Linear Piezo Stages for Nanopositioning (Flexure Guided)
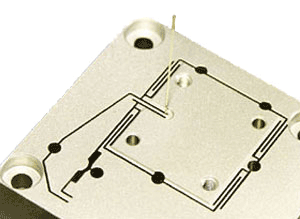
The linear piezo stages shown here are flexure-guided nanopositioning mechanisms, driven by integrated piezo stacks. Direct-drive (faster response and higher stiffness) and motion-amplified designs (longer travel ranges) are available. Flexure-guided piezo stages are frictionless, backlash and maintenance free, and provide better straightness and flatness of motion compared to linear stages employing mechanical guiding mechanisms. For highest linearity, resolution, and repeatability in the nanometer realm, non-contacting position sensors are integrated in the piezo linear stages to provide closed-loop control with our line of advanced piezo servo controllers.
PI’s piezo flexure nanopositioners provide excellent responsiveness and step/settle times typically in the millisecond range (and below for direct drive mechanisms), minimal tilt and out-of-plane motion, all based on zero-wear components.
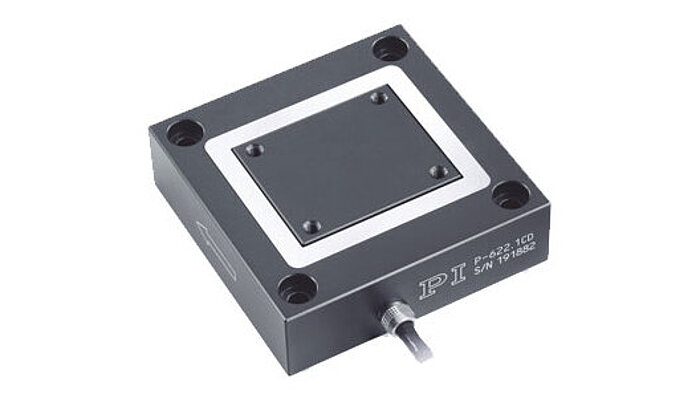
PIHera Piezo Nanopositioning Stage
Compact, High Performance
- 50µm to 1800µm motion range
- Closed-Loop, capacitive feedback
- <1 nanometer resolution
- Frictionless precision flexure guides
- X, XY, Z, XYZ combinations
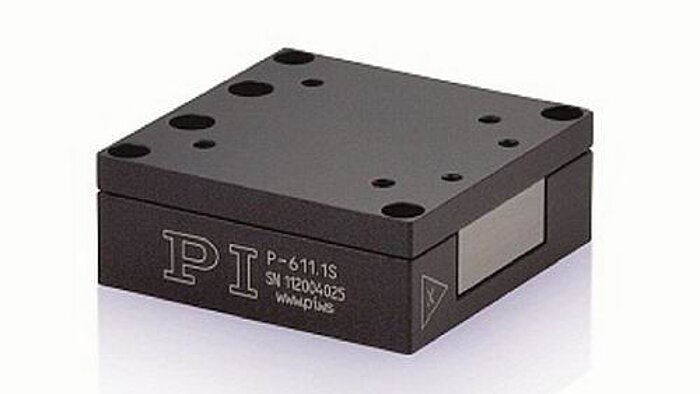
P-611 Piezo Nanopositioning Stage
Compact, Low Cost
- 100µm motion range
- For cost-sensitive applications
- Small footprint: 44x44mm
- <1 nanometer resolution
- Z, XZ, XY, XYZ options
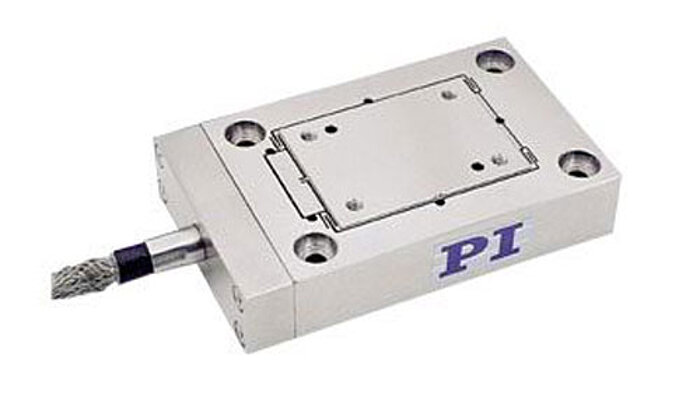
P-752 High Dynamics Piezo Stage
Direct Drive = Highest Performance
- 30µm motion range
- Ultra-fast response
- Ultra-precise trajectory control
- Direct-capacitive feedback
- 0.1 nanometer resolution
