PI’s high-performance direct-drive motorized linear actuators provide a unique combination of high accuracy and velocity. Multiple drive concepts are available: compact direct-drive linear actuators based on voice-coil linear motors, for strokes from a few millimeters to an inch and longer stroke actuators based on 3-phase linear motors. Both linear motor types are frictionless and wear free. Guiding systems usually consist of highly accurate crossed roller bearings. For the ultimate precision, performance and lifetime, completely wear free air bearings and flexure guiding systems are also available. PI also offers high precision, rod-type ball-screw linear actuators and rod-less linear module actuators. All units come equipped with direct-measuring linear incremental encoders or absolute encoders for the highest closed-loop precision and step and settle performance.
Fast, Compact Rodless Direct-Drive Actuators driven by Voice-Coil and 3-Phase Linear Motors
Travel Ranges 7mm to 25mm – Crossed-Rollers and Air Bearing Options
These rodless compact direct-drive actuators use cross-roller bearings and air bearings for the highest geometric accuracy (straightness, flatness) as well as excellent repeatability. High resolution, closed-loop linear encoder feedback makes them a premier choice for precision nanopositioning requirements. Motion ranges from 7mm to 25mm (1 inch).
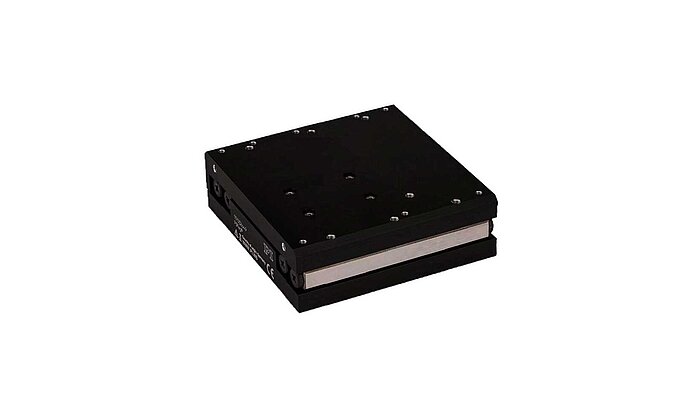
V-141 Low-Cost Linear Motor Stage
Compact, High Force, 80mm Width
40, 60, and 100mm travel
120nm bidirectional repeatability
2µm accuracy
1m/sec max. velocity
Up to 45N push/pull force
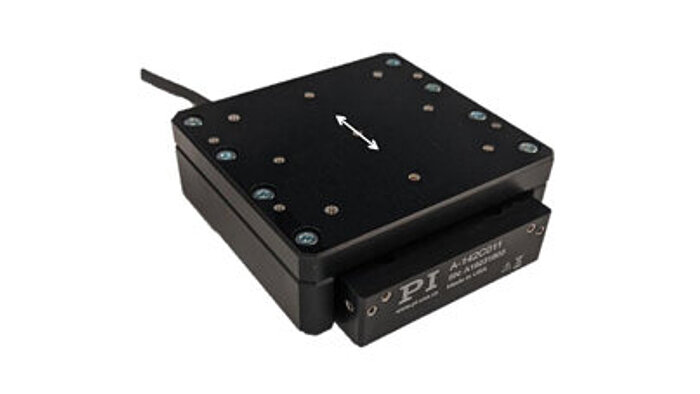
A-142 Mini Voice Coil Linear Slide
Air Bearings, Frictionless, Fast
- 10mm travel
- 3kg load
- 5nm encoder, 0.1µm straightness
- 75x80mm table; 27mm height
- 450mm/sec, 2g acceleration
- 20N push/pull force
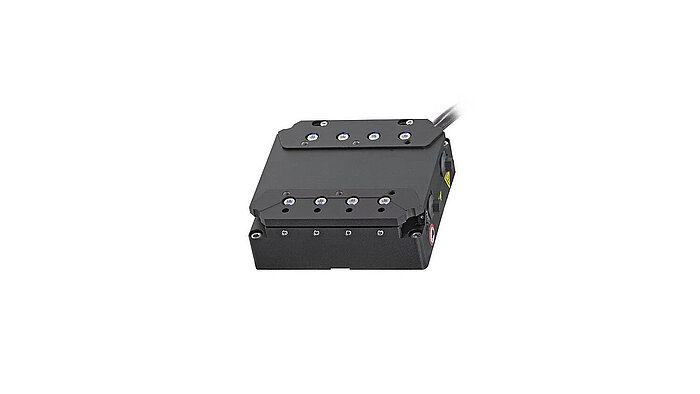
V-308 Fast Scanning Stage
Integrated Counterbalance
- 7mm motion
- Voice coil linear motor
- Adjustable Z-counterbalance
- Millisecond settling time
- 1nm sensor resolution
High Speed Rodless Motorized Linear Actuator Modules for Long Travel Ranges to 800mm
Ideal for Performance Automation Applications
These fast, rodless motorized direct-drive linear actuators are driven by a high speed 3-phase linear motor and can achieve velocities to 5m/sec, fast acceleration up to 5g’s, and travel ranges up to 1.2m (47”). Three-phase electromagnetic linear motors work on a non-contact principle and provide high speed motion and extremely long lifetime. They are ideal for high performance, precision automation applications. All units are equipped with linear encoders for position feedback.
