Resolution
Since the displacement of a piezo actuator is based on the orientation of electrical dipoles in the elementary Piezo cells, the resolution depends on the electrical field applied and is theoretically unlimited. Infinitesimally small changes in operating voltage are converted to a smooth linear movement.
No threshold voltages influence the constant motion.
Piezo actuators are used in atomic force microscopes to produce motion less than the diameter of an atom. Since displacement is proportional to the applied voltage, optimum resolution cannot be achieved with noisy, unstable voltage sources.
The above presented performance can only be provided by frictionless and stictionless solid state actuators such as PZTs. "Traditional" technologies used in motion positioners (stepper or DC servo motor drives in combination with dovetails, ball bearings, and roller bearings) all have varying degrees of friction and stiction. This fundamental property limits resolution, causes wobble, hysteresis, backlash, and an uncertainty in position repeatability - limiting their practical usefulness to a precision of two orders of magnitude less than with PI Piezo NanoPositioners.
Amplifier Noise
As stated above, amplifier noise directly influences the position stability (resolution) of a piezo actuator. Some vendors specify the noise value of their Piezo driver electronics in millivolts. This information is of little use without spectral information. If the noise occurs in a frequency band far beyond the resonant frequency of the mechanical system, its influence on mechanical resolution and stability can be neglected. If it coincides with the resonant frequency, it will have a more significant influence on the system stability. Therefore, meaningful data can only be acquired if resolution of the complete system – piezo actuator and drive electronics – is measured in terms of nanometers rather than millivolts.
Displacement of Piezo Actuators (Stack & Contraction Type)
PI PZTs are designed for industrial reliability. Displacement, operating voltage range and load capability in the technical data tables are realistic figures with regard to safe operation in conditions not restricted to research labs. Since we manufacture our own ceramics (in contrast to most other Piezo vendors) we can easily modify material parameters to trade lifetime for displacement. When you are looking for piezo actuators to be included in your application, "Maximum Displacement" may not be the only important design parameter.
Displacement of Piezo ceramics is a function of the applied electric field strength E, the piezoelectric material used and the length L of the Piezo ceramics. The material properties can be described by the piezoelectric strain coefficients dij. These coefficients describe the relationship between the applied electrical field and the mechanical strain produced.
The displacement DL of an unloaded single layer piezo actuator can be estimated by the equation:
DL = S*Lo ~~ ±E*dij*Lo (4-1)
Where
S = strain (relative length change DL/L, without Dimensions)
Lo = ceramic length [m]
E = electrical field strength [V/m]
dij, = material properties
d33 describes the strain parallel to the polarization vector of the ceramics (thickness) and d31 the strain orthogonal to the polarization vector (width). d33 and d31 are sometimes referred to as "piezo gain". The strain coefficient d33 applies for Piezo stack actuators, d31 applies for tube and strip actuators.
Note:
For the material used in standard PI piezo actuators, d33 is on the order of 450 to 650 x 10-12 m/V, d31 is on the order of -200 to -300 x 10-12 m/V. These figures only apply to the raw material at room temperature under small signal conditions.
For standard PI PZTs, the allowable field strength ranges from 1 to 2 kV/mm in the poling direction and up to 300 V/mm inverse to the poling direction (semi-bipolar mode), see Fig. 4.19/2 for details. The maximum voltages depend on the ceramic properties and the insulating materials. Exceeding the maximum voltage may cause dielectric breakdown and irreversible damage of the Piezo.
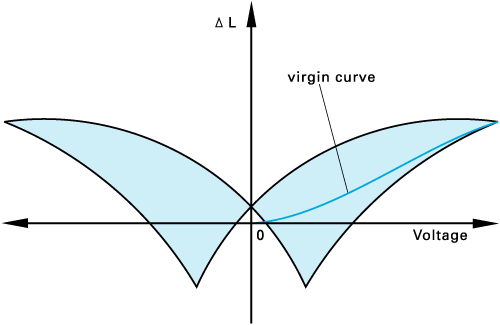
With the inverse field, negative expansion (contraction) occurs to yield an additional 20 % of the nominal displacement. If both the regular and inverse electric field are used, a relative expansion (strain) up to 0.2 % is achievable with Piezo stack actuators.
Stacks can be built with as aspect ratios up to 12:1 (length:diameter). Maximum travel for medium size stack piezo actuators (15 mm diameter), is therefore limited to approximately 200 mm. Longer travel ranges can be achieved by mechanical amplification techniques.
If you have any questions, ask a PI engineer for help.