism. Integrated sensors are available to hook up to the driver and shut it down when a preset threshold is exceeded.
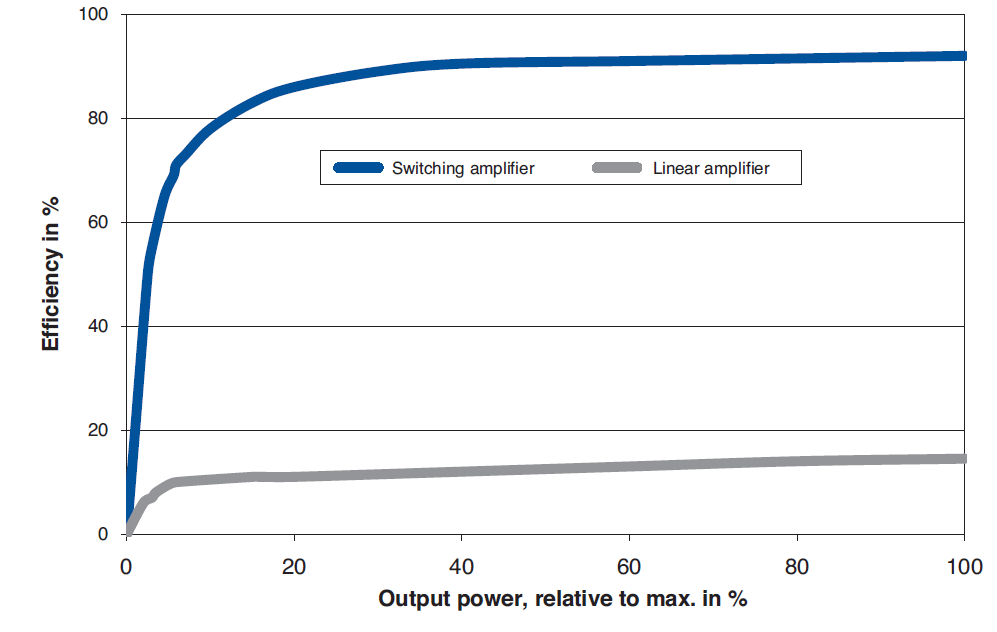
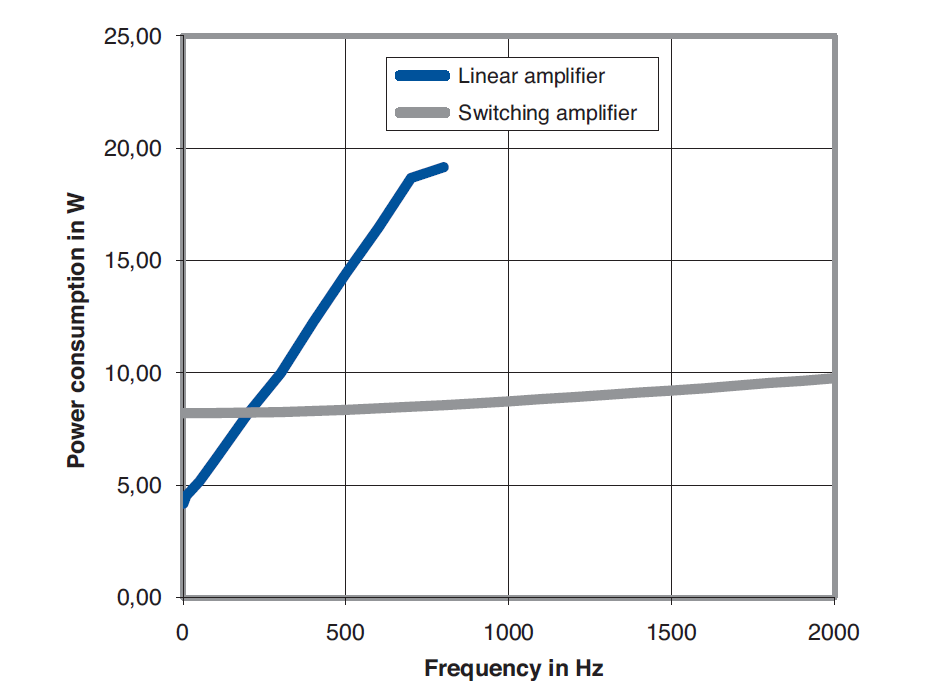
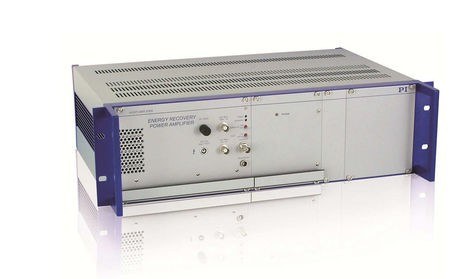
Blog Categories
- Aero-Space
- Air Bearing Stages, Components, Systems
- Astronomy
- Automation, Nano-Automation
- Beamline Instrumentation
- Bio-Medical
- Hexapods
- Imaging & Microscopy
- Laser Machining, Processing
- Linear Actuators
- Linear Motor, Positioning System
- Metrology
- Microscopy
- Motorized Precision Positioners
- Multi-Axis Motion
- Nanopositioning
- Photonics
- Piezo Actuators, Motors
- Piezo Mechanics
- Piezo Transducers / Sensors
- Precision Machining
- Semicon
- Software Tools
- UHV Positioning Stage
- Voice Coil Linear Actuator
- X-Ray Spectroscopy