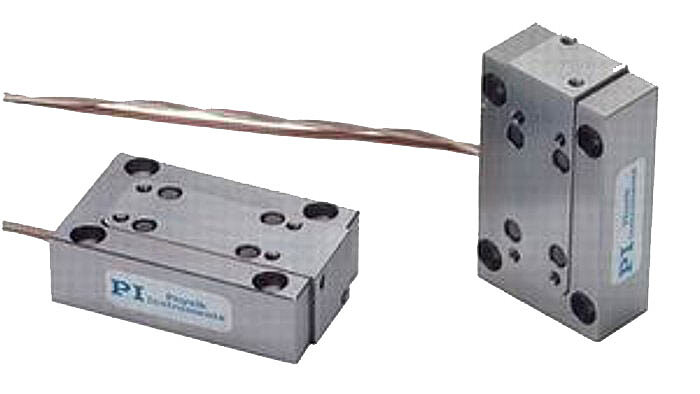
P-753 Piezo Flexure Stage/Actuator
Direct Drive, High Dynamics
- 38µm motion
- 0.05nm resolution
- Direct drive = Ultra-fast response
- Frictionless precision flexure guides
- Capacitive direct metrology
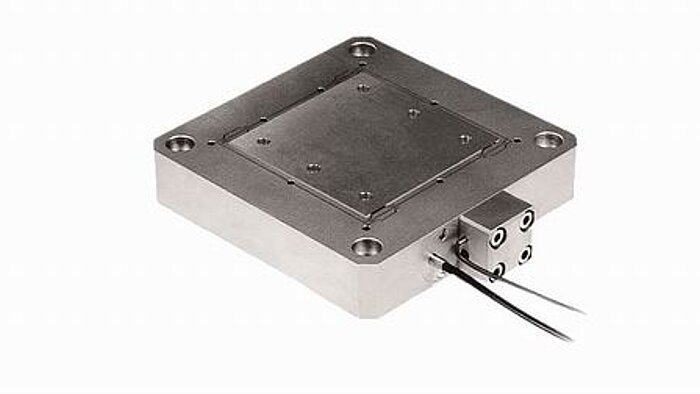
P-750 High-Load Piezo Stage
Direct Drive, Direct Metrology
- 75µm motion range, direct drive
- 10kg load capacity
- 1 nanometer guiding precision
- <1 nanometer resolution
- PICMA® long-life piezo drives
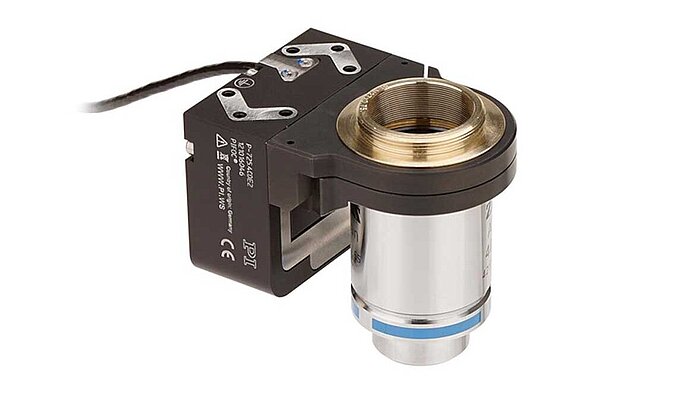
P-725 High Performance Piezo Focus Scanner
Up to 800µm, Sub-Nanometer Precision
- 100, 400, 800µm motion
- Combines higher dynamics & longer travel
- Millisecond responsiveness
- Ideal for autofocus, metrology, pathology
- New high performance controller
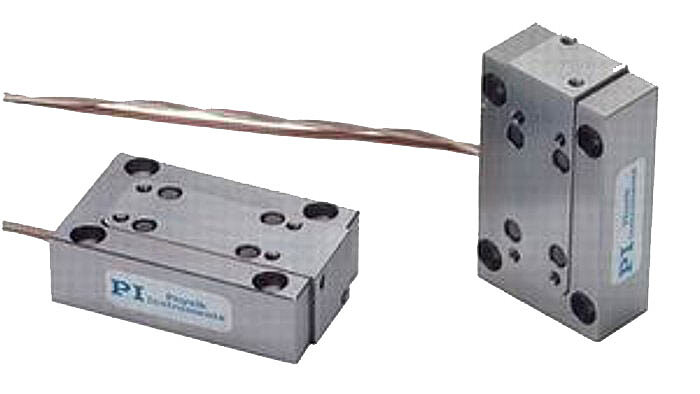
P-753 Piezo Flexure Stage/Actuator
Direct Drive, High Dynamics
- 38µm motion
- 0.05nm resolution
- Direct drive = Ultra-fast response
- Frictionless precision flexure guides
- Capacitive direct metrology
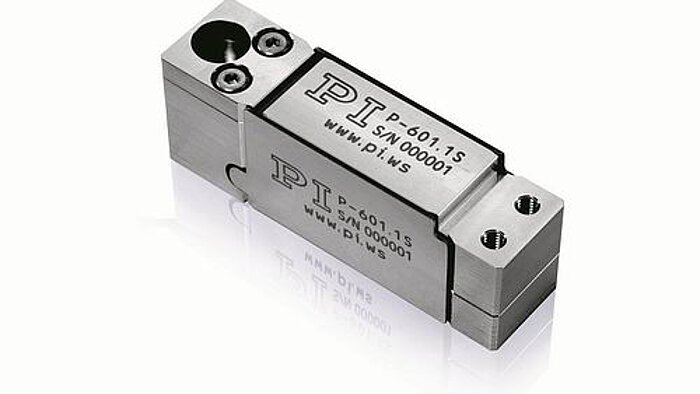
P-601 Piezo Flexure Z-Actuator
Motion-Amplified, 120 to 480µm
- 120 to 480µm motion
- <1 nanometer resolution
- High dynamics and stiffness
- Flexure guides = Straight motion
- PICMA® long-life piezo drives
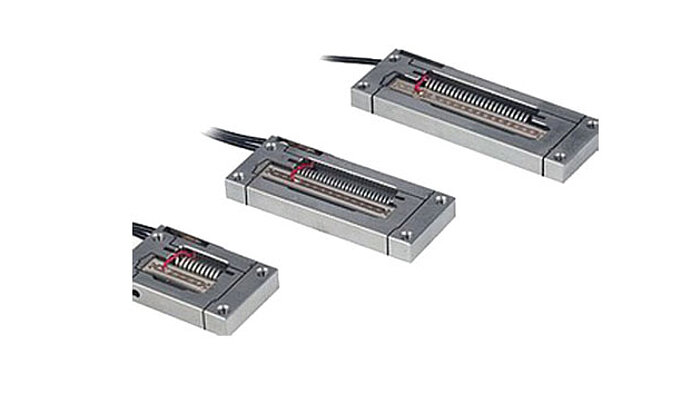
P-603 OEM Piezo Flexure Actuator
Motion-Amplified, 100-500µm
- 100, 300, 500µm motion
- Cost-effective OEM design
- Closed-loop option
- Frictionless, flexure guides
- Options: longer travel
