Rotary Stages: Direct Drive and Worm Gear, Choice of Motors
Different Direct Drive Principles with 3-Phase and Piezo-Electric Motors
High Performance Rotation Stages for Industry and Research
The PI Group provides a variety of direct drive rotation stages and worm-gear driven goniometers and rotary stages, designed for a large spectrum of automation and research applications. High speed, high performance rotation stages are equipped with 3-phase electromagnetic motors and mechanical bearings or air bearings – for frictionless and maintenance free operation with the highest accuracy and geometric precision. Our extensive knowledge in the design and manufacture of highly precise rotation stages and multi-axis positioning systems has helped many customers solve precision motion control problems in variety of applications, including optical metrology, precision automation, beamline instrumentation, fiber-optical alignment, semiconductor inspection, bio-medical instrumentation, and X-ray crystallography.
The advantage of working with PI is the access to a large variety of different drive and guiding technologies.
Highest performance is guaranteed through the complete control of the design and machining process, the selection of components and assembly. Our air-bearing rotary stage selection is the most accurate in the industry with minimized eccentricity and wobble, while providing the highest repeatability and accuracy. A variety of motors and drive principles are available from stepper-motor driven worm gear designs to direct drive closed-loop torque motors. Low profile piezo motor stages provide self-locking capabilities with zero jitter, drift and no holding current at rest.
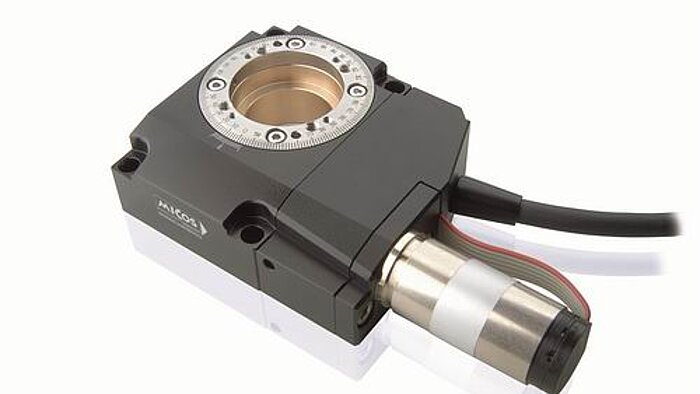
RS-40 Small Rotation Stage
Worm Gear, Servo & Stepper
- 20mm aperture, 34mm turn table
- 87µrad min. inc. motion
- 7°/sec max. velocity
- 2kg load
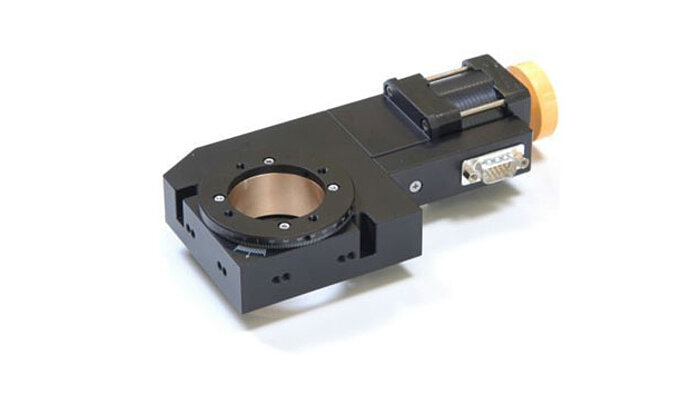
DT-80 Small Rotation Stage
Worm Gear, Servo & Stepper
- 40mm aperture, 64mm turn table
- 70µrad min. inc. motion
- 40°/sec max. velocity
- 2kg load
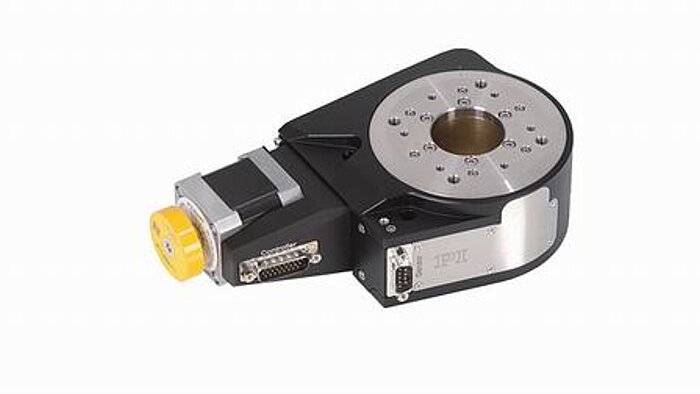
L-611 Precision Rotary Stage
Worm Gear, Servo / Stepper
- 35mm aperture, 80mm turn table
- 0.7µrad min. inc. motion
- 50-200°/sec max. velocity
- 10kg load
- Direct encoder option
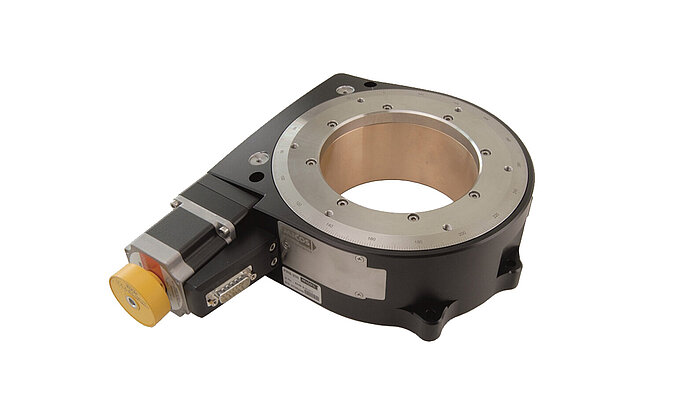
PRS-200 Precision Rotary Stage
Worm Gear, Servo / Stepper
- 120mm aperture, 200mm turn table
- 0.5 – 8.7µrad min. inc. motion
- 35-75°/sec max. velocity
- 50kg load
- Direct encoder option
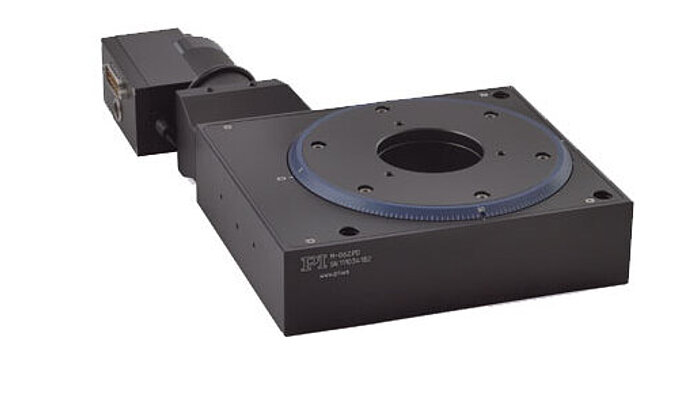
M-060/1/2 Precision Rotary Stage
Worm Gear, Servo / Stepper
- 20/35/45mm aperture, 60/100/120mm turn table
- 5 – 32µrad min. inc. motion
