For updated product information, see the latest specs and order info.
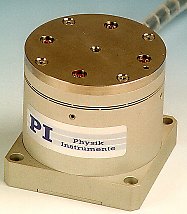
- 2 Axis, ±1mrad θX and θY Tilt Range
- For Laser Mirrors to 100 mm Ø
- Sub-µrad Resolution
- Closed Loop Versions
- Differential Drive Design for Excellent Temperature Stability
S-340 Two Axis High Speed Laser Beam Steering Mirror Platforms are based on a flexure-guided, high precision Piezo Tip/Tilt mechanism. These very fast and compact tilt stages provide extremely dynamic and precise angular movements of the top platform in two orthogonal axes. The angular tilt range is ±1mrad (each axis) with sub-µrad resolution. Closed loop feedback versions provide the highest accuracy, repeatability and precision. S-340 laser steering mirror systems are designed for mirrors up to 100 mm diameter and have outstanding angular stability over a wide temperature range.
To match the CTEs of various mirror materials the following platforms are available (see ordering information).
Application Examples
Free space optical laser communication, image dithering, image stabilization, image resolution enhancement, laser beam stabilization, precision optical dithering, adaptive optics systems, laser beam steering & scanning, correction of polygon scanner errors
Steering Mirror Working Principle
S-340 Tilt stage platforms are equipped with two pairs of ultra-reliable multilayer piezoelectric linear drives operating in push/pull mode for higher stability and performance. The aluminum case is equipped with an integrated, FEA (Finite Element Analysis) modeled circular flexure featuring zero stiction/friction and exceptional guiding precision.
In open loop operation, the laser mirror platform angle roughly corresponds to the drive voltage. The open loop models are ideal for applications where the position is controlled by an external loop based on data provided by a sensor (e.g. quad cell, CCD chip, ...).
The closed loop laser mirror versions are equipped with two pairs (one per axis) of LVDT (Linear Variable Differential Transformer) sensors operated in a bridge circuit for ultra-high resolution and angular stability. They provide sub-µrad resolution and repeatability (with PI control electronics).
A) Piezo Driver Electronics for High Dynamic, High Speed, High Precision Applications
E-500 Chassis with 2 x standard and 1 x specially configured E-505.00 Amplifier Modules, specially configured E-509.L3 Position Servo Controller Module (required for closed loop operation, section for details).
B) Piezo Driver Electronics for Static and Medium Dynamic Applications
E-500 Chassis with specially configured E-503.00 Amplifier Module, specially configured E-509.L3 Position Servo Controller Module.
ORDERING INFORMATION:
S-340.A0 2-Axis Piezo Tilt Platform, ±1 mrad, Aluminum Top Plate
S-340.i0 2-Axis Piezo Tilt Platform, ±1 mrad, Invar Top Plate
S-340.S0 2-Axis Piezo Tilt Platform, ±1 mrad, Steel Top Plate
S-340.T0 2-Axis Piezo Tilt Platform, ±1 mrad, Titanium Top Plate
S-340.AL 2-Axis Piezo Tilt Platform, ±1 mrad, Aluminum Top Plate, LVDT Sensor
S-340.iL 2-Axis Piezo Tilt Platform, ±1 mrad, Invar Top Plate, LVDT Sensor
S-340.SL 2-Axis Piezo Tilt Platform, ±1 mrad, Steel Top Plate, LVDT Sensor
S-340.TL 2-Axis Piezo Tilt Platform, ±1 mrad, Titanium Top Plate, LVDT Sensor
Platform | Recommended Mirror | Models |
Aluminum | Aluminum | S-340.Ax |
Invar | Zerodur Glass | S-340.ix |
Titanium | BK7 Glass | S-340.Tx |
Steel | S-340.Sx |
TECHNICAL DATA: | ||||
Models | S-340.A0 | S-340.AL | Units | Notes |
Active axes | θX,θY | θX,θY | ||
Open loop tilt angle @ 0 to 100 V | ±1 | ±1 | mrad ± 20 % | A2 |
Closed loop tilt angle ³ | - | ±1 | mrad | A3 |
Integrated feedback sensor | - | 4 x LVDT | B | |
Closed / open loop ***resolution ≤ | - / 0.1 | 0.5 / 0.1 | µrad | C1 |
Closed loop linearity (typ.) | - | ±0.1 | % | |
Full range repeatability (typ.) | - | ±1 | µrad | C3 |
Electrical capacitance | 7.2 / axis | 7.2 / axis | µF ± 20 % | F1 |
* Dynamic operating current coefficient (DOCC) | 0.45 / axis | 0.45 / axis | µA/(Hz x µrad) | F2 |
** Unloaded resonant frequency (f0) | 1.4 | 1.4 | kHz ± 20 % | G2 |
** Resonant frequency w/ Ø 50 x 15 mm glass mirror | 0.9 | 0.9 | kHz ± 20 % | G3 |
** Resonant frequency w/ Ø 75 x 22 mm glass mirror | 0.4 | 0.4 | kHz ± 20 % | G3 |
Distance pivot point to platform surface (T) | 7.5 | 7.5 | mm | |
** Platform moment of inertia | 18000 | 18000 | gmm² | |
Operating temperature range | - 20 to 80 | - 20 to 80 | ° C | H2 |
Voltage connection | 3 x VL | 3 x VL | J1 | |
Sensor connection | - | 2 x L | J2 | |
Weight (w/o cables) | 335 | 335 | g ± 5 % | |
Material (case / platform) | Al / depends on version | Al / depends on version | L |
* Dynamic Operating Current Coefficient in µA per Hertz and mrad. Example: Sinusoidal scan of 100 mrad at 10 Hz requires approximately 0.45 mA drive current.
** Value for aluminum top plate. Lower resonant frequency for other platforms due to higher moment of inertia: Titanium: +60%; Invar: +200%; steel: +190%.
*** Noise equivalent motion with E-503 amplifier.
For updated product information, see the latest specs and order info.
This is a legacy product that may have limited availability or may have been replaced. Ask a PI engineer for an equivalent new model.