Linear Actuators – High Precision Motorized Actuators
Direct Drive, Voice Coil, Ball Screw, Linear Motor and Piezo Motor Actuators for Precision Motion and Positioning
A precision linear actuator is a positioning device that provides linear motion in one axis (1 degree of freedom). PI designs and manufactures a variety of precision actuators (pushers) for high precision motion control, positioning and automation applications.
Actuator types include economical stepper-motor linear actuators, high-speed linear actuators based on frictionless, brushless linear motors, for performance automation applications and nanometer-precise piezo-motor linear actuators.
While there are many different types of precision motorized linear actuators, piezoelectric actuators are the first choice when accuracy, speed, responsiveness, and resolution are essential. Long travel, motorized, rodless actuators – often called linear stages – provide precision guidance and facilitate the mounting of objects.
See our latest direct-drive linear modules for industrial automation.
Precision Lead Screw Captive Linear Actuators, Closed-Loop Servo and Stepper Motor-Driven
<0.1µm Resolution to 50mm Travel, ~1mm/sec
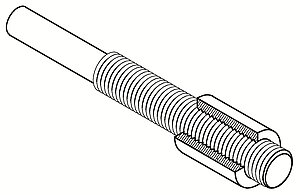
These classical captive motorized linear actuators convert rotary motion into linear motion by coupling a rotary motor to a lead screw or ball screw. They are available with closed-loop servo motors and, for lower cost applications with stepper motors.
Lead-screw actuators provide high forces and can hold high loads with self-locking capabilities, while ball screw actuators are used for higher speed linear motion applications with longer service life. Position feedback is available with linear encoders and motor shaft mounted rotary encoders. Both types of actuators are based on a combination of an electromagnetic rotary motor with a mechanical screw.
To reduce power consumption and size, smaller rotary motors are often equipped with gear heads to provide higher torque and resolution, however at the cost of speed.
Motorized linear actuators with built-in anti-rotation (non rotating tip) are easier to integrate and when used as pushers, do not generate torque or wear at the contact surface. An economical high precision stepper motor actuator controller is available as the C-663 Mercury Step.
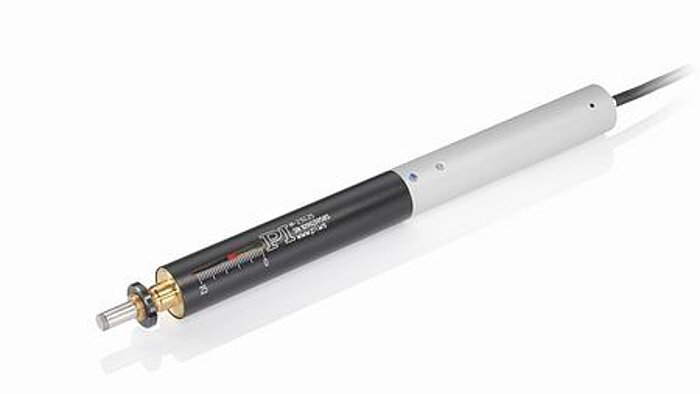
M-230 High Precision Actuator
Servo & Stepper Motors
- 10 and 25mm travel
- 0.05µm min. incremental motion
- 4nm sensor resolution
- 1.2 mm/sec max. velocity
- 70N push/pull force
- Nonrotating tip
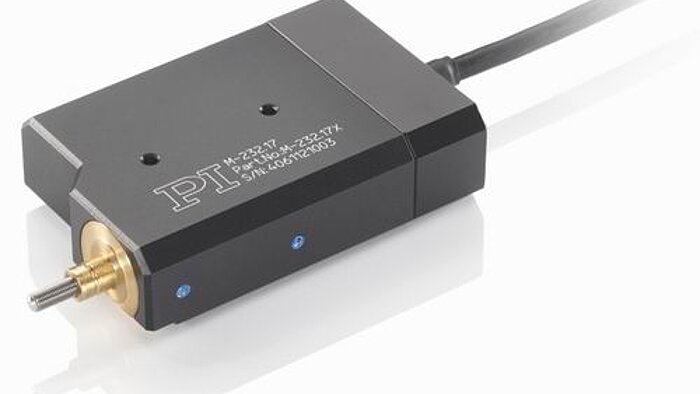
M-232 Servo Motor Actuator
Compact, Servo & Stepper
- 17mm travel
- 0.1µm min. incremental motion
- 7nm sensor resolution
- 1.5 mm/sec max. velocity
- 40N push/pull force
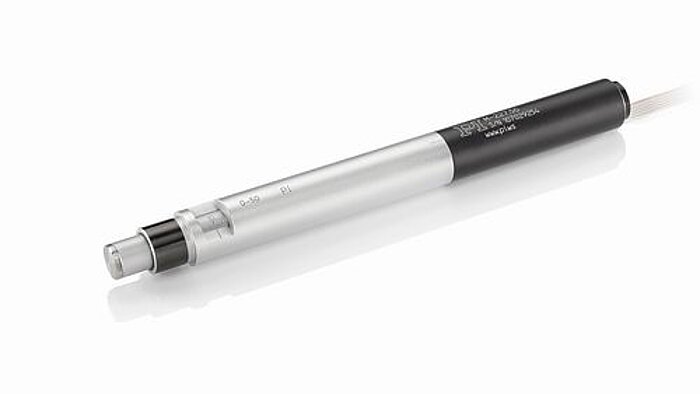
M-227 High Precision Actuator
Servo & Stepper Motors
- 10, 25, 50mm travel
