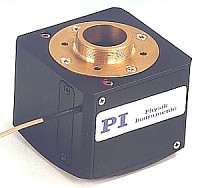
- Fast Piezo Drive for Focusing Applications with Nanometer Resolution
- Travel to 350 µm
- Precision Trajectory Control
- Fast Settling
P-722/P-723 PIFOC ® Focus Drives are fast and compact piezo mechanisms units which can be mounted on most microscopes. The units are screwed between the turret and the objective, providing a positioning and scanning range of up to 350 µm with nanometer resolution while extending the optical path by only 13 mm (infinity corrected microscope required; extension tubes are available to adjust path lengths of other objectives on the turret). Standard thread is W 0.8x1/36", alternate threads are ordered separately.
In open loop, the vertical position of the objective roughly corresponds to the drive voltage. The open loop models P-722.00 / P-723.00 are ideal for fast tracking applications where the position is controlled by data provided by an external sensor (e.g. optical displacement sensor, a CCD camera, etc.). The closed loop versions allow for absolute position control, high linearity and repeatability based on an integrated position feedback sensor.
Application examples:
Fast Focus Drives, scanning interferometry, surface structure analysis, disk drive testing, autofocus systems, confocal microscopy, bio-technology, semiconductor test equipment.
Working principle:
PIFOC focus drive positioners are equipped with low voltage piezoelectric drives (0 to 100 V) integrated into a sophisticated flexure guiding system. The force exerted by the piezo drive pushes a flexure parallelogram via an integrated motion amplifier. The wire EDM (Electric Discharge Machining) cut flexures are FEA (Finite Element Analysis) modeled for zero stiction/ friction, ultra-high resolution and exceptional guiding precision.
Optional threads for P-722.07/17 & P-723.07/17:
P-722.01 Thread M25x0.75 for P-722.07/17, P-723.07/17
P-722.02 Thread M26x0.75 for P-722.07/17, P-723.07/17
P-722.03 Thread M27x0.75 for P-722.07/17, P-723.07/17
P-722.04 Thread M28x0.75 for P-722.07/17, P-723.07/17
P-722.05 Thread M32x0.75 for P-722.07/17, P-723.07/17
P-722.06 Thread M26x1/36 for P-722.07/17, P-723.07/17
P-722.08 Thread M19x0.75 for P-722.07/17, P-723.07/17
Ordering Information:
- P-722.00 PIFOC Objective Positioner & Scanner, 200 µm, Thread W0.8 x1/36"
- P-722.07 PIFOC Objective Positioner & Scanner, 200 µm, Specify Thread (P-722.01 - .08)
- P-722.10 PIFOC Objective Positioner & Scanner, 200 µm, LVDT, W0.8x1/36"
- P-722.17 PIFOC Objective Positioner & Scanner, 200 µm, LVDT, Specify Thread (P-722.01 - .08)
- P-723.00 PIFOC Objective Positioner & Scanner, 350 µm, Thread W0.8x1/36"
- P-723.07 PIFOC Objective Positioner & Scanner, 350 µm, Specify Thread (P-722.01 - .08)
- P-723.10 PIFOC Objective Positioner & Scanner, 350 µm, LVDT, W0.8x1/36"
- P-723.17 PIFOC Objective Positioner & Scanner, 350 µm, LVDT, Specify Thread (P-722.01 - .08)
TECHNICAL DATA: | ||||||
Models | P-722.00 | P-722.10 | P-723.00 | P-723.10 | Units | Notes |
Max. objective diameter | 39 | 39 | 39 | 39 | mm | |
Open loop travel @ 0 to 100 V | 200 | 200 | 350 | 350 | µm ± 20 % | A2 |
Closed loop travel ³ | - | 200 | - | 350 | µm | A5 |
Integrated feedback sensor | - | LVDT | - | LVDT | B | |
Closed / open loop ** resolution£ | - / 2 | 10 / 2 | - / 3 | 10 / 3 | nm | C1 |
Closed loop linearity (typ.) | - | 0.1 | - | 0.1 | % | |
Full range repeatability (typ.) | ±40 | ±60 | nm | C3 | ||
Stiffness | 0.38 | 0.38 | 0.32 | 0.32 | N/µm ± 20 % | D1 |
Push/pull force capacity | 20 / 20 | 20 / 20 | 20 / 20 | 20 / 20 | N | D3 |
Tilt (Q X, Q Y) (typ.) | 3 | 3 | 5 | 5 | µrad | E1 |
Electrical capacitance | 7.8 | 7.8 | 11.1 | 11.1 | µF ± 20 % | F1 |
* Dynamic operating current | 4.8 | 4.8 | 3.9 | 3.9 | µA/(Hz x µm) | F2 |
Unloaded resonant frequency | 300 | 300 | 150 | 150 | Hz ± 20 % | G2 |
Resonant frequency @ 150 g load | 180 | 180 | 100 | 100 | Hz ± 20 % | G3 |
Operating temperature range | - 20 to 80 | - 20 to 80 | - 20 to 80 | - 20 to 80 | ° C | H2 |
Voltage connection | VL | VL | VL | VL | J1 | |
Sensor connection | - | L | - | L | J2 | |
Weight (with cables) | 400 | 410 | 410 | 420 | g ± 5 % | |
Body material | Al | Al | Al | Al | L | |
Recommended driver/controller | G, C, (A) | H, E | G, C, (A) | H, E | M |
* Dynamic Operating Current Coefficient in µA per Hertz and µm.
Example: Sinusoidal scan of 30 µm at 10 Hz requires approximately 1.4 mA drive current (P-722).
** Noise equivalent motion with E-503 amplifier.