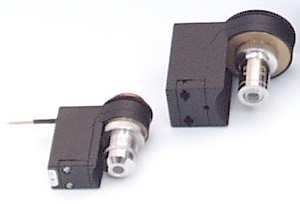
- Fast, Piezo-Based Focus Drive with Nanometer Precision
- Motion Range 100 microns
- Straightness of Travel ≤ 30 µrad
- Fast Settling Time
The P-720 and P-721 PIFOC® focus drives are piezo based mechanisms that combine high speed and precision to allow highly accurate motion for microscope lenses. The units are screwed between the turret and the objective, providing a positioning and scanning range of up to 100 µm with sub-nanometer resolution while extending the optical path by only 13 mm (infinity corrected microscope required; extension tubes are available to adjust path lengths of other objectives on the turret). Standard thread is W 0.8x1/36", alternate threads are ordered separately.
Open and closed-loop focus drives are available. Open loop models P-720 / P-721.00 are ideal for tracking applications where the position is controlled by data provided by an external sensor (e.g. optical displacement sensor, a CCD camera, etc.). The closed loop versions allow for absolute position control, high linearity and repeatability based on an integrated position feedback sensor.
Application examples:
Microscopy, fast focusing, scanning interferometry, surface structure analysis, disk drive testing, autofocus systems, confocal microscopy, bio- technology, semiconductor test equipment.
Working principle:
PIFOC focus drives are equipped with high performance piezo drives (0 to 100 V) integrated into a sophisticated flexure guiding system. The force exerted by the piezo drive pushes a flexure parallelogram via an integrated motion amplifier. The wire EDM (Electric Discharge Machining) cut flexures are FEA (Finite Element Analysis) modeled for zero stiction/ friction, ultra-high resolution and exceptional guiding precision.
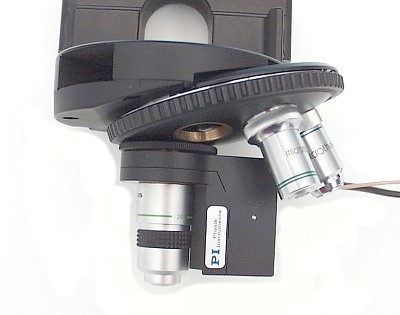
Optional threads for P-721.07 and P-721.17:
P-721.02 Thread M26 x 0.75 for P-721.07/17
P-721.03 Thread M27 x 0.75 for P-721.07/17
P-721.04 Thread M28 x 0.75 for P-721.07/17
P-721.05 Thread M32 x 0.75 for P-721.07/17
P-721.06 Thread M26 x 1/36 for P-721.07/17
P-721.08 Thread M19 x 0.75 for P-721.07/17
P-721.11 Thread M25 x 0.75 for P-721.07/17
Objective Extension Tubes:
P-721.90 Objective extension tube, 13 mm, thread W0.8x1/36
P-721.91 Objective extension tube, 13 mm, thread M25 x 0.75
P-721.92 Objective extension tube, 13 mm, thread M26 x 0.75
P-721.93 Objective extension tube, 13 mm, thread M27 x 0.75
P-721.94 Objective extension tube, 13 mm, thread M28 x 0.75
P-721.95 Objective extension tube, 13 mm, thread M32 x 0.75
P-721.96 Objective extension tube, 13 mm, thread M26 x 1/36
P-721.98 Objective extension tube, 13 mm, thread M19 x 0.75
Ordering Information:
P-720.00 PIFOC Objective Positioner & Scanner, 100 µm, W0.8 x1/36"
P-721.00 PIFOC Objective Positioner & Scanner, 100 µm, W0.8 x1/36"
P-721.07 PIFOC Objective Positioner & Scanner, 100 µm, Specify Thread (P-721.01 - .08)
P-721.10 PIFOC Objective Positioner & Scanner, 100 µm, LVDT Sensor, W0.8 x1/36",
P-721.17 PIFOC Objective Positioner & Scanner, 100 µm, LVDT Sensor, Specify Thread (P-721.01 - .08)
P-721.20 PIFOC Objective Positioner & Scanner, 100 µm, Capacitive Sensor, W0.8 x1/36"
TECHNICAL DATA: | ||||||
Models | P-720.00 | P-721.00 | P-721.10 | P-721.20 | Units | Notes |
Max. objective diameter | 25 | 39 | 39 | 39 | mm | |
Open loop travel @ 0 to 100 V | 100 | 90 | 90 | 90 | µm ± 20 % | A2 |
Closed loop travel* | - | - | 100 | 100 | µm | A5 |
Integrated feedback sensor | - | - | LVDT | Capacitive | B | |
Closed / open loop ** resolution £ | - / 1 | - / 1 | 10 / 1 | 1 / 1 | nm | C1 |
Closed loop linearity (typ.) | - | - | 0.1 | 0.03 | % | |
Full range repeatability (typ.) | - | - | ±20 | ±5 | nm | C3 |
Stiffness | 0.2 | 0.3 | 0.3 | 0.3 | N/µm ± 20 % | D1 |
Push/pull force capacity (in operating direction) | 100 / 20 | 100 / 20 | 100 / 20 | 100 / 20 | N | D3 |
Tilt (Q X, Q Y) (typ.) | 30 | 30 | 30 | 30 | µrad | E1 |
Lateral runout (Y) (typ.) | 100 | 100 | 100 | 100 | nm | E2 |
Electrical capacitance | 3.6 | 3.6 | 3.6 | 3.6 | µF ± 20 % | F1 |
* Dynamic operating current coefficient (DOCC) | 4.5 | 5 | 5 | 5 | µA/(Hz x µm) | F2 |
Unloaded resonant frequency | 400 | 620 | 620 | 620 | Hz ± 20 % | G2 |
Resonant frequency @ 120 g load | 180 | 280 | 280 | 280 | Hz ± 20 % | G3 |
Resonant frequency @ 200 g load | 150 | 220 | 220 | 220 | Hz ± 20 % | G3 |
Operating temperature range | - 20 to 80 | - 20 to 80 | - 20 to 80 | - 20 to 80 | ° C | H2 |
Voltage connection | VL | VL | VL | VL | J1 | |
Sensor connection | - | - | L | 2 x C | J2 | |
Weight (with cables) | 100 | 215 | 235 | 240 | g ± 5 % | |
Body material | Al | Al | Al | Al | L | |
Recommended driver/controller | G, C, (A) | G, C, (A) | H, E | H, F, L | M |
* Dynamic Operating Current Coefficient in µA per Hertz and µm. Example: Sinusoidal scan of 30 µm at 10 Hz requires approximately 1.4 mA drive current.
** Noise equivalent motion with E-503 amplifier.