- 0.05µm min. incremental motion
- 4nm sensor resolution
- 0.75mm/sec max. velocity
- 40N push/pull force
- Nonrotating tip
- Requires external limit switches
Low Cost Stepper Motor Captive Actuators, Lead Screw Drive
To 25mm Travel, 1µm Resolution, to 5mm/sec
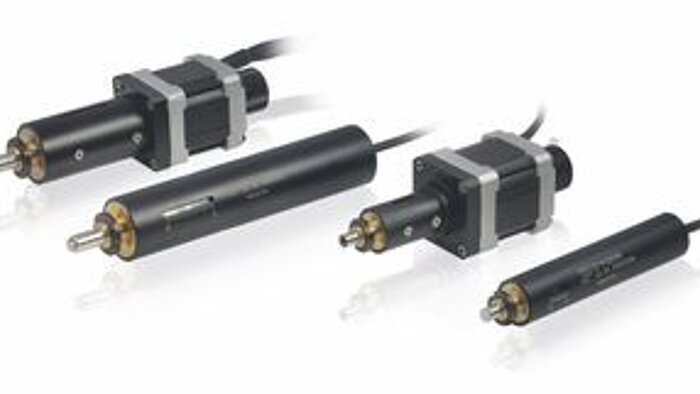
M-228/9 Low Cost Linear Actuators
Gear & Direct Drive, Stepper
- 10 and 25mm travel
- 1µm min. incremental motion
- 1.5 and 5mm/sec max. velocity
- 20/50/80N push/pull force
Closed-Loop Servo & Stepper Motor Options
To 0.1µm Resolution, Low Friction, To 50mm/sec, Forces to 400N
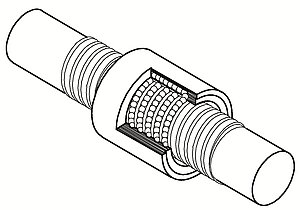
Recirculating ball screw actuators (RBS) have lower friction and can provide higher velocity than lead screw actuators. Ball screws replace sliding friction with rolling friction. Lower friction also means less heat generation when operated at high duty cycles and high velocities. On the other hand, reduced friction also means lower holding forces of the linear actuator when powered off.
Motorized linear actuators with built-in anti-rotation (non-rotating tip) are easier to integrate and when used as pushers, do not generate torque or wear at the contact surface. When long travel ranges, high velocity and long service life are required, rodless linear motor actuators can be the best choice.
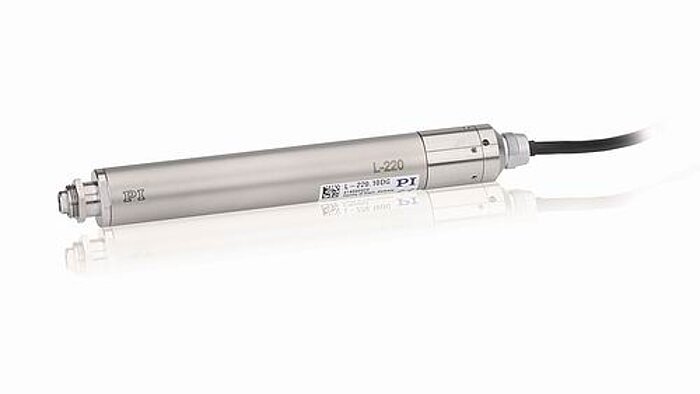
L-220 High Precision Actuators
Servo & Stepper Motors
- 13/26/52/77mm travel
- 0.1µm min. incremental motion
- 20nm sensor resolution
- 3.5mm/sec max. velocity
- 125N push/pull force
- Nonrotating tip
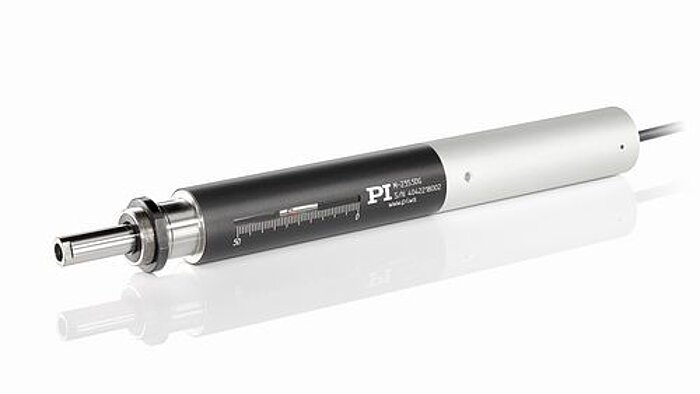
M-235 High Precision Actuators
Servo & Stepper Motors
- 20/50mm travel
- 0.1 & 0.5µm min. inc. motion
- 16 & 500nm sensor resolution
- 2.6 & 30mm/sec max. velocity
- 120 & 50N push/pull force
- Nonrotating tip
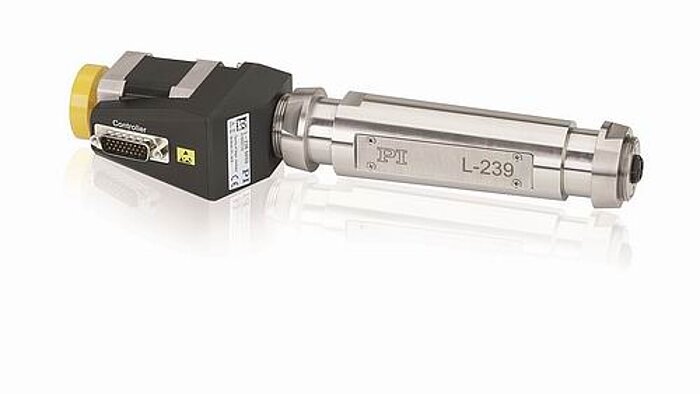
L-239 High Precision Actuators
Servo & Stepper Motors
- 52mm travel
- 0.2 & 0.1µm min. inc. motion
- 50nm sensor resolution
- 50 & 25mm/sec max. velocity
- 300N push/pull force
- Nonrotating tip
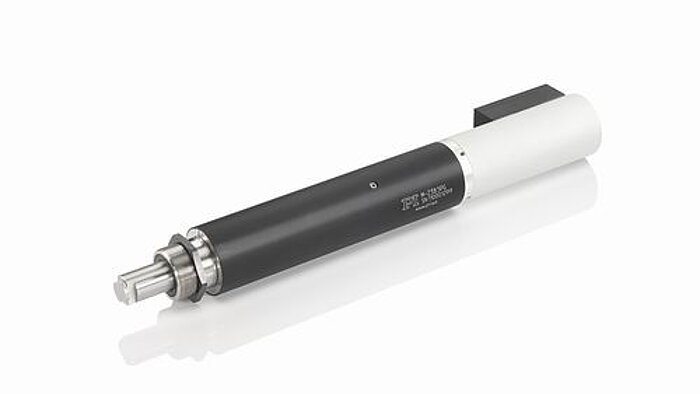
M-238 High Precision Actuators
Servo Motor / Linear Encoder
- 50mm travel
- 0.1µm min. inc. motion
- 0.1µm linear encoder
- 30mm/sec max. velocity
- 400N push/pull force
- Nonrotating tip
Fast Voice Coil Linear Actuators with Mechanical Bearings
Velocity to 750mm/sec, to 20mm Travel, to 20N Force
Voice Coil Actuators are based on a single-phase, brushless electromagnetic linear motor similar to the driver of a loud-speaker. They provide high velocity with zero wear and motion ranges typically up to 1 inch. The V-273/5/7 high-speed, closed loop linear actuator family shown below come with a force sensor option, useful in applications such as switch testing or touch surface sensitivity analysis. The C-413 closed-loop voice coil actuator controller allows on-the-fly switching between force and position mode.