The direct-drive linear modules use a single guiding rail and are well suited as high performance actuators and can form the basis of a gantry system.
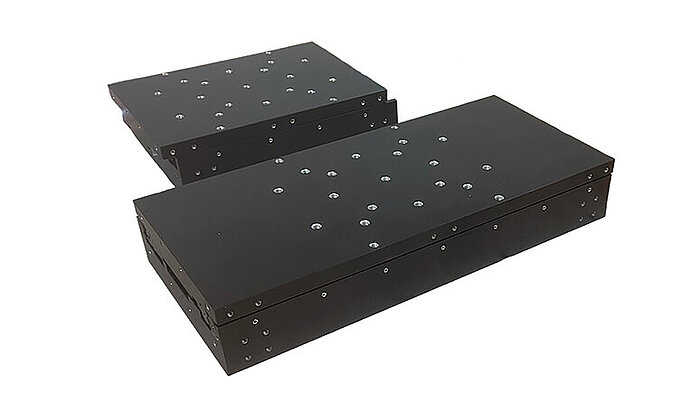
V-574 Linear Motor Stage
160mm Stage Width
- 1 - 1.5µm straightness
- 60/130/230mm travel
- 80nm bidirectional repeatability
- 1nm absolute encoder resolution
- 1m/sec max. velocity
- 58N push/pull force
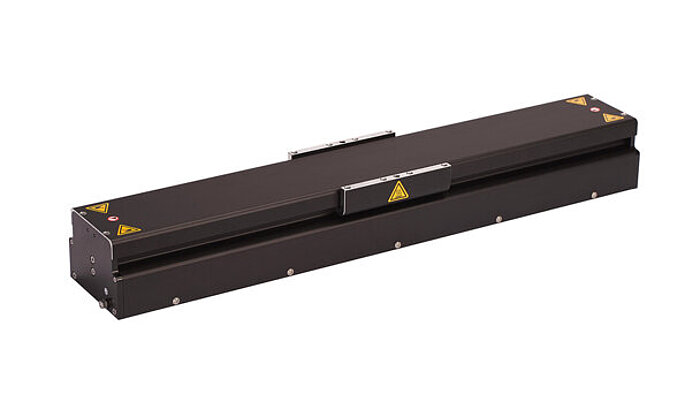
V-855 High-Speed Linear Module
Linear Motor, 4m/sec 600N Load
- 200 - 800mm travel
- 0.1µm min. inc. motion
- <1nm encoder res.
- 4m/sec max. velocity
- 90N peak force
- Excellent value for precision automation
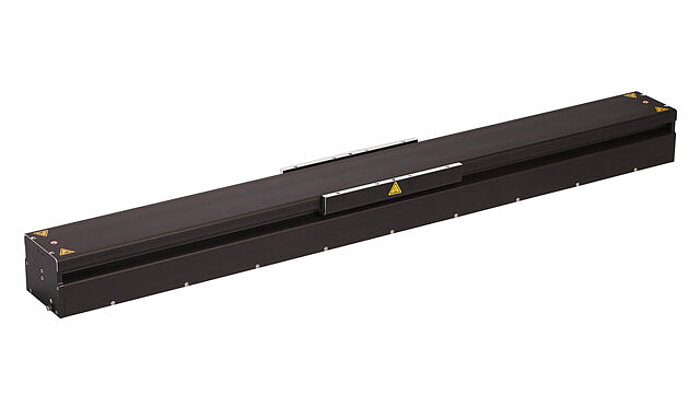
V-857 High-Speed Linear Module
Linear Motor, 5m/sec 1000N Load
- 400 - 800mm travel
- 0.1µm min. inc. motion
- <1nm encoder res.
- 5m/sec max. velocity
- 420N peak force
- Excellent value for precision automation
Compact High-Speed Actuators Based on Voice-Coil Linear Motors
Travel Ranges to 1 Inch with Force Control Option
PI provides direct-drive voice coil linear actuators with mechanical bearings and for the highest performance requirements offers friction-free and wear-free flexure guides and air bearing guides. These actuators are fully self-contained and PI can provide custom voice coils and linear motors for OEM precision motion applications. All direct-drive zctuators are equipped with direct position feedback for closed-loop servo control, and we offer a closed-loop force control option on some of these models.