- 7.5-90°/sec max. velocity
- 50kg load
- Rotary encoder
Direct Drive Rotation Stages with High Performance Torque Motors for High Speed, Direct Metrology Closed-Loop Encoder, Mechanical Bearings
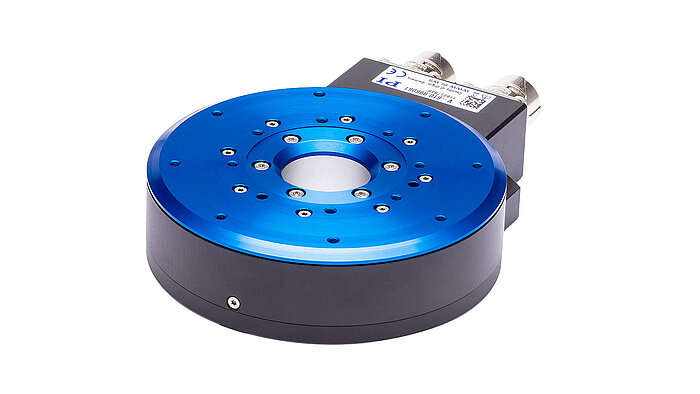
V-610 High Precision Rotation Stage
Direct Drive, Direct Encoder
- 25mm aperture, 100mm turn table
- 27µrad min. inc. motion
- 540°/sec max. velocity
- 2kg load
- Torque motor, sine/cosine encoder
- Optional brake
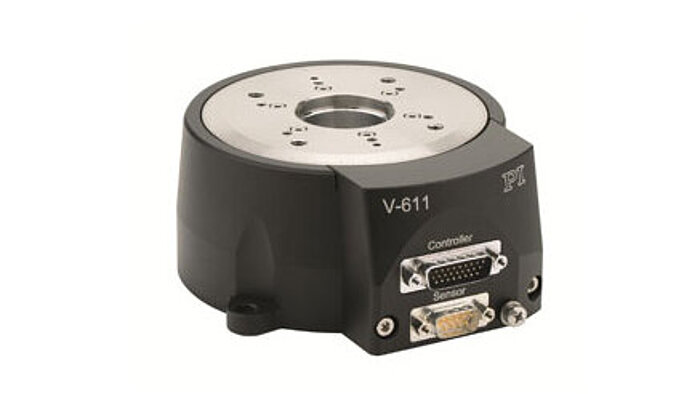
V-611 High Precision Rotation Stage
Direct Drive, Absolute Encoder Option
- 35mm aperture, 100mm turn table
- 1µrad min. inc. motion
- 2880°/sec max. velocity
- 10kg load
- Torque motor
- Sine/cosine or absolute encoder
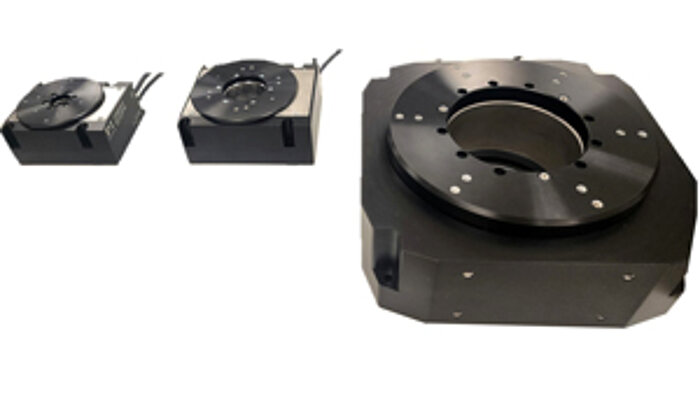
V-62x Ultra-High Precision Rotation Stages
Direct Drive, Absolute Encoder Option
- 85/110mm turn table
- 0.0015µrad max resolution
- 7200°/sec max. velocity
- 15kg load
- Torque motor
- Sine/cosine or absolute encoder
Direct Drive Rotation Stages, Ultra-High Precision Air Bearings. High Performance Direct Drive Torque Motor, Direct Metrology Closed-Loop Encoder
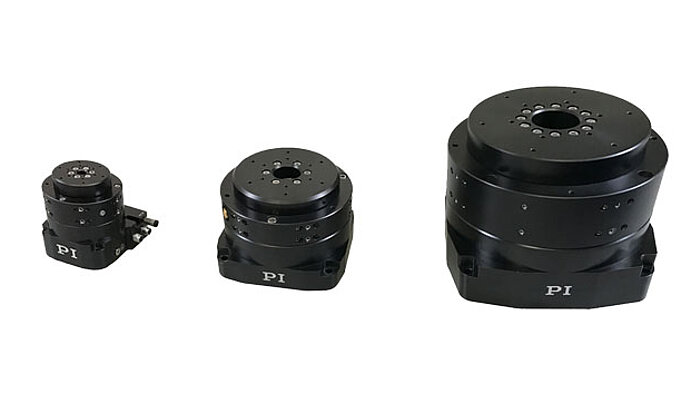
A-621 - A-627 Air Bearing Rotary Stages
Direct Drive, High Load
- 2/4/6/8/12” table diameter
- 13 to 420kg load
- 0.008µrad max. resolution
- 40 to 100nm flatness
- 500 to 2500 RPM max.