With the use of flexures mechanisms, the motion of a piezo stack can be multiplied many times to achieve up to one millimeter travel (or more in extreme cases). The flexures can be used as guide and preload mechanism at the time. Flexure motion is based on the elastic deformation (flexing) of a solid material. Friction and stiction are entirely eliminated, and flexures exhibit high stiffness, load capacity, and resistance to shock and vibration. Flexures are maintenance free and not subject to wear. They are vacuum compatible, operate over a wide temperature range, and require neither lubricants nor compressed air for operation.
Piezo Stage Buyers Guide
Buying a piezo stage requires careful consideration of various factors to ensure that you choose the right product for your specific needs. Linear piezo stages are commonly used in applications such as microscopy, nanotechnology, laser machining, and more. Before we get into details, it is important to know that there are very different types of Piezo Stage designs. While all make use of the piezo effect, the major differences are the type of piezo motor that drives them. Highest precision is achieved with flexure guided, piezo-stack-driven stages. Read our tutorial on why not all piezo stages are created equal and our piezo nanopositioning stage FAQ blog to get the basics on the differences.. Here's a comprehensive buyer's guide to help you make an informed decision.
1. Performance Specifications
- Travel Range: Determine the required distance the stage needs to move. Linear piezo stages based on piezo-stacks and flexure guides offer the highest precision, especially for short travel ranges. Piezo motor stages offer longer travel ranges but are more comparable to magnetic linear drives in their precision.
- Resolution: Consider the smallest movement increment the stage can achieve. Piezo stages can provide ultra-high resolution, flexure guided, closed-loop stages get into the sub-nanometer range.
