Performance Measurements on a Fast Tracking Autofocus Scanning Stage
Nanometer resolution, minimal tracking error, and high frequency made possible by a voice-coil direct-drive stage with advanced motion control algorithms.
In Glasgow City, Scotland, allegorical figures of speed and science flank the main entrance to the North British Locomotive Company. Speed is gazing toward the allegory of science caught in a dramatic pose of extreme dynamism with the inertia of flowing robes behind, astride a winged chariot. These allegorical figures were created shortly after the Wright Brothers were actively pioneering the frontiers of powered flight. At this intersection of science, speed, and flight, we find new frontiers in genetic sequencing, nanofabrication, and digital pathology taking place in the modern day.
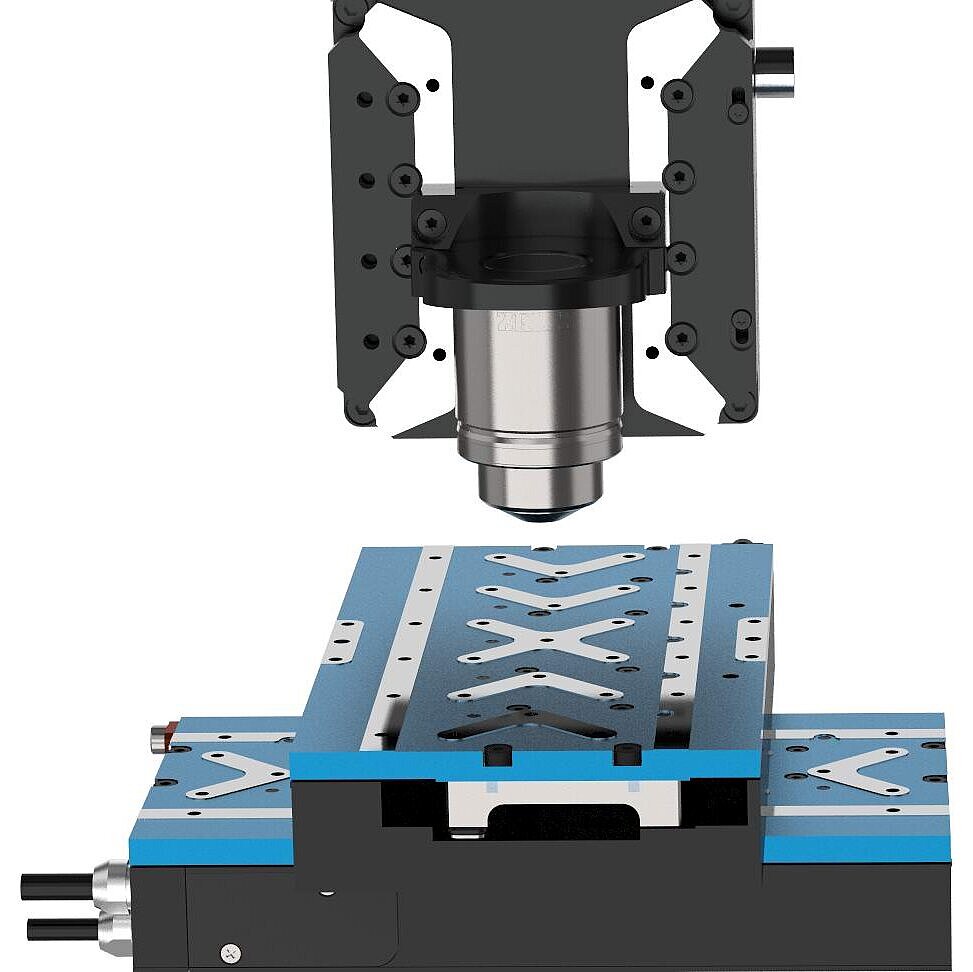
At the borders of new scientific frontiers, highly specialized motion control systems, optics, and high numeric aperture microscope objectives provide a medium to interface with the mesoscopic world. These narrow focal depth objectives impose constraints on imaging and fabrication that become inextricably linked to the materials and methods they interface with. In the macroscopic world of materials, tolerances often extend beyond what a static objective process can accommodate and the need for fast autofocus arises.