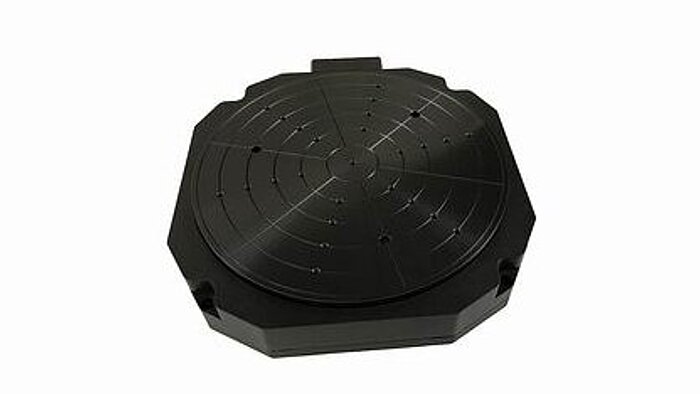
A-634 – A-638 Air Bearing Rotary Stages
Low Profile, Large Diameter
- 6/8/14” table diameter
- 20/32/60/120kg load capacity
- 0.03µrad max. resolution
- <100nm eccentricity & flatness
- 500 RPM max.
- Self-locking option at rest
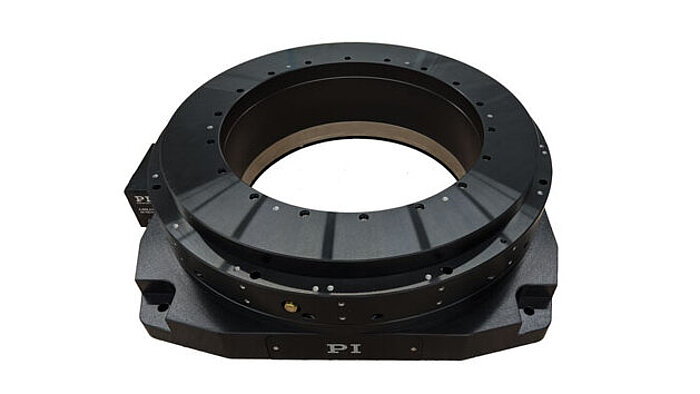
A-688 Air Bearing Rotary Stage
Large Clear Aperture
- ⌀260mm clear aperture
- 77kg load capacity
- 0.0015µrad max. resolution
- 500 RPM max.
- Flatness/Eccentricity <175/300nm
- Wobble: < 1µrad
- Direct drive
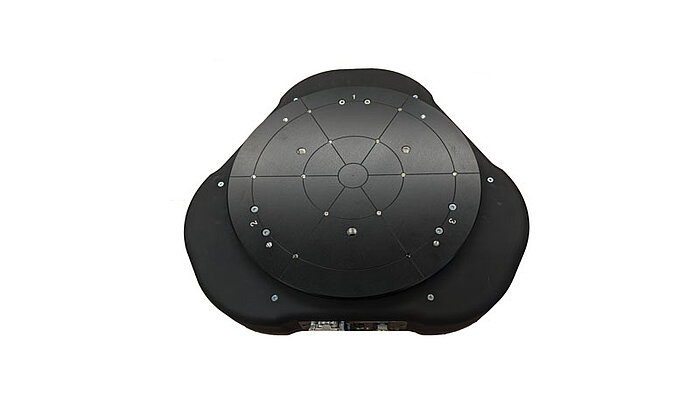
A-523 Z-Tip-Tilt Air Bearing Stage
Low Profile
- ⌀250mm table
- 8 kg load capacity
- 5mm Z-stroke, to 2° tip/tilt
- 10nm/0.06µrad incremental motion
- 1nm sensor resolution
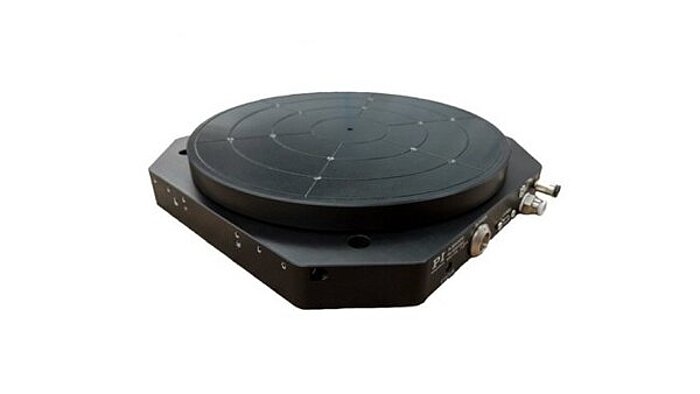
A-361 X-Y-θ Air Bearing Alignment Stage
Voice Coil Driven, Low Profile
- 5mm x 5mm x 2° Travel
- 40mm height, ø200mm
- Air Bearings & Voice Coils
- Parallel Kinematics
- Lock-down Capable
- 6-DOF Option
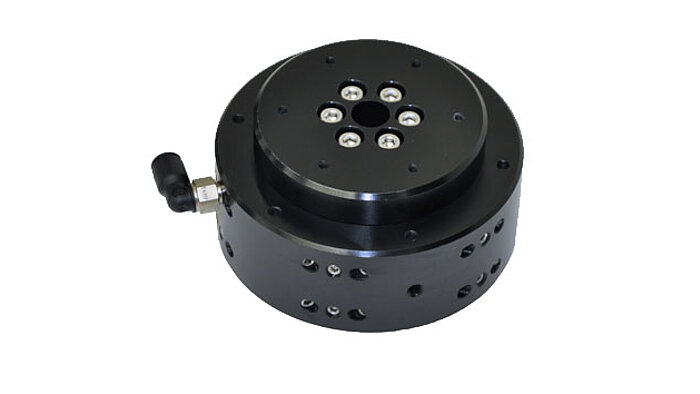
A-601 – A-607 Rotary Air Bearings