- Accuracy and Repeatability: Here, closed-loop operation is critical, with feedback sensors, controllers and advanced algorithms and guidance systems determining the limits. Short-travel stages benefit from capacitive feedback sensors or piezoresistive sensors, long-travel stages use high resolution linear encoders. Only flexure-guided stages are virtually friction free and can last billions of cycles without maintenance or wear.
2. Load Capacity
- Payload Capacity: Most ultra-high precision applications require small pay loads. When fast response and high dynamic performance is required, try to keep the payload as low as possible to achieve higher performance. Design mounting brackets from lightweight materials to improve performance.
3. Speed and Dynamics
- Speed and Settling Time: Direct-drive flexure stages achieve the fastest response times and highest frequencies. Faster settling times are preferable for applications requiring rapid positioning, fast focusing, scanning etc. Ultrasonic-motor stages can achieve 100’s of mm/sec over long travel ranges.
4. Feedback System
- Closed-Loop vs. Open-Loop: As mentioned above, closed-loop stages provide higher accuracy and repeatability. Read our blog article on how feedback sensor type influences the precision of a piezo stage. Typical position feedback mechanisms include piezoresistive sensors, strain gauge sensors, and capacitance sensors, the latter offering greater accuracy and linearity. Long travel stages use linear encoders or laser interferometer feedback. Open-loop stages lack this feedback and might be suitable for applications where extreme precision isn't necessary.
5. Piezo Motion Controller and Compatibility
- Digital vs Analog Servo: Digital servo circuits provide advantages in the choice of algorithms and auto-tuning capability. Analog servos can have advantages when it comes to low cost and size. Check the available control interfaces such as USB, RS-232, Ethernet, or analog control.
- Software Compatibility: Verify that the stage's control software is compatible with your operating system and programming environment.
6. Environmental Considerations
- Vacuum Compatibility: Piezo ceramics are intrinsically vacuum compatible and in the case of flexure guiding mechanisms, no lubricants are required, eliminating outgassing issues. Yet, other components can have an influence, so check with the manufacturer on the level of UHV compatibility.
- Temperature Stability: Temperature compensated designs can be used across a large range of temperatures with consistent performance. Discuss your requirements with the manufacturer upfront.
7. Cost and Budget, ROI
- Price: The lowest cost stage may become a burden if it is not performing according to specs and the manufacturer is not capable of providing the support to make it work in your specific application. A well designed piezo stage can last billions of cycles without any maintenance, providing greater value in the end.
8. Manufacturer and Support
- Reputation: Choose a reputable manufacturer known for producing high-quality piezo stages.
- Customer Support: Check if the manufacturer offers reliable customer support, warranty, and extended warranty options, as well as setup packages where an application engineer can save your project valuable time as well as making the product perform much higher in your application by tuning it perfectly to your requirements.
9. Future Scalability
- Expansion: Consider if you might need to expand your setup in the future. Choosing a controller that can be upgraded for multi-axis operation, or a modular stage that can be configured to provide XY or XYZ motion could turn out to further reduce your long-term cost.
Remember that the best linear piezo stage for you will depend on your specific application requirements. Prioritize the factors most critical to your work and conduct thorough research to find a stage that meets those needs. Working with a reputable manufacturer with a long track record is a good starting point. Reading user reviews, seeking recommendations from colleagues, and consulting with experts in the field can also provide valuable insights.
- High precision: Piezo flexure mechanisms are known for their high precision positioning capabilities. They can achieve sub-nanometer incremental motion, making them ideal for many cutting-edge applications in industry and research.
- Rapid response: Piezoelectric mechanisms, including flexure linear stages can respond to a control signal rapidly, in milliseconds or even microseconds. This makes them well-suited for dynamic applications, such as scanning, switching, or tracking where fast and accurate positioning is required.
- No friction: Piezo linear stages based on flexure mechanisms are frictionless, which means that they can provide smooth, continuous motion free of or backlash.
- High stiffness: Flexures, when designed properly provide a high stiffness, which means that they can resist deformation under load. This is a prerequisite for high guiding precision.
- Compact size: Flexure guiding mechanisms can be very compact. PI designs piezo linear stages where the flexure guides are cut into the monolithic stage using wire electro discharge machining techniques. With this design, stage and guiding system are one piece.
- Low power consumption: Piezo flexure linear stages require virtually no power to hold a position with nanometer precision, which keeps heat generation to a minimum and further increases position stability.
- Non-magnetic: Piezo flexure linear stages can be made from non-magnetic materials. The driving piezo element itself is of ceramic nature and creates no electromagnetic interference. This can be an advantage in many applications from electron beam lithography, electron microscopy, or in medical or scientific equipment.