When high-speed linear motion with longer travel range up to 1m or more is required, brushless 3-phase linear motor actuators are recommended.
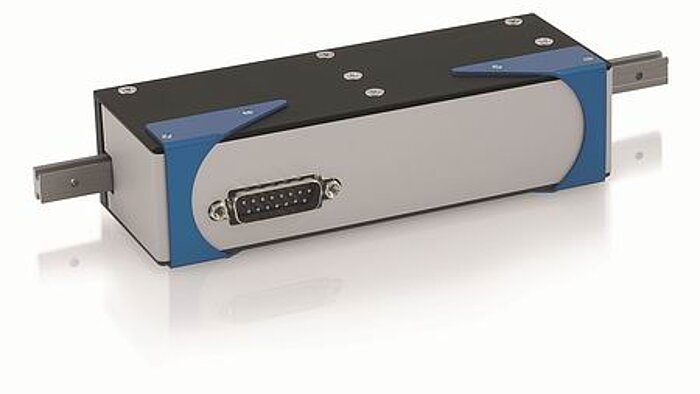
V-273 Voice Coil Actuator
Force Sensor Option
- 20mm travel
- 10nm linear encoder resolution
- 100mm/sec max. velocity
- 6N push/pull force
- 1mN force sensor option
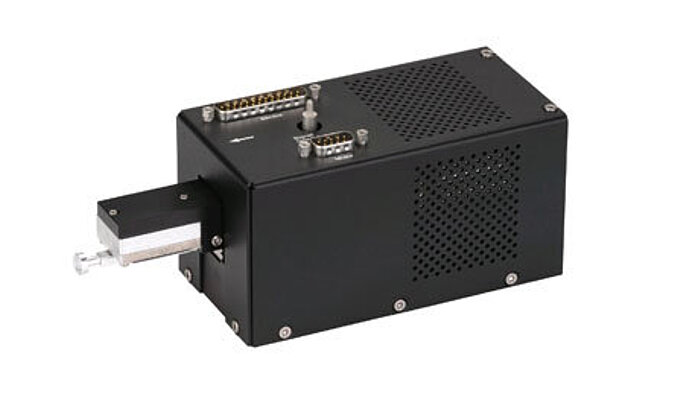
V-277 Voice Coil Actuator
High-Speed, Force Sensor Option
- 15mm travel
- 10nm linear encoder resolution
- 750mm/sec max. velocity
- 20N push/pull force
- 1mN force sensor option
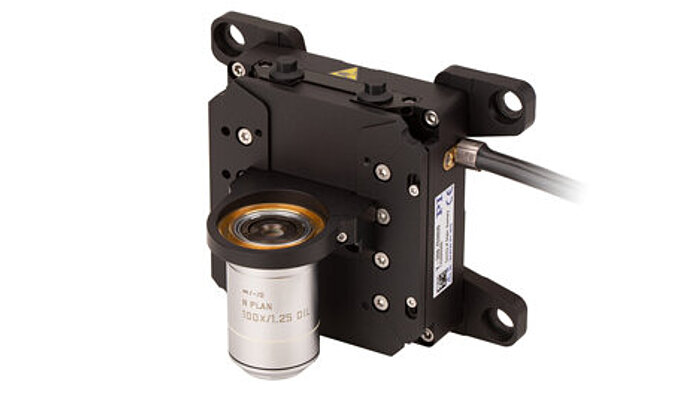
V-308 Fast Nano Focus
Voice Coil Scanner, 7mm
- 7mm motion
- Voice coil linear motor
- Adjustable Z-counterbalance
- Millisecond settling time
- 1nm sensor resolution
Fast Closed-Loop Voice Coil Actuators with Frictionless Air Bearings / Flexures
Zero Wear, Velocity to 1000mm/sec, to 25mm Travel, to 70N Force
These voice coil actuators uses frictionless bearings – either flexures for short travel, or air bearings for extremely straight guiding. Both drive and guiding systems are wear free and clean room compatible.