Non Motorized, Encoder Options
- Ideal for optics testing
- 2/3/4/6/8/12” table diameter
- 13 to 420kg axial load
- 5 to 270kg radial load
- 75 to 300nm eccentricity
- Optional high resolution encoder
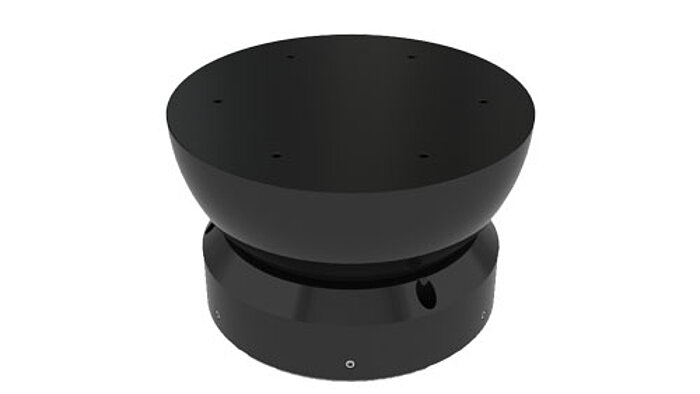
A-651 - A-657 Spherical Air Bearings
3 Degrees of Freedom
- Ideal for zero gravity simulation
- 2/3/4/6/8/10/12” sphere diameter
- 15 to 635kg load
- ±45 degrees rotation range
Direct-Drive Rotation Stages, Ultrasonic Motor, Low Profile, Self Locking Drive, Wide Dynamic Range, Direct Metrology Encoder
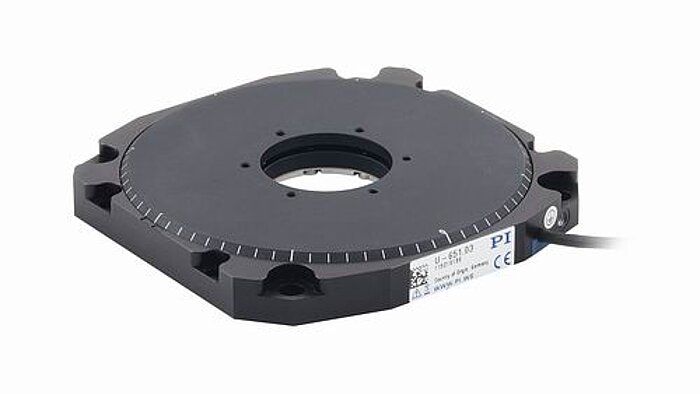
U-651 Low Profile Ultrasonic Motor Stage
Direct Drive, Direct Encoder
- 36mm aperture, 110mm turn table, 14mm height
- 12-27µrad min. inc. motion
- 540°/sec max. velocity
- 2kg load
- Ultrasonic motor, self locking
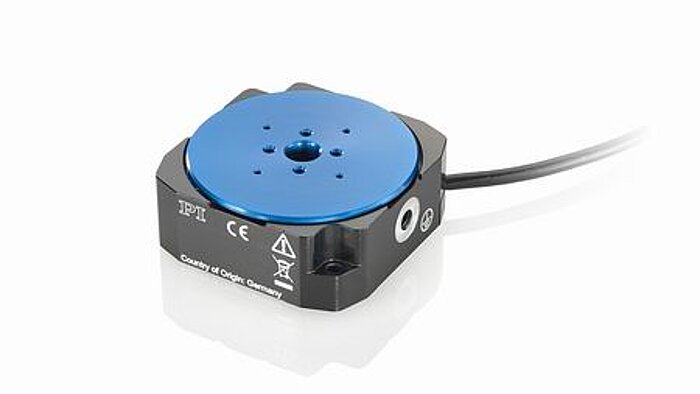
U-628 Miniature Ultrasonic Motor Stage
Direct Drive, Direct Encoder
- 7mm aperture, 50mm turn table, 19mm height
- 51µrad min. inc. motion
- 720°/sec max. velocity
- 0.5kg load
- Ultrasonic motor, self locking
