Precision positioning and automation applications widely rely on high-performance motion stages and motion controllers. When it comes to developing a next generation machine or process, motion system designers often ask the question whether to employ mechanical bearings or air bearings. Mechanical bearings such as crossed-roller bearings, and recirculating ball bearings are widely used in precision motion control and positioning applications and are a good choice in most cases. However, in scenarios where parameters such as lifetime, particle generation, reproducibility, angular accuracy, runout, straightness, and flatness are critical, air bearings are superior and deserve a closer look.
Air bearings use a thin film of pressurized clean air or gas to support the load, very similar to the principle of an air hockey table. There is no contact between the static and moving part of the bearing since the pressurized gas creates a layer separating both. There are two basic types of air bearings: porous media bearings with millions of sub-micrometer sized holes and bearings with small, integrated orifices. In both cases, the air bearing designers need to achieve a uniform pressure across the entire bearing area.
Air bearing surfaces are precision-ground to the highest tolerances and hard coated. Since they do not come into contact (modern controllers with pressure reservoirs and switches shut down the motion in case of a pressure drop), they avoid traditional bearing issues such as friction, tribological wear, and relubrication. As a result, air bearings provide significant advantages in high-velocity motion applications and precision positioning, especially in 24/7 automation applications with high uptime and reliability requirements.
1. Maintenance-Free, Virtually Unlimited Lifetime, Clean Room Compatible: Since air bearings work without mechanical contact between components, they do not require maintenance, periodic inspections or relubrication cycles. There is also no cage migration issue known from cross roller bearings. And the systems are ideally suited for clean room applications.
2. True-Planar Motion XY and XY-Theta Motion Designs Feasible: Multi-axis stages with mechanical bearings usually stack one axis on top of another. This is a straight-forward approach but has several disadvantages. As the upper axis moves to the extremes, it will generate torque loads on the lower axis leading to geometric errors. In air-bearing designs, fully planar XY and XY-Theta positioning systems are feasible, where all degrees of freedom reference to the same base plane.
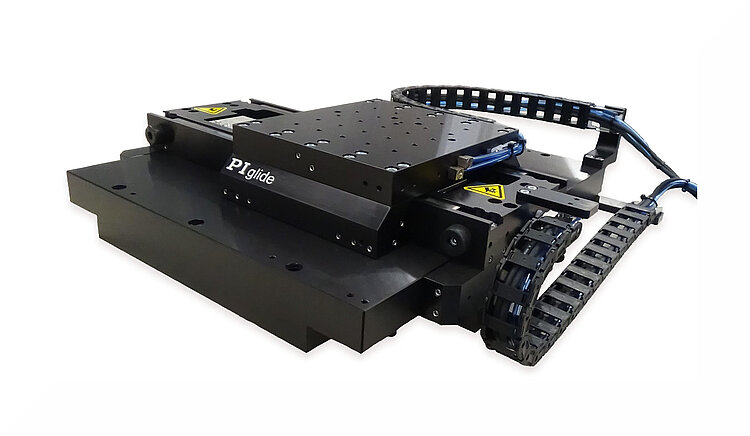
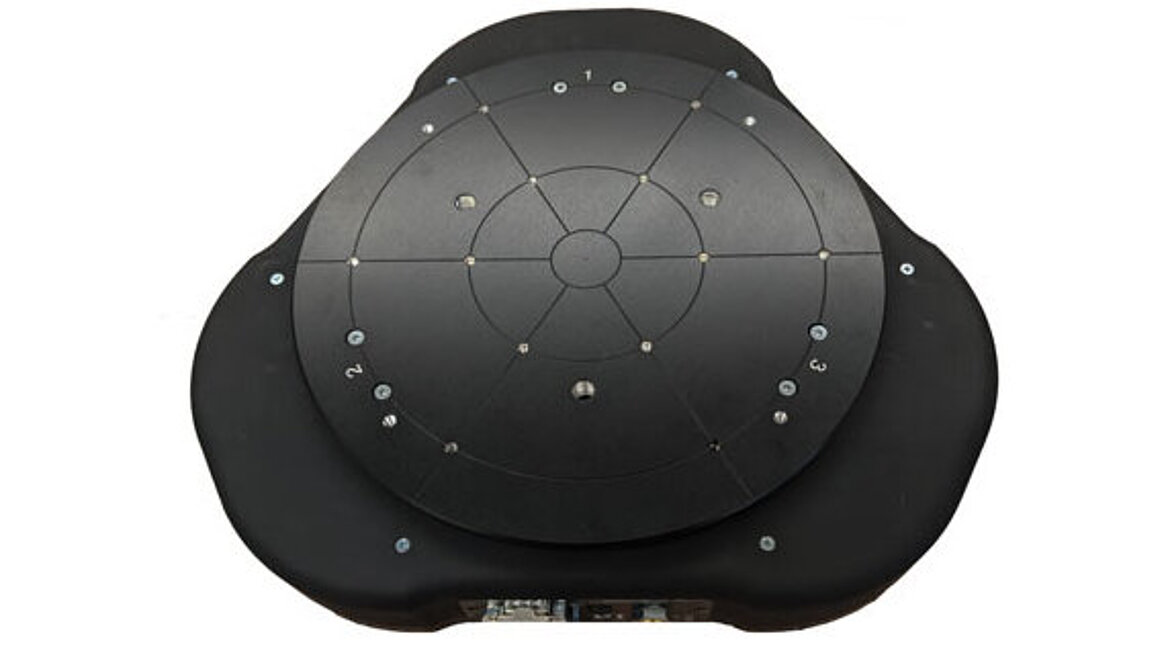
3. Vibration-Free, High-Speed Motion with Highly Constant Velocity: The fluid film in air bearings can readily accommodate high velocity, and some air bearings can even improve efficiency at high speed, due to aerodynamic lift effects. Certain processes and experiments, such as semiconductor wafer scanning, 3D tomography, and inertial sensor testing, demand constant motion at precisely controlled speeds, without bearing rumble. In these instances, air bearing systems are the most appropriate solution to provide the necessary continuous motion at precisely controlled speeds, and they generally last longer than mechanical bearings.