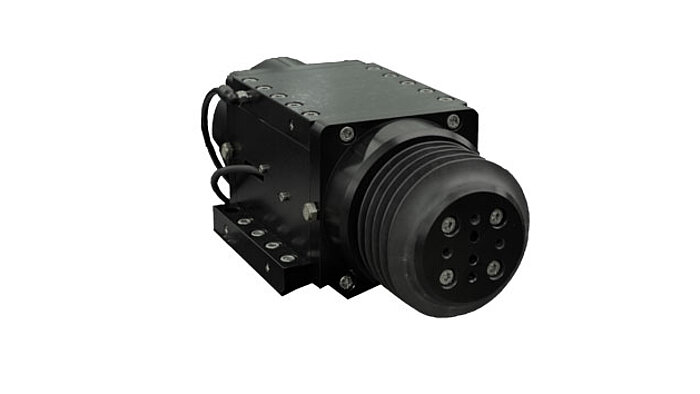
A-131 Voice Coil Positioner
For Fast Scanning/Autofocus
- 1” travel
- Optional bellows
- 1nm resolution
- 8g max. acceleration
PI currently offers several types of long travel piezo linear motors and several types of short travel actuators such as flexure actuators, stack actuators, and bender actuators. The drive principle in piezo ceramic motors / actuators is intrinsically nonmagnetic and vacuum-compatible.
Piezo Motor Linear Actuators
Stick-Slip Ratchet Type Piezo Motor Linear Actuators (Screw Drives) are often used for set & forget type adjustments, replacing manual micrometers. They provide high resolution and holding forces, but low speed typically on the order of a few mm/minute.
Stick-Slip Direct-Drive Piezo Motor Linear Actuators (Mini-Rod Drives) are compact ceramic linear motors with forces to 10N and speed to 10 mm/sec.
PiezoWalk® Linear Motor Actuatorsachieve holding forces to 800N and picometer range resolution; however they are more complex and typically used in high-end applications.
For more information on the differences between piezoelectric motors and piezoelectric linear actuators and their applications, refer to the piezo motion tutorial.
Ultrasonic Piezo Motors are characterized by very high speed of 100's of mm/sec and a very compact design.
Learn more on vacuum compatible motorized linear actuators.
Compact, Low Cost Piezo Ratchet Motor Linear Actuators (Micrometer Replacement)
Set & Forget Applications, to 20nm Steps, to 22N Force
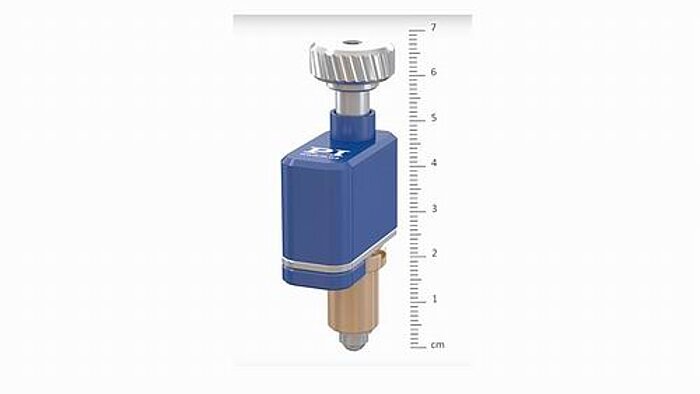
N-472 Closed-Loop PiezoMike
Piezo Ratchet Drive
- <1nm encoder resolution
- ¼” (7mm) motion range
- Self-clamping: Holding force >100N
- Pushing force 22N
- Variety of mounting options
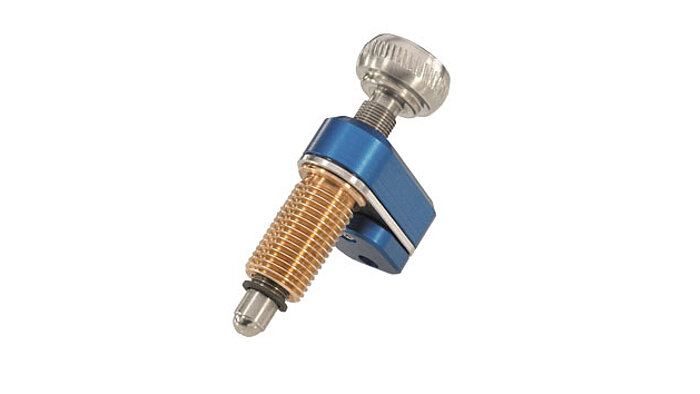
N-470 PiezoMike Micrometer
Piezo Ratchet Drive
- ¼” to 1/2" (7 & 13mm) motion range
- Self-clamping: Holding force >100N
- Pushing force 22N
- 30 nanometer step size
- Variety of mounting options
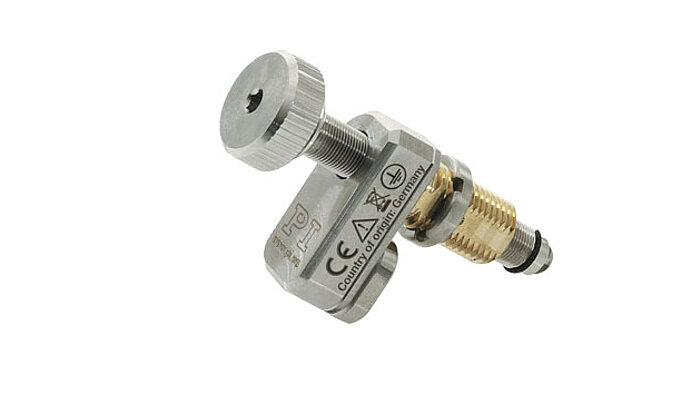
N-470.V/U Vacuum PiezoMike
Piezo Ratchet Drive
- ¼” to 1/2” (7 & 13mm) motion range
- Self-clamping: Holding force >100N
- Pushing force 22N
- 20 nanometer step Size
- Variety of mounting options
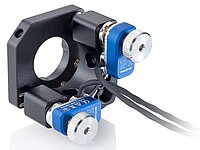
Application Example:
N-480 kinematic mirror mount with N-470 actuators
Low Cost Piezo Motor Linear Miniature Actuators, Mini-Rod Inertia Drive
7N Force, Travel to 35mm, 5mm/sec
These compact, motorized miniature actuators require some kind external position feedback – the inertia motors provide linear motion with high resolution, but w/o an internal sensor exact position information is not provided. Unlike conventional stepper motor actuators, the step size in piezo inertia motor actuators is not equidistant.