Autofocus systems, much like the allegorical figures in Glasgow, are driven by motion systems that rely on science to achieve speed at correct fly height. The science of autofocus is superficially simple, but when done optimally is built on deceptively complex motion science that extracts the greatest value from optimally selected positioning, motion control, and sensing hardware. PI has a variety of technological solutions deployed globally helping promote new development and production. One common solution uses the PI V-308 positioning stage and a high-performance motion controller.
The V-308 is a high-precision, compact direct-drive stage originally designed and developed for fast tracking autofocus applications with large objectives. With in-position stability reaching the nanometer and sub-nanometer scale and servo bandwidth achieving up to 200 Hz, the V-308 has become a go-to solution for fast focus applications. Providing a 1kg load capacity and an innovative integrated adjustable dual magnetic counterbalance, the V-308 can be used optimally in any orientation and easily integrated. Our tests were run with an A-81x series motion controller equipped with an ACS SpiiPlusEC motion controller module with 5 kHz MPU and UDMnt drive. ACS motion controllers provide exceptional motion performance and are available with advanced control algorithms that reduce heat while increasing motion performance in high duty-cycle applications.
Setup and Performance Test Results
We tested different move amplitudes (2.5µm to 3mm) and frequencies up to 200Hz. The stage can run up to 200Hz but for the pathing algorithm to provide optimum results, the controller sampling frequency suggests 50Hz as the practical speed limit.
We will be running additional tests with different loads in the near future. The current results show that the V-308 stage (operated with an ACS controller) is capable of rapid profile/scanning motion with almost imperceptible tracking error. In a different test, the stage also proved capable of moves with excellent velocity constancy, which is critical for two photon polymerization.
How Autofocus Works
There are several ways to design an autofocus system, the following methods are the most common.
Contrast Detection: Contrast detection directly looks at the sharpness of an image by measuring the contrast between neighboring pixels. When an image is in focus, the contrast between adjacent pixels is at its highest. Therefore, by continually adjusting the lens and monitoring the change in contrast, the system can determine the optimal focus.
Phase Detection: This method works on the principle of parallax, where it compares two or more images from different angles to estimate the distance to the subject. Here, the incoming light is analyzed through the lens. The phase detection method conducts a comparison of the light originating from two apertures positioned at opposite ends of the lens. When the image is accurately focused, the intensity profiles from the two light beams overlap. However, if the image is out of focus, the system is capable of precisely determining the extent to which the focus requires adjustment, without the oscillations typical in contrast-detection autofocus.
Laser Autofocus: Laser autofocus systems operate by emitting a laser beam towards the subject and measuring the time it takes for the beam to bounce back to a sensor. This is known as time-of-flight measurement. Based on the speed of light, which is constant, the exact distance can be calculated and fed into the motion controller to set the correct position. Laser autofocus is very fast and accurate and works well even in low light conditions. It is particularly effective for close-up subjects.
Blog Categories
- Aero-Space
- Air Bearing Stages, Components, Systems
- Astronomy
- Automation, Nano-Automation
- Beamline Instrumentation
- Bio-Medical
- Hexapods
- Imaging & Microscopy
- Laser Machining, Processing
- Linear Actuators
- Linear Motor, Positioning System
- Metrology
- Microscopy
- Motorized Precision Positioners
- Multi-Axis Motion
- Nanopositioning
- Photonics
- Piezo Actuators, Motors
- Piezo Mechanics
- Piezo Transducers / Sensors
- Precision Machining
- Semicon
- Software Tools
- UHV Positioning Stage
- Voice Coil Linear Actuator
- X-Ray Spectroscopy