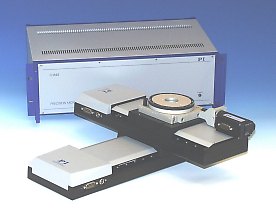
- Simultaneous Closed-Loop Control of up to 4 DC Servo Motors
- Fast 32 bit Digital PID V-ff Servo Loop
- Integrated Linear Power Amplifiers (12 bit) and PWM Outputs
- Trapezoidal-Curve, S-Curve & Velocity Contouring
- LabViewä Drivers, Libraries for C, PASCAL etc.
- IEEE-488.2 and RS-232 interfaces
- SCPI Command Language
- Non-Volatile Macro Command Storage
- 16 I/O Lines for Flexible Automation
- 4 Analog Input Lines (10 bit)
- 12 TTL Inputs for Limit & Origin Switches
- Electronic Gearing
- Programmable Torque Limit
A successor to the C-844 controller is here:
C-844 is a programmable multi axis motion controller for DC servo motors and can be used for general positioning tasks in research and industry.
C-844 is based on a multi-processor architecture including a fast DSP motion control chip set (providing trajectory generation and closed loop digital servo control based on position information supplied by incremental feedback encoders) and a host processor for communication and command handling.
The host processor provides flexible and fast high-level command handling and advanced features such as stackable macro commands (up to 16 macros, up to 100 commands per macro, non-volatile storage). The command language complies with the SCPI (Standard Commands for Programmable Instruments) standard which is a user-friendly tree-structured language reflecting the device functionality. The C-844 is prepared for future firmware updates via the RS-232 interface.
Learn more about advanced motion control algorithms and motion systems for PCB board manufacturing
C-844 servo controller offers advanced features such as S-curve profile generation, electronic gearing, velocity contouring, real time origin position capture, and fast 32-bit PID + V-ff servo control (parameters can be changed on-the-fly). They are ideally suited for multi-axis precision positioning stages.
Integrated, low noise, 15-Watt linear power amplifiers allow operation of all PI micropositioning systems without additional external amplifiers, reducing costs and simplifying the set-up.
In addition to the analog motor output, PWM (Pulse Width Modulation) output signals are available to drive fast PI micropositioning stages with integrated PWM power amplifiers (Active Drive) or external PWM power amplifiers from other manufacturers.
More information on motion control software tools from PI
SCPI Command Language
C-844 multi-axis motor controllers are computer controlled by the SCPI (Standard Command language for Programmable Instruments) language. This language is well established for instruments such as oscilloscopes, signal generators, programmable power supplies, etc. and saves valuable programming time by its simple and easy to remember structure.
Examples:
TARG 5000
Moves motor to position 5000
TARG:RPOS 250
Moves relative to current position 250 counts
OUTP:SERV ON
Activates the servo loop
TARG?
Reads the target position
MVEL 75000
Sets the maximum velocity to 75000 c/s
MVEL?
Reads programmed maximum velocity
ORDERING INFORMATION:
C-844.40 4-Axis Closed-Loop Servo DC Motor Controller, 19" Rack Mount, RS-232 and IEEE 488
C-844.20 2 Axis Closed-Loop Servo DC Motor DC Motor Controller, 19" Rack Mount, RS-232 and IEEE 488
TECHNICAL DATA: C-844 | |
Function | rack mountable DC-Servo Motor Controller |
Channels | 2 (C-844.20); 4 (C-844.40) |
Servo characteristics | 32 bit programmable PID V-ff filter, 100 m s/ enabled axis; |
Profile modes | trapezoidal, S-curve, velocity contouring, electronic gearing |
Output power / resolution | analog H-bridge ± 12 V, 15 Watts/channel, 12 bit D/A converters, |
Current limitation | 1.8 A peak (short circuit proof) |
Encoder input | AB (quadrature) TTL signals (single ended or RS-422 differential mode), max. 106 counts / sec |
Stall detection | Motor stop, servo on, triggered by programmable position error |
Limit switches | 8 TTL (pull-up/ pull-down, programmable), programmable soft limits |
Origin switches | 4 TTL (pull-up/ pull-down, programmable), real time position capture |
I/O ports | 8 TTL inputs, 8 TTL outputs (pull-up) |
Analog input | 4 channels, 5V unipolar, 10 bit ADC |
Motor brake output | 15 V, software controllable |
Trajectory monitor output | encoder frequency/voltage conversion (0 to 12 V) for settling analysis purposes, etc. |
Interface / Communication | RS-232 (cable included), IEEE 488.2 |
Command Set: | > 100 SCPI commands, ASCII format, firmware updates by RS-232 possible |
Macro command capability | 16 stackable macros in non volatile RAM, up to 100 commands per macro |
Motor connectors | one 15 pin (f) D-sub per channel |
Output safety options | amplifier enable/disable (by software) |
Internal safety options | servo amplifier over-temperature shut-down |
Heat sink | internal heat channel with temperature controlled fan |
Operating voltage | 90 to 264 VAC, 50 to 60 Hz, wide range P/S |
Dimensions | 288x450x158 mm (19" rack mountable) |
Weight | 6.7 kg |
DCMove Interactive Operating Program (included)
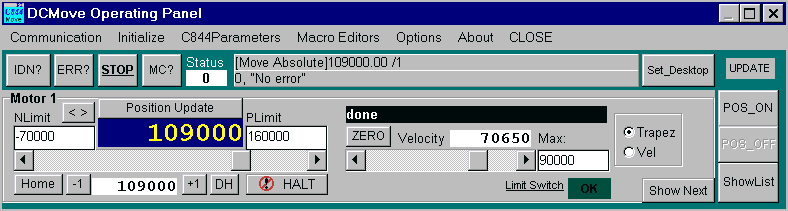
DCMove is a general purpose operating program for positioning tasks. It provides a set of mnemonic short form commands for easy parameter setting and operation. A variety of push buttons, slide bars and parameter tables controls all motors by a mouse click. Online status displays and position displays offer a comprehensive view of the overall positioning system.
DCMove allows single command execution and macro command file handling for multi axis motion. Complex positioning procedures can be programmed using stackable macro command loops.
DCMove runs under Windows 95™ and Windows 3.1™.
WinTerm Terminal Program (included)
WinTerm is a Windows Terminal Program providing both RS-232 and IEEE 488 communication. All commands can be edited in a terminal window, responses send by the motor controller are displayed in an output window.
WinTerm runs under Windows 95™ and Windows 3.1™.
Dynamic Link Libraries (included)
16 and 32 bit DLL Libraries are provided for easy communication with the C-844. They also guarantee compatibility with programs written for the C-842 motor controller card and former PI DC motor controllers such as C-832.
C-844.LV LabView™ Drivers
A comprehensive set of virtual instruments offers LabViewä programmers access to the functions of the C-844. Serial and IEEE 488 communication are supported. C-844.LV LabViewä drivers are available at no charge (please order separately).
This is a legacy product that may have limited availability or may have been replaced. Ask a PI engineer for an equivalent new model.
Precision Motion Controller Overview