Captive Actuator and Non-captive Actuator Miniature Actuator Versions
The N-422 is a non-captive compact actuator design with the shaft running through the linear motor, providing longer travel linear motion. The N-412 is a captive miniature actuator..
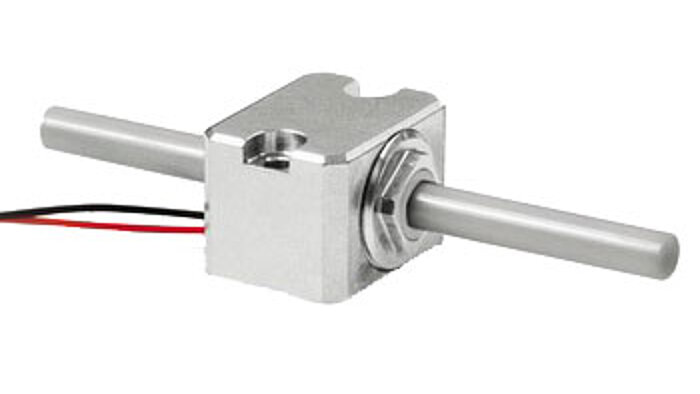
N-422 OEM Piezo Motor Actuator
Direct Drive Piezo Inertia Motor
- 35mm travel
- 0.3µm step size
- 5mm/sec max. velocity
- 7N push/pull force
- 10N holding force
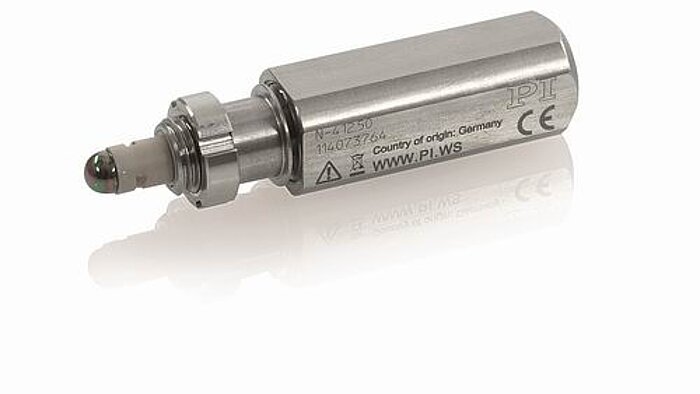
N-412 Piezo Motor Actuator
Direct Drive Piezo Inertia Motor
- 13mm travel
- 0.3µm step size
- 5mm/sec max. velocity
- 7N push/pull force
- 10N holding force
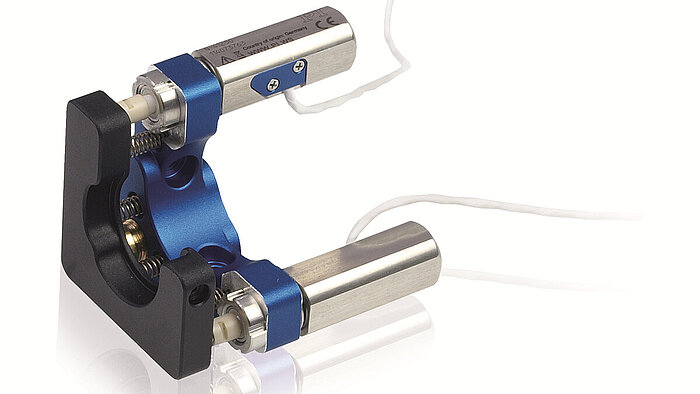
Application Example: N-412 actuators on a kinematic mirror mount
The operating principle of a PiezoWalk® linear motor actuator is similar to the principle of biological walking. Motion is generated through a succession of coordinated lift/forward/drop cycles of two or more “legs”. Each cycle can be controlled to provide steps from a few picometers to a few microns of linear motion. With repetition rates of up to 100’s of steps per second, continuous linear motion up to 15mm/sec can be achieved. These drives are preloaded, self-clamping and achieve exceptional life times. PI offers open-loop and closed-loop PiezoWalk linear motor actuators.