4. Frictionless Motion and Positioning with Very High Accuracy: In linear motion applications, precise positioning of a moving carriage within nanometers is achievable by employing a direct-drive motor and high-resolution encoder supported by an air bearing. For rotational applications, angular resolutions to tenths of arc-seconds are achievable. Air bearings are often preferred in many inspection, metrology, and manufacturing applications due to their minimal hysteresis effect or reversal error, which arises from reduced mechanical contact and friction. The elimination of friction makes it possible to minimize in-position hunting and improve resolution capabilities significantly. Although flexure guided piezo stages can achieve comparable precision, they are limited to much smaller travel ranges.
5. Motion with Extreme Straightness and Flatness, Minimal Geometric Errors: Air bearings offer high accuracy, owing to the excellent quality manufacturing of their components. Linear air bearings feature exceptionally flat and straight travel with minimal roll, pitch, and yaw errors. Air bearings are highly suitable for manufacturing and measurement processes, providing excellent repeatability of the same procedure and the ability to compensate for deviations from the ideal trajectory. Many current semiconductors have tolerances of just single-digit nanometers, and some components in the latest automotive engines require submicron precision. For precision machining and optics inspection, air bearings provide repeatable part quality and measurement reliability.
6. Travel Ranges of 1m and More Are Feasible:Another frictionless drive technology often used in nanopositioning applications is from amplified piezoelectric actuators and flexure guiding mechanisms. Here, the maintenance free advantages of air bearings also come into play. However, while piezo flexure stages can provide even faster response and higher resolution than air bearings their motion ranges are limited to typically under 1mm.
7. Rotary Motion with Minimal Eccentricity and Wobble: Rotary air bearings are highly effective in providing precise rotary motion due to their exceptional stiffness. In rotary stages, wobble or tilt errors typically occur within the range of 0.1 to 1 arc-second. Compared to most mechanical bearing solutions, errors caused by wobble, axial and radial motions are much smaller.
Blog Categories
- Aero-Space
- Air Bearing Stages, Components, Systems
- Astronomy
- Automation, Nano-Automation
- Beamline Instrumentation
- Bio-Medical
- Hexapods
- Imaging & Microscopy
- Laser Machining, Processing
- Linear Actuators
- Linear Motor, Positioning System
- Metrology
- Microscopy
- Motorized Precision Positioners
- Multi-Axis Motion
- Nanopositioning
- Photonics
- Piezo Actuators, Motors
- Piezo Mechanics
- Piezo Transducers / Sensors
- Precision Machining
- Semicon
- Software Tools
- UHV Positioning Stage
- Voice Coil Linear Actuator
- X-Ray Spectroscopy