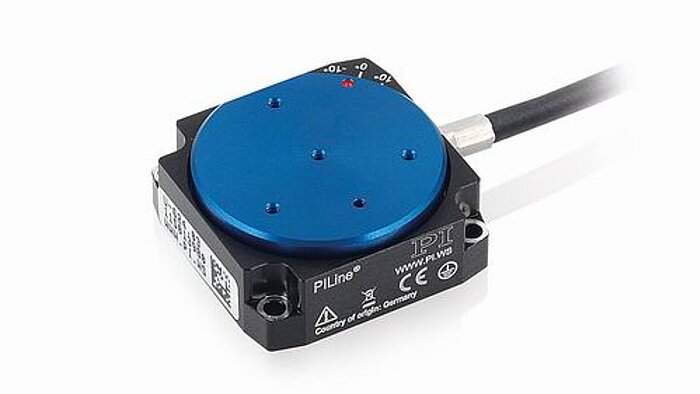
U-624 Miniature Ultrasonic Motor Stage
Direct Drive, Direct Encoder
- 28.5mm turn Table, 12mm height
- 105µrad min. inc. motion
- 720°/sec max. velocity
- 0.1kg load
- Ultrasonic motor, self locking
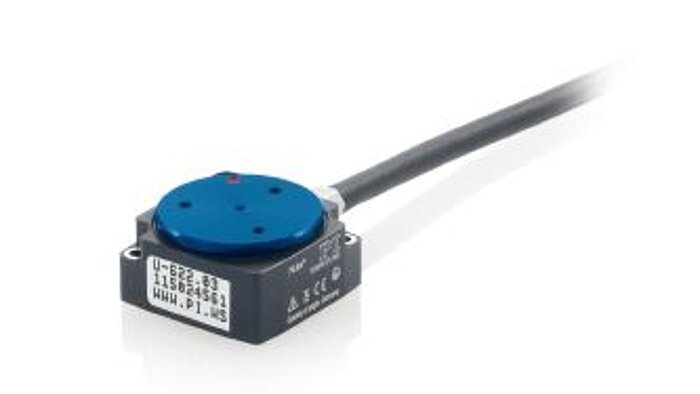
U-622 Miniature Ultrasonic Motor Stage
Direct Drive, Direct Encoder
- 18.5mm turn table, 10mm height
- 525µrad min. inc. motion
- 720°/sec max. velocity
- 0.03kg load
- Ultrasonic motor, self locking
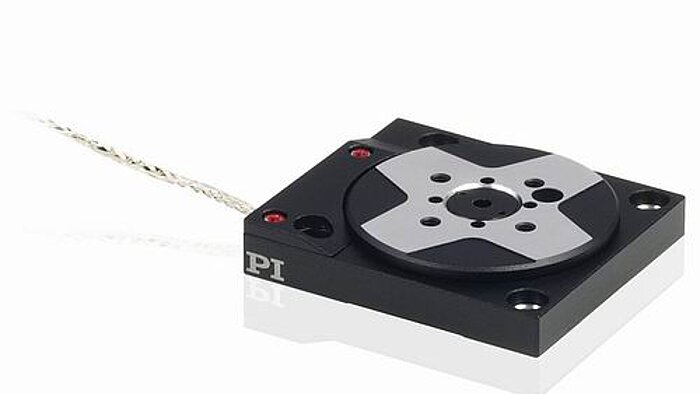
Q-632 Q-Motion® Miniature Rotation Stage
Inertia Motor, Direct Encoder
- 30mm turn table, 10mm height
- 3µrad min. inc. motion
- 45°/sec max. velocity
- 0.1kg load
- Piezo inertia motor, self locking
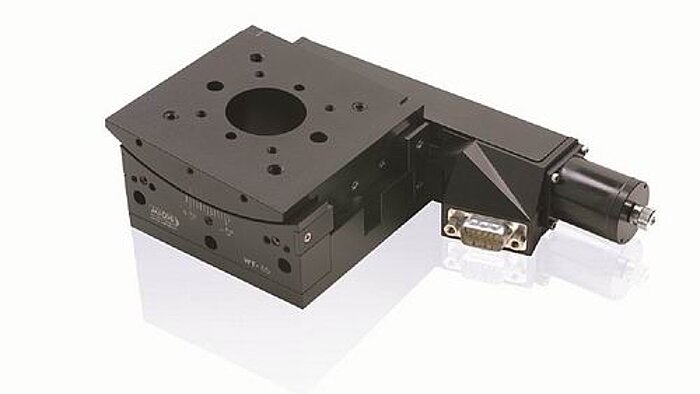
WT-85 Motorized Precision Goniometer
Aperture, Servo / Stepper
- 10° rotation range
- 2 - 17.5µrad min. inc. motion
- 7 - 15°/sec max. velocity
- 2kg load
- 30mm aperture
- Direct encoder option
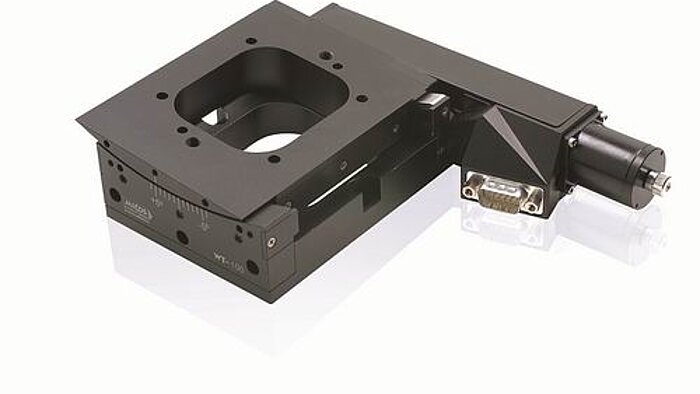
WT-100 Motorized Precision Goniometer
Aperture, Servo / Stepper
- 10° rotation range
- 8.7 - 17µrad min. inc. motion
- 7-15°/sec max. velocity
- 2kg load
- 50mm aperture
- Direct encoder option
What is a Rotation Stage?
A precision rotation stage, also referred to as rotary stage, is designed to limit movement to a solitary rotary degree of freedom, or rotation axis, and meticulously regulate the circular motion along this axis. PI provides a variety of high-precision rotation stages and tables with a range of motor and drive options, from direct drive air bearings to compact stepper motor driven worm-gear stages. Talk to our engineers to find the best match to your application.
Rotary Stages Buyers Guide
When you're in the market for a rotary stage, there are several key factors to consider to ensure that you select the right equipment for your needs. Here's a simple guide to help you make an informed decision:
- Load Capacity: Consider the weight, size, and inertia of the object that the rotary stage will need to support. A stage with a high load capacity may be necessary for heavier or larger items.