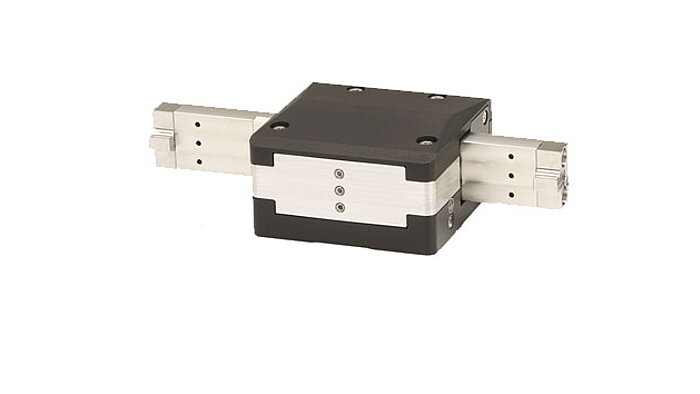
N-331 V8 PiezoWalk® Actuator
V8 Drive: Higher Force & Speed
- 25 to 100mm travel
- 0.02nm open loop resolution
- 15mm/sec max. velocity
- 50N push/pull force
- 5nm encoder integrated
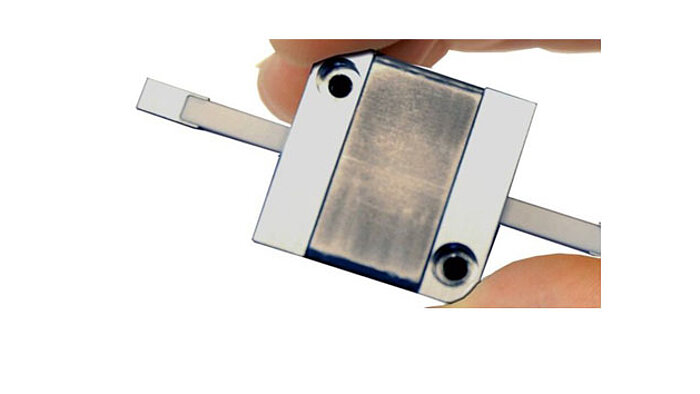
N-310 PiezoWalk® Linear Actuator
Miniature OEM Actuator
- 31010 to 125mm travel
- 0.03nm open loop resolution
- 10mm/sec max. velocity
- 10N push/pull force
- Use w/external position feedback
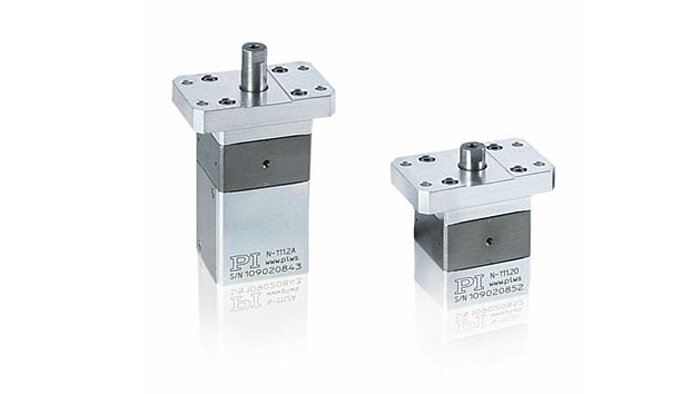
N-111 PiezoWalk® Linear Actuator
Medium Force, Encoder Option
- 10mm travel
- 0.03nm open loop resolution
- 1mm/sec max. velocity
- 50N push/pull force
- 5nm encoder integrated
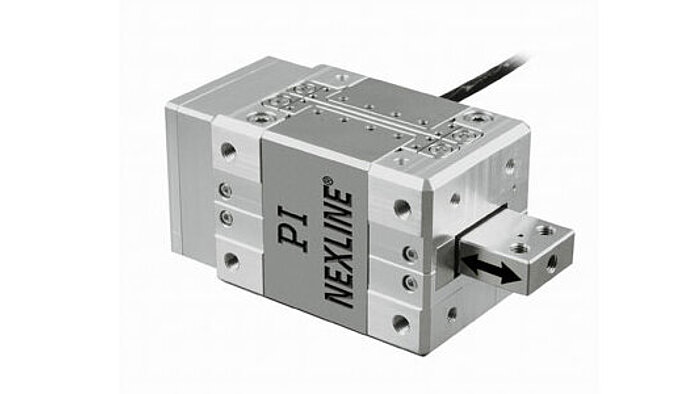
N-216 PiezoWalk® Linear Actuator
High Force, Encoder Option
- 20mm travel
- 0.03nm open loop resolution
- 1mm/sec max. velocity
- 600N push/pull force
- 5nm encoder integrated
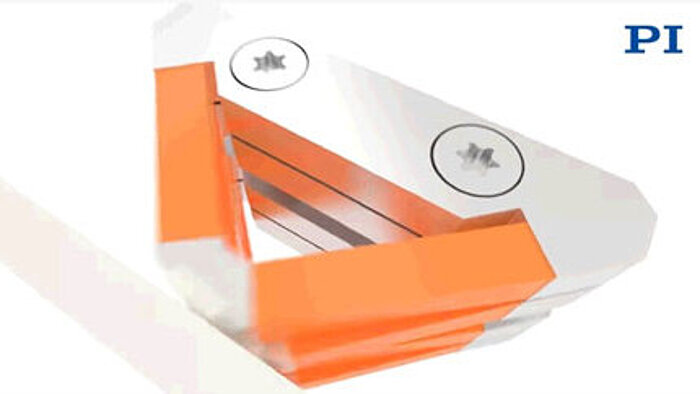
Animation: V8 Piezo Motor with Nanometer Precision
"Honey, I shrunk the V8 Engine!"
PI's PICMA-Walk V8 Piezo Linear Motor - Power, Reliable, Precise
Ultra-High Resolution & Speed Amplified Piezoelectric Linear Actuators
For Fast Step & Settle or Dynamic Scanning Applications, Sub-nm Resolution, up to 1mm Travel
Amplified piezo flexure linear actuators provide friction free linear motion with sub-nm resolution and very fast response (millisecond and below). These types of linear actuators are used when short travel motion with extremely high precision and maintenance-free, virtually unlimited service life, is required.