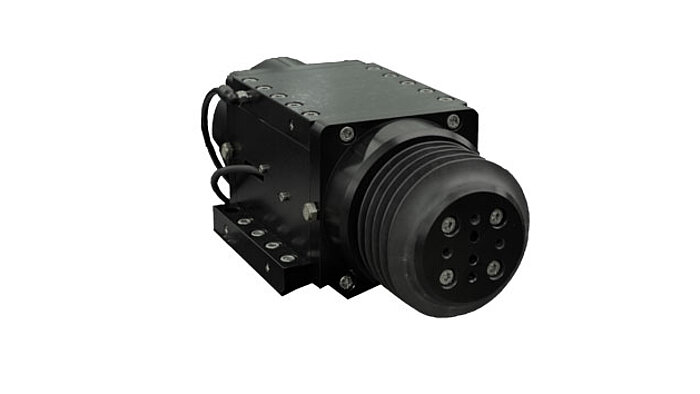
A-131 Voice Coil Positioner
For Fast Scanning/Autofocus
- 1” travel
- Optional bellows
- 1nm resolution
- 8g max. acceleration
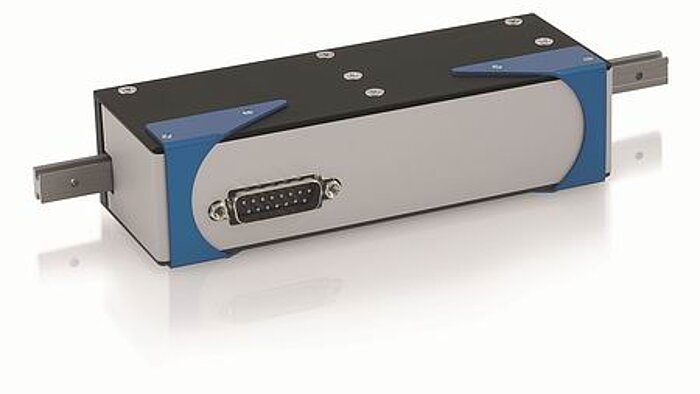
V-273 Voice Coil Actuator
Force Sensor Option
- 20mm travel
- 10nm linear encoder resolution
- 100mm/sec max. velocity
- 6N push/pull force
- 1mN force sensor option
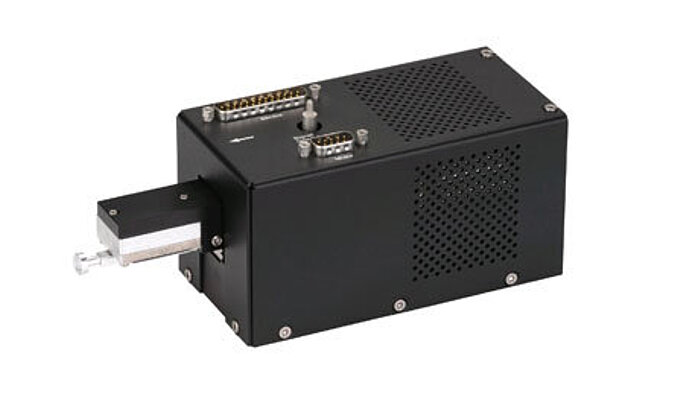
V-277 Voice Coil Actuator
High-Speed, Force Sensor Option
- 15mm travel
- 10nm linear encoder resolution
- 750mm/sec max. velocity
- 20N push/pull force
- 1mN force sensor option
PI provides a number of standard motion and position controllers for linear motor actuators and voice coil actuators. In addition to fully contained controllers, OEM controllers and modules are available. Labview, Matlab, etc., software packages, drivers and support are available, too.
What are High Speed Precision Actuators?
High-speed precision actuators are positioning, motion, and automation devices that create motion in response to a control signal, and are specifically designed to provide high acceleration and velocity to move quickly and accurately. They convert different types of energy – usually electrical, but sometimes also pneumatic or hydraulic – into mechanical motion or force. Here we are focusing on electrically controlled actuators because of their compact size and ease of controllability. The actuators covered here are not designed for consumer applications but for high-tech industrial and research applications.
High speed actuators are often used in industries that require precise and rapid movement, such as robotics, optical test and production equipment, aerospace, medical devices, and manufacturing processes. They can be used for a variety of applications, such as moving a tool to a certain position, adjusting the focus in optical devices, or controlling a valve in an industrial process (for high speed dispensing and nanoliter dosing applications, piezoelectric actuators and voice coil actuators are best suited).
The "precision" part of the name refers to the actuator's ability to reach a specific position or apply a specific force accurately and repeatably. Here, the mechanical design but especially the position feedback system such as a linear encoder or high resolution LVDT or capacitance sensor and the capabilities of the motion controller are essential. The "high-speed" part of the name refers to the actuator's ability to make these precise movements quickly, which is related to motor design and power, but also to controller bandwidth, algorithms, and output capabilities. Together, these characteristics enable actuators to perform tasks with a high degree of accuracy and at a high acceleration and velocity.
Several different technologies can be used to achieve these capabilities, including piezoelectric materials, voice coil actuators, linear motors, and more. The exact design of a high-speed precision actuator can vary widely depending on the specific requirements of the application.
Before You Buy
Consider your application requirements carefully, including travel range, force output, load capacity, duty cycle, frequency range, step-and-settle performance, environmental demands (vacuum, clean room, temperature range), and control system. Always discuss your actuator requirements with a knowledgeable engineer at a reputable manufacturer to ensure you choose the most suitable linear actuator for your application. Don’t forget to check the level of technical support provided by the manufacturer, as well as the warranty terms. For a more comprehensive overview of actuator types including screw type and piezomotor actuators, see our linear actuators buyers guide.