- Motor Type: Stepper motors are simple in their control, but limited in velocity and without feedback may lack the required accuracy. Closed-loop servo motors provide higher speed and better repeatability due to the encoder feedback. Direct-drive torque motors provide the highest performance and speed, but won’t hold a position without power. Piezo motors are very compact, provide high resolution, and hold a position even when powered down. On the other hand, they don’t handle high loads.
- Rotation Range: Depending on your application, you may need a rotary stage that can turn 360 degrees or possibly even more. Check the rotation range of the stage to ensure it fits your needs.
- Resolution and Accuracy: The resolution of a rotary stage determines how precisely it can be moved or positioned. This is particularly crucial for applications that require very precise positioning, such as optics or photonics alignment. Here, direct drive stages with direct encoders are superior to worm-gear-driven stages. Air bearings outperform mechanical bearings.
- Speed: The speed at which the rotary stage can rotate might be important, depending on your application. If you're using the stage in a production environment, for instance, a faster rotation speed could increase throughput. Again, direct-drive motors provide the highest speed.
- Drive Mechanism: Rotary stages can use different types of drive mechanisms, such as worm gears, direct drive motors, or belt drives. The choice of drive mechanism can affect the stage's speed, accuracy, and lifespan. Worm-gear driven stages can provide high torque from small motors, but relatively lower speed. Three-phase direct-drive torque motors provide fast acceleration, high velocity, and are friction and wear free. Belt drives can also provide high velocity, but lack the precision of a direct drive or good worm gear motor.
- Environment Suitability: Consider the environment in which the stage will be used. For instance, if it will be used in a cleanroom, vacuum, or under harsh conditions, you’ll need a stage designed to withstand those conditions. Stepper motors are often used for high vacuum environments. Lubrication and friction-free air bearing stages are ideal for clean room compatibility.
- Support and Warranty: Check the level of technical support provided by the manufacturer, as well as the warranty terms. Always discuss your requirements with the manufacturer or supplier to ensure you choose the most suitable stage.
Applications for Motorized Rotation Stages (Rotary Tables):
Motorized rotation stages are used in various applications where accurate and controlled rotation is required. Several use cases are listed below:
- Optics and Photonics: Precision motorized rotation stages are widely used in the field of optics and photonics for applications including laser beam control, alignment, waveplate rotation, polarizer rotation, and optical component positioning. They enable precise angular control for achieving desired optical configurations and alignments. With some of PI’s rotary stages, especially air bearing stages, angular resolution to 0.008µrad is available
- Microscopy: In microscopy applications, high precision motorized rotation stages are utilized for highly accurate sample positioning, angular scanning, and multi-axis imaging. The precise rotation of microscope stages enables researchers to capture images from different angles and orientations.
- Metrology and Precision Measurement: Motorized high precision rotation stages play a crucial role in surveying instruments, metrology and precision measurement applications. They are used for calibrating instruments, aligning optical systems, and conducting accurate angular measurements. These stages ensure precise angular positioning for achieving reliable and repeatable measurement results.
- Semiconductor Manufacturing: In semiconductor and MicroLED manufacturing processes, high precision motorized rotary stages are employed for wafer alignment, inspection, and testing. They enable precise rotation of wafers during lithography, etching, and other fabrication steps, ensuring precise alignment and accuracy in microchip production.
- Robotics and Automation: High precision motorized rotary stages find applications in robotics and automation systems where precise rotary movements are required. They are used in robotic arms, automated assembly lines, and robotic manipulators to provide accurate positioning and rotation for various tasks. PI provides custom 6-axis robotic hexapod stages with an additional 360 degree rotation axis.
- Research and Development: Motorized high precision rotary stages are essential in research and development environments, where highly accurate angular motion is needed for experimental setups, material characterization, and testing. They provide researchers with the ability to precisely manipulate samples, devices, or instruments in their studies.
In summary, the large selection of high precision motorized rotation stages listed on this overview page can be utilized in many high fields that demand accurate and controlled rotation, enabling precise angular positioning, alignment, measurement, and manipulation of various objects and components.