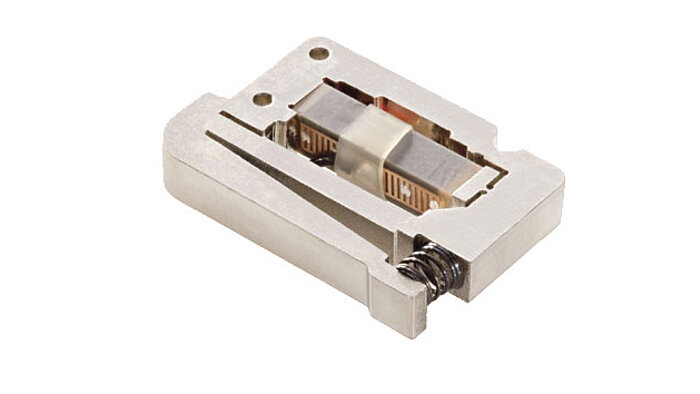
P-604 Low-Cost, Piezo Flexure Actuator
300µm Motion, Flexure Guided
- 300µm travel
- Cost-optimized for large quantities
- Lightweight construction, only 4 grams
- Flexure guided = Frictionless & straight motion
- Small footprint of 13x20mm
- PICMA® long-life piezo actuator
- For OEM instrumentation
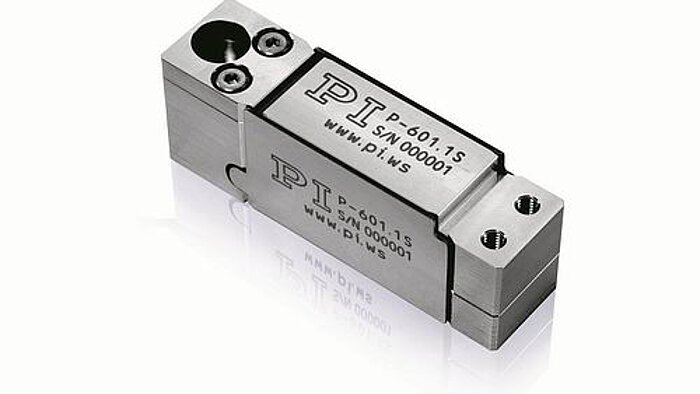
P-601 Piezo Flexure Actuator
Closed-Loop Option
- 100, 250 and 400µm travel
- Position sensor option for closed-loop operation
- Flexure guided = Frictionless & straight motion
- High dynamics and stiffness
- PICMA® long-life piezo actuator
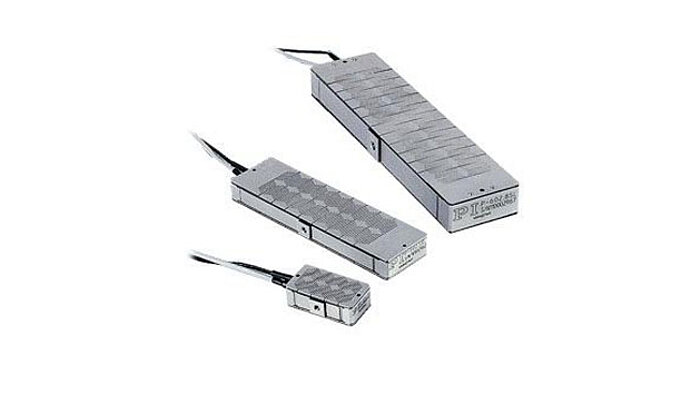
P-602 Piezo Flexure Actuator
Motion to 1mm, High Force
- Up to 1mm travel
- Position sensor option for closed-loop operation
- Flexure guided = Frictionless & straight motion
- To 400N force, high stiffness & dynamics
- PICMA® long-life piezo actuator
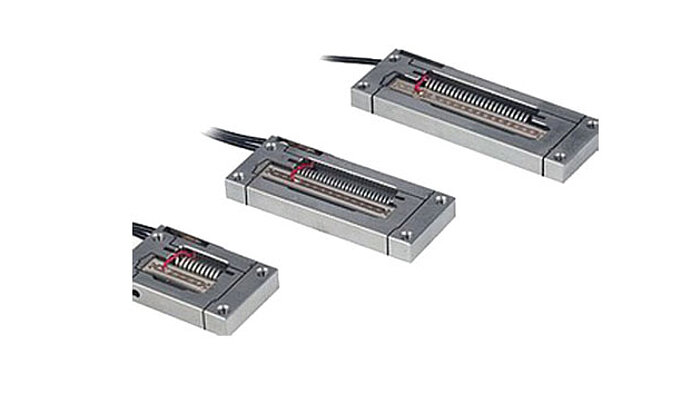
P-603 Piezo Flexure Actuator
Motion to 500µm
- 100, 300 and 500µm travel
- Position sensor option for closed-loop operation
- Compact, cost-effective design
- Flexure guided = Frictionless & straight motion
- High dynamics and stiffness
- PICMA® long-life piezo actuator
Ultra-High Resolution Closed-Loop Piezoelectric Stack Linear Actuators (Short Travel 15 to 180µm)
Forces to 30kN+, Sub-millisec Response, Sub-nm Resolution
These closed-loop precision linear actuators provide high forces, high stiffness, and very fast response in the sub-millisecond range, with displacement typically in the 100µm range.
Applications: biotechnology, nano-dispensing, microfluidics, valve control, fast switching and nanopositioning, optics, medical-devices, life-sciences
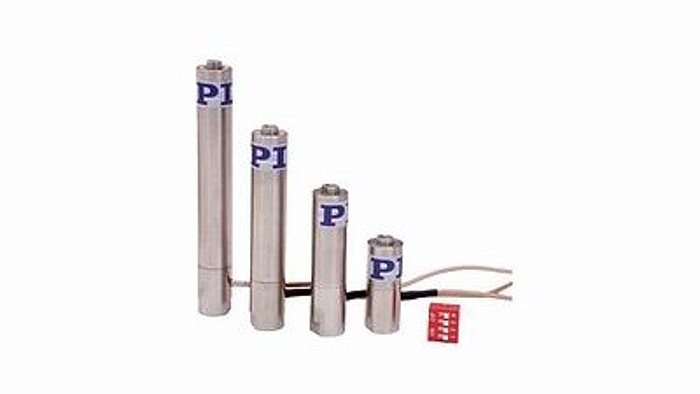
Piezo Stack Actuators
- Very high force & stiffness
- Sub-millisec response
- Many different designs
- Sub-nanometer resolution
- Learn more….
What is a Linear Actuator?
A linear actuator, sometimes referred to as a pusher, is a device that provides motion in one degree of freedom, however mostly unrestrained, in contrast to a linear stage which also comes with a guided platform. Here we are focusing on motorized precision actuators.
Linear Actuators Buyers Guide
There are many different types of linear actuators, consider the following factors when buying a motorized precision linear actuator:
- Drive Type: Motorized linear actuators are available with stepper motors, voice-coil motors, piezo motors, with closed-loop position feedback for highly precise and repeatable motion, with direct-drive motors for higher speed, and screw drives for higher force. See examples and specifications of representative models on this overview page above to give you a basic understanding of capabilities and limitations.
- Push/Pull Force, Stiffness, and Size: Consider the mass, size, and inertia of the object that the linear actuator will need to move. Do you have an external guiding system or will the actuator have to provide precision guidance, too? An actuator with a higher load capacity will provide a longer lifetime, especially in high duty cycle applications.
- Drive Mechanism / Bearing Type: In general, ballscrews provide higher velocity and lower friction, but unlike leadscrews lack self-braking capability, which might be important in vertical applications. Piezo-motor actuators are compact, provide self-locking capabilities, and extremely high resolution but require different drivers than simple stepper-motor-driven actuators. Air bearing actuators provide the highest accuracy and lifetime, as well has the best controllability for extremely small forces since they are friction-free and maintenance-free.
- Travel Range: This refers to the total displacement the actuator can provide. Here, screw type actuators provide the longest travel ranges, while piezo stack actuators or flexure actuators are friction free and provide very fast response times to the sub- millisecond range, but travel ranges are limited to the low millimeter range. Piezo-motor actuators, such as the Piezowalk actuators, can provide 100mm or more and forces to 800N. Voice coil actuators are used for highly dynamic scanning or step-and settle applications with typical travel ranges of 25mm or less. They also need weight force compensation in vertical applications such as the V-308 fast focus actuator.
- Acceleration and Speed: Higher velocity and acceleration can be achieved with direct-drive motors (voice-coil, three-phase linear motors, ultrasonic piezo motors). Lead-screw or ballscrew actuators can provide higher force. The motor size and motion controller will have a big influence on step-and-settle performance.
- Accuracy, Repeatability, and Resolution: Actuators with integrated linear encoders provide the highest repeatability and accuracy compared to open loop stepper motor actuators or motor mounted rotary encoders. Piezo stack actuators and amplified actuators provide the best dynamics and precision, however with limited travel ranges.
- Environmental Compatibility: Vacuum compatible actuators require careful designs with reduced outgassing. Air bearing actuators are ideal for clean rooms, and since frictionless, can virtually run forever without maintenance.
- Support and Warranty: Check the level of technical support provided by the manufacturer, as well as the warranty terms. Always discuss your actuator requirements with a knowledgeable engineer at the manufacturer or supplier to ensure you choose the most suitable linear actuator for your application.
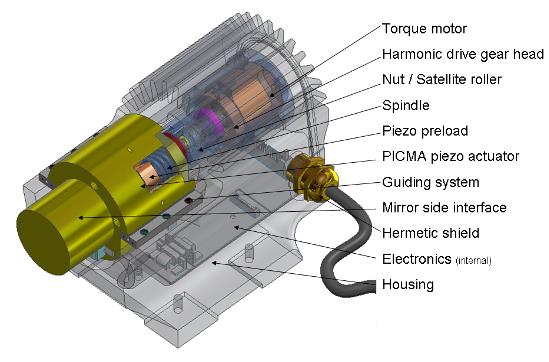
High performance precision linear actuators can be customized for force, speed, resolution and travel length to suit varying applications - like adjusting 798 quarter ton segments in the primary mirror of the Extremely Large Telescope (ELT) with nanometer accuracy in the extreme environment of the Chilean Atacama Desert, with a hybrid actuator design. More information
Precision actuators find applications in various industries and fields where accurate and controlled motion is required to test, measure, and automate processes. Some common applications include:
- Semiconductor and Electronics Manufacturing: Precision actuators and stages play a crucial role in semiconductor and electronics manufacturing processes. They are used in automating wafer handling, die bonding, wire bonding, and inspection equipment to ensure precise positioning, alignment, and manipulation of delicate electronic components.
- Optics and Photonics, Astronomy: Precision linear actuators and stages are essential in the field of optics and photonics. They are used in optical systems, lens positioning, beam steering, and mirror tilting applications. They enable precise adjustment and automated alignment of optical components for accurate light control and beam manipulation.
- Microscopy and Imaging: Precision linear actuators and stages are utilized in microscopy and imaging systems for precise positioning and scanning of samples. They enable high-resolution imaging, sample manipulation, and autofocus capabilities in various microscopy techniques such as confocal microscopy and scanning electron microscopy (SEM).
- Aerospace and Defense: Precision linear actuators and stages are essential in aerospace and defense systems. They are used in aircraft control surfaces, antenna positioning, satellite mechanisms, and missile guidance systems to ensure accurate and reliable motion control in critical operations.
- Robotics and Automation: Precision automation actuators are widely used in robotics and automation systems for precise and repeatable motion control. They are employed in robotic arms, grippers, and manipulators to enable precise positioning, gripping, and assembly tasks.
- Medical and Healthcare: Precision linear actuators and stages play a vital role in medical and healthcare applications. They are used in medical devices, surgical robotics, prosthetics, and patient positioning systems to enable precise movement, manipulation, and control for surgeries, diagnostics, and patient care.
- Laboratory Automation: Precision actuators and stages are utilized in laboratory automation equipment for precise liquid handling, sample positioning, and automation of laboratory processes. They ensure accurate and repeatable motion control for efficient and reliable laboratory operations.
- Research and Development: Precision linear actuators and stages are commonly used in research and development settings. They find applications in experimental setups, material testing, and scientific instruments where precise positioning and control are required for data collection and analysis.
With a global growing need for more precision in automation and manufacturing, the demand for higher accuracy actuators keeps increasing across all industries where precise